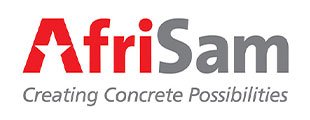
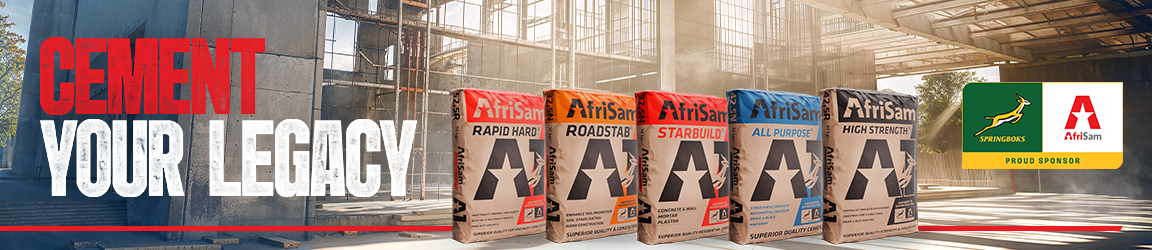
AfriSam exploring ways to further reduce its carbon emissions
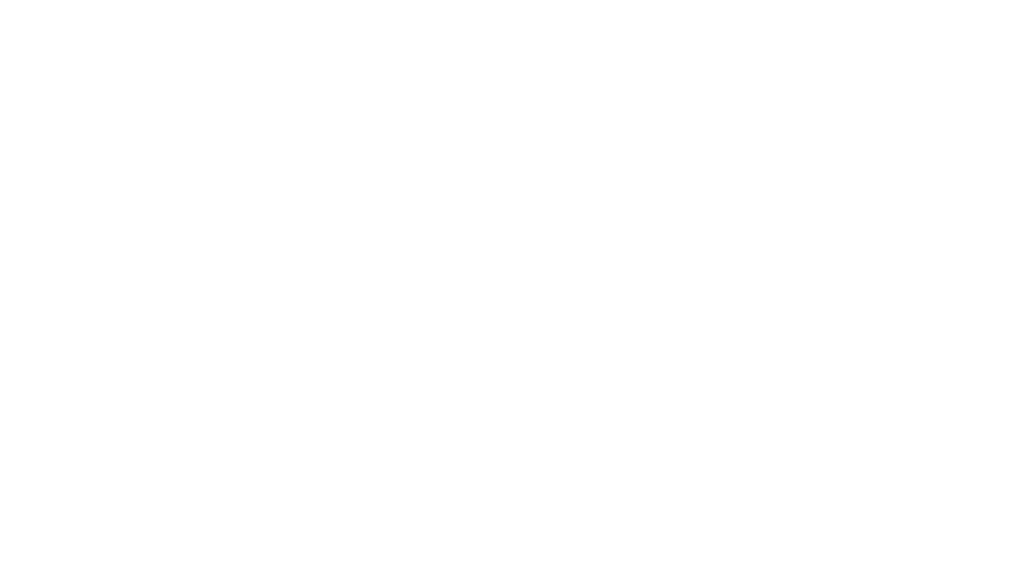
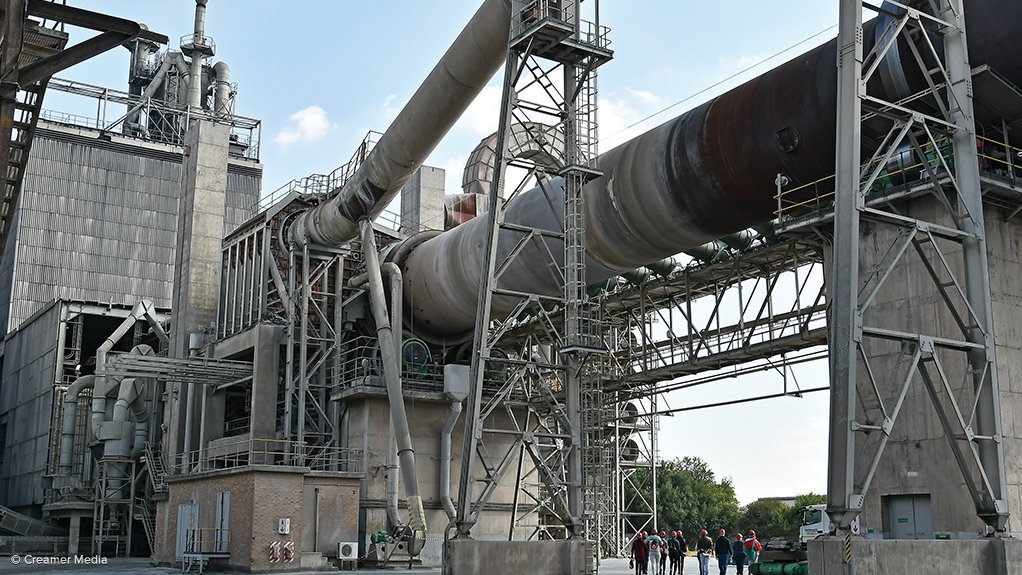
LIMESTONE KILN Producing clinker is energy intensive and releases CO2 over and above the fuel used to burn the limestone
Photo by Dylan Slater
Diversified materials company AfriSam is working to further reduce its carbon emissions, after achieving a sustained reduction of 35% as a result of various initiatives over nearly two decades, says AfriSam Cementitious executive Hannes Meyer.
During a media tour of the clinker production plant at the Dudfield cement plant, in the North West, the company outlined some of its plans to reduce the carbon intensity of the cement process, but, nevertheless, highlights that greater efficiencies are ever-more difficult to reach.
The company is exploring capturing and using the waste heat from its kiln, but this would require a significant investment.
Besides using coal to fire the kiln, a further challenge to reduce carbon dixoide (CO2) emissions is that the endothermic chemical reaction to form the main ingredient of clinker, quicklime, from limestone, releases CO2. The company already meets European Union standards for sulphur dioxide emissions and also emits less than 30 mg/m3 of particulate matter.
“The process of making cement is very energy intensive and about 786 kg of CO2 is released per ton of clinker produced,” explains Meyer.
Overcoming this challenge requires innovative solutions, including exploring alternative means to reduce carbon intensity. As with most cement producers, AfriSam uses preheaters and precalciners before the limestone is burned. The energy intensity means that renewable-energy sources are rarely suitable to replace coal as the primary energy source.
Alternative fuel sources, such as waste tyres, also release CO2 and the chemical composition of the fuel must be factored in prior to production. This means that the company cannot change from one fuel source to another quickly because the feedstock buffers, including the chemical composition of the buffers in relation to that of the fuel, must be prepared for the fuel used in the furnace.
“We cannot stop building infrastructure, but we can get better performance from cement. This is what we have been successfully achieving. The next phase of reducing our carbon intensity is assessing electricity offset and using the cement produced more effectively.”
AfriSam uses cement extenders – additives that change the properties of the cement – to reduce the carbon intensity of the final product to build infrastructure, while improving or adding to the performance of the cements.
Meyer, who holds a master’s degree in chemistry, adds that the company is also considering the deployment of logistics best practices to reduce carbon intensity, such as trying to source suitable materials as close to the point of use as possible. This is in keeping with client demands to adhere to the highest environment-friendly practices possible by reducing the climate impact of logistics and supply chains.
Meanwhile, the introduction of carbon taxes in South Africa, albeit through an introductory phase, poses economic and commercial challenges for the industry. The fact that CO2 emissions are unavoidable means that the industry has no option but to pass on this additional cost, notes AfriSam sales and marketing executive Richard Tomes.
However, AfriSam has already estimated the impact on the prices of the range of cement and readymix concrete products and has communicated the prices to clients. The price increases are benchmarked against the current carbon tax rates, which will increase by inflation plus 2% each year until December 2022.
“The idea is to incentivise customers to make more environmentally responsible choices.
“Composite cement, which is cement with various extenders to meet the required need, is the most relevant answer for us to reduce our environmental impact. We are also looking at using waste products from other industries that contain the cementitious chemicals and chemical properties that we use in our products,” says Tomes.