Alcohol testing a priority for mines
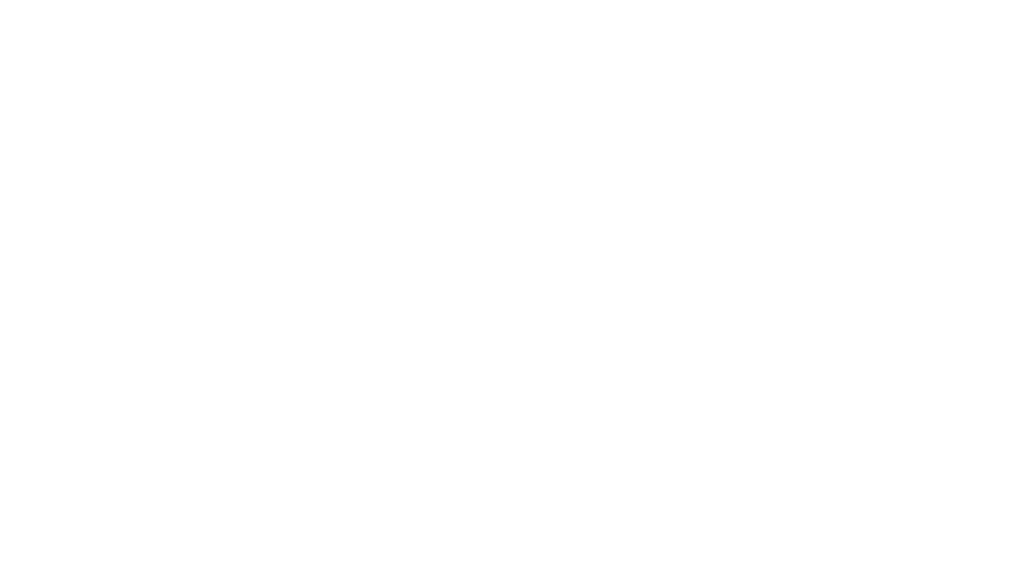
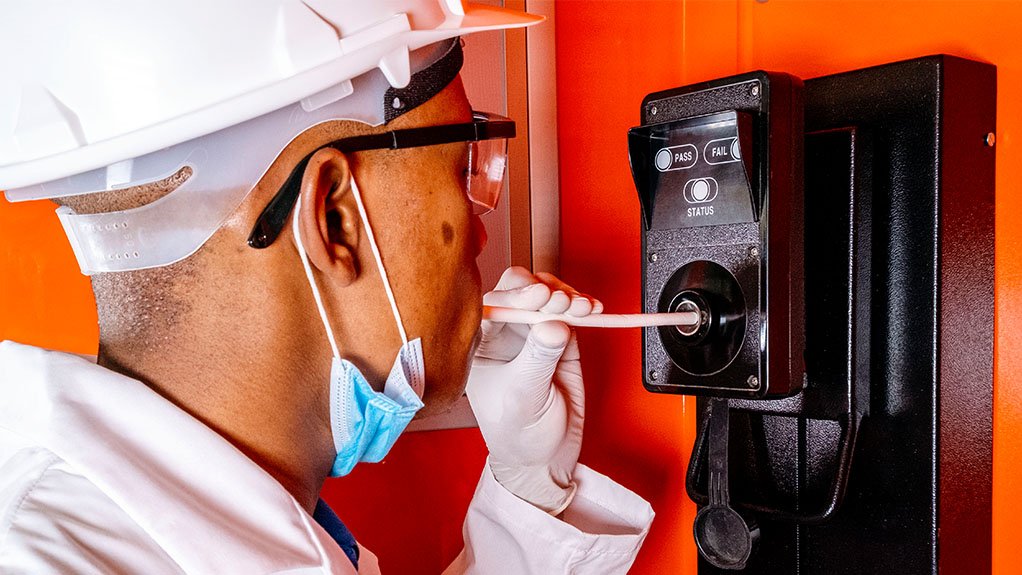
ENTRANCE BREATHALYSER SYSTEM An underground miner uses Alcohol Breathalysers' EBS0101 entrance breathalyser before entering the mine to ensure their fitness for hazardous work
It is a top health and safety priority to ensure that mineworkers do not enter mines after having consumed any alcohol, or with any alcohol remaining in their blood the day after consumption, as this can inhibit their ability to work safely.
Alcohol Breathalysers is a specialist business that was established in 2004 to supply alcohol breathalyser equipment to the mining sector to enhance the safety in those working conditions, as well as to a variety of other industries that require the sobriety of employees while they are at work.
A mineworker who enters a mine under the influence of alcohol can cause harm or death to themself or others, and can also harm other mineworkers, potentially impacting on a mining company’s ability to operate; while the risks and consequences can result in serious legal implications.
The consequences of noncompliance with the Mine Health and Safety Act can be severe for both mining companies and mineworkers, says Alcohol Breathalysers director Angus MacArthur.
He emphasises that mandatory breath alcohol testing for all employees should be carried out at all entrance points to mines – both pedestrian and vehicular, as well as at various other high risk internal points, adding that anyone who tests positive for alcohol at any breath alcohol concentration should be denied access for at least a period of one hour and thereafter until such time the employee tests negative for alcohol.
The time frame for retesting after a first initial positive breath test depends on company policies in place and on the human resource capabilities of individual companies operating in the mining environment.
Equipment Maintenance
“Due to the high number of breath tests that would be conducted with any given breathalyser unit, it is imperative that the equipment used in the mining environment be regularly serviced to ensure that the breathalysers continue to provide accurate test results and function optimally,” notes MacArthur.
The number of breathalysers required and the respective service intervals depend on the size of the workforce, as well as on the number of tests conducted on a daily basis. For example, one breathalyser used for a smaller workforce of 50 to 100 employees would require yearly calibration, whereas for larger workforces of 500 to 1 000 employees more breathalysers would be required at a ratio of at least one unit to every 100 employees, so that yearly calibration can be facilitated.
Equipment should not be overburdened. When budget constraints are effected and higher volume testing takes place on a fewer number of breathalysers, MacArthur notes that equipment may require maintenance at six-monthly intervals, whereby more regular checking of breathalysers will be advised between calibration intervals to ensure that equipment remains in good working order.
Alcohol Breathalysers offers both a comprehensive calibration service in-house and also supplies fully replaceable interchangeable sensors for the Entrance Breathalyser System EBS010, which enables easy exchange of old internal sensors with new calibrated sensors, avoiding any downtime of breathalysers at mines.
MacArthur regards mine health and safety as a top priority, and for this reason he not only sees to the provision of high-quality breathalysers for industrial use, but also encourages the relevant upkeep and maintenance of the equipment.
Using breathalyser technology is of paramount importance for mining companies for risk reduction and to ensure that mineworkers are fit and safe for operations at all times, thereby contributing to the mining industry’s ambition to achieve zero harm.
Insufficient measures to ensure the safety and sobriety of mineworkers can have fatal implications for mineworkers and damaging effects on mine infrastructure, equipment and operations, concludes MacArthur.