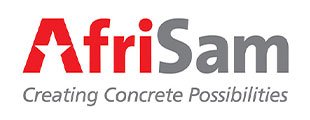
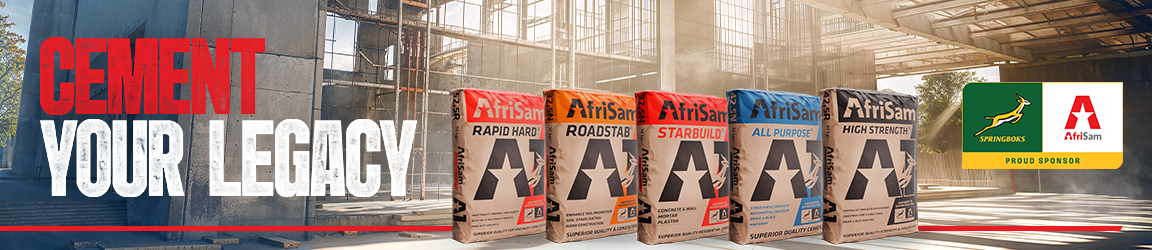
Producer achieves 35% emission reduction, supports carbon tax
Construction materials supplier AfriSam has reduced the company’s carbon emissions, a ton of cement produced, by 35% from 1990 to 2018 and is focusing on further carbon reductions, sustainability and the implementation of the carbon tax in South Africa.
“The 35% is close to the targets being mentioned now and we’ve already achieved that. We’ve also managed to achieve cost savings while driving down carbon emissions,” states AfriSam cementitious executive Hannes Meyer.
He claims that AfriSam has focused on optimising two of the biggest contributing processes to carbon emissions from cement producers – cement thermal consumption and cement production processing.
“You need to liberate carbon dioxide from your limestone material, but you need energy for that, and that’s the second-biggest source of emissions, we’ve reduced 31% of our thermal consumption for every ton of cement that we have produced from 1990 to 2018,” he states.
Meyer highlights the development of cement kilns and its contribution to energy savings and carbon reduction. Traditionally, cement production was started in wet process kilns, which uses a slurry. These kilns used more than double the energy that kilns use currently, but not many of these kilns are operational today elsewhere in the world and, in South Africa, there are none, he explains.
Subsequently, the next generation of kilns, referred to as dry process kilns, were manufactured to be longer in length and introduced with a fine powder in the vacuum of the kiln. This resulted in significant improvements in energy use when compared with the wet process kilns, as the dry process is more thermally efficient.
This is because wet process kilns used slurries, which contained about 40% water. The water had to be evaporated, which required a lot of energy.
Heat transference is also more efficient in a dry process kiln.
“The next stage of improvement was to introduce a set of preheating cyclones, and as a next step, also a precalciner, in these kilns. You can also add a precombustion chamber,” Meyer states.
This would result in even greater efficiency in the heating process and, therefore, greater energy and fuel efficiency, he adds.
While highlighting the importance of these advancements in terms of enhancing fuel efficiency and reducing carbon footprint, Meyer says upgrading a kiln is an expensive process.
Meyer highlights the use of alternative fuels and raw materials by cement manufacturers, including AfriSam, particularly in the use of precombustion chambers for kilns, which allows for further carbon reduction.
AfriSam is using alternative fuels, such as sludges and alternative coal sources, in its kilns, he adds.
Moreover, the company is also focused on the use of ground granulated blast furnace slag (GGBFS) to reduce energy use in cement production.
“The carbon footprint of composite cement using GGBFS is significantly lower – it can be less than half of the ordinary portland cement – and we are driving that,” states Meyer.
Carbon Tax Issues
Meyer states that the implementation of the South African Carbon Tax Bill this month will have a significant impact on the cement industry as an energy user, and that its implementation and the collection of carbon taxes can only be successful, if the gains are used correctly.
Meyer highlights a correlation between the successful collection of carbon taxes and the successful use of such revenue, which results in trust between the tax payers concerned and those in charge of collecting and dispensing it.
“If the money is spent for the purpose that it had been collected, which is to reduce carbon emissions, people will be willing to pay the tax because they know it will be used for the right purpose. If there is a perception of high corruption and/or misappropriation, obviously trust will be low.”
The issue of legislation around the use of alternative fuels and waste materials for energy is another significant challenge to reducing carbon emissions, states Meyer.
“For instance, processing waste materials in our processes is governed by stringent legislation, which adds to the cost of production. Any benefit you might get from your waste materials that you process from an energy process will go towards being legally compliant.
“Output on equipment will decrease and you will lose production rates on your units – all this is costly in the long run,” he elaborates.
Meyer states that, owing to this, many companies would rather use “traditional fuels”– such as coal – that makes no contribution to the overall reduction of carbon emissions, and then pay the carbon tax.
Further, the cement and concrete industry is traditionally a significant contributor to carbon emissions, contributing about 5% to 6% of carbon emissions internationally.
Meyer states that, based on current estimated cement sales in South Africa, between R600-million and R900-million per year could contribute to carbon taxes.
“If you take into account that cement producers are running at significantly reduced margins, the impact is significant.
“However, for the first five years, there will be some tax allowances for cement producers, based on current mitigating factors, to reduce carbon tax.”
The challenge, however, is in dealing with the uncertainty of the Carbon Tax Bill after this five-year period, as there is a lack of information and legislation published about how the tax will be handled after this initial period.