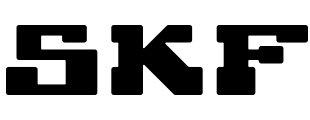
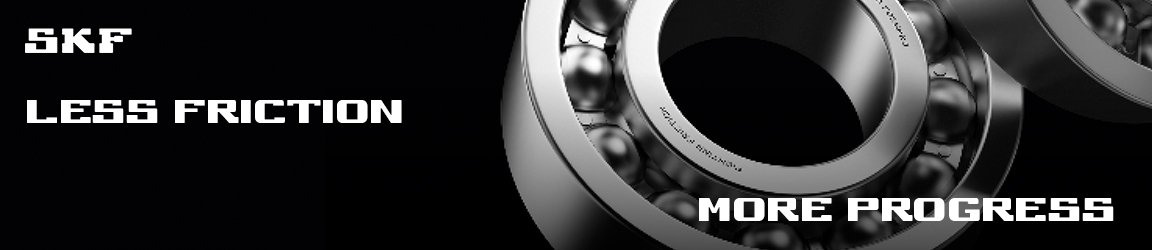
Automated machine health monitoring improves efficiency
The ever-increasing demand for consumer goods means that machinery on mines and in manufacturing plants are required to operate more effectively, consistently and with a longer lifespan.
“In order to achieve maximum production and overall plant optimisation, operators are demanding more from their heavy industrial machines and equipment, which are expected to run ultra-reliably and perform better and more efficiently for longer, while paying close attention to safety and environmental compliancy,” states SKF Connected Technologies manager John Storm. “Given that machines and equipment typically operate in stringent environments, condition monitoring and regular maintenance go hand in glove in achieving the trio of high performance, availability and reliability. Manual monitoring by technicians using portable devices is time consuming and counter-productive, sapping resources and compromising worker safety.”
He asserts that switching from a manual to an automated machine monitoring system and data collection process, the availability of rotating equipment will increase, enabling the optimisation of operations.
SKF Enlight Collect IMx-1 vibration and temperature sensors are designed to automatically monitor the condition of rotating parts, enabling operators to collect critical data on machine and equipment health. The use of automation technology means fewer technicians are required and a safer working environment can be created. In addition, more frequent data collection enables early problem detection and machine failure prediction, allowing operators to carry out preventative maintenance, helping to reduce costly unplanned downtime and maintenance costs, increasing machine life cycles and optimising asset reliability.
SKF explains that the IMx-1 system relies on a ‘mesh network’ which allows sensors to relay data between each other, enabling data to be routed around radio obstacles such as pipework. The mesh network is engineered to be self-forming, which means the system is quicker and easier to deploy compared to wireless systems such as Wi-Fi or Bluetooth. In addition, the way in which the system handles bandwidth and the sensors’ power consumption, leads to a long battery life.
The battery-powered sensors are said to be compact and easy to install and are designed to enable operators to build an automated machine monitoring system powered by Cloud-based Internet of Things solutions and AI-driven analytics. Mounted to a bearing housing, the IMx-1 sensor forms a scalable network, wirelessly detecting and processing common and critical health data from rotating assets including unbalance, misalignment, high temperatures, looseness, electrically induced vibration and early stage damage to bearings and gears.
An IP69K ingress protection rating makes the system particularly suited for harsh industrial conditions, offering protection against exposure to elements such as dust, dirt, oil, grease, contaminants, flying debris, temperature changes, wind, rain, and high-pressure hot water wash-downs.
SKF Enlight Collect IMx-1 is available on a fee-based contract, aimed at helping operators achieve goals of high machine availability, increased productivity, improved safety and reduced environmental impact of plants.