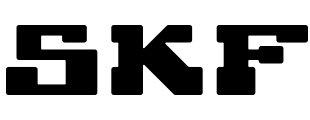
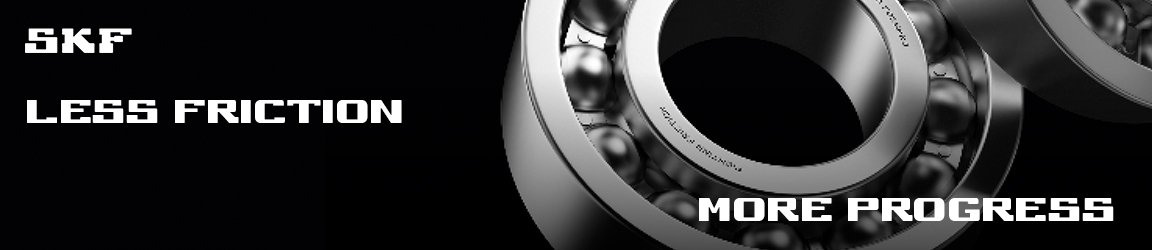
Collaboration between SKF South Africa’s business units leads to customer plant optimisation
Smart collaboration between four of SKF South Africa’s business units has resulted in plant optimisation as well as the delivery of several sustainability benefits for key customer, Wilmar SA (Pty) Ltd, part of Wilmar International Limited.
Founded in 1991 and headquartered in Singapore, Wilmar International Limited is Asia’s leading agribusiness group, ranking amongst the largest listed companies by market capitalisation on the Singapore stock Exchange. Wilmar International’s business activities include oil palm cultivation, oilseed crushing, edible oils refining, sugar milling and refining, manufacturing of consumer products, specialty fats, oleochemicals, biodiesel and fertilisers as well as flour and rice milling. The local company’s consumer products include edible oils, rice, margarine, shortening and mayonnaise.
A Global Service Agreement for SKF Services was signed through the SKF Indonesia office. When this information was shared with SKF Global, SKF South Africa identified an opportunity for providing value added solutions and services for Wilmar SA’s Randfontein plant located on Johannesburg’s West Rand, in Gauteng.
Collaboration between the customer and SKF resulted in SKF offering the management of their rotating assets within the plant,” explains SKF Territory Sales Manager, Simphiwe Siwela. “They have always relied on reactive maintenance and in line with this form of maintenance practice, bearings and other related components would subsequently only be replaced once they have failed. As a result, the customer experienced frequent and unexpected machine breakdowns necessitating unplanned shutdowns which resulted in costly losses in production time and subsequent lost company capital.”
With the customer keen to introduce RCM in partnership with SKF. SKF conducted a site inspection, meeting with Wilmar SA’s technical team Led by Mduduzi Dube (Plant Engineering Manager) and Nhlanhla Maswanganye (Maintenance Planner) to gain a full understanding of the customer’s needs.
Following the site-walk, the SKF business units - CoMo (Condition Monitoring), MaPro (Maintenance Tools), MFS (Mechanical Field Services) and Lincoln (Lube Systems) - combined their collective experience, knowledge, and competencies to develop a best product and service solutions package for Wilmar SA.
“Our recommendations included on-site monthly vibration condition monitoring for critical plant equipment, proposing both on- and offline systems,” notes Siwela. “In addition to monthly lubrication inspections on existing Lincoln systems, SKF and Wilmar decided on the installation of new lube systems for additional critical assets.”
The SKF team further proposed that Wilmar’s technical personnel be equipped with SKF maintenance tools including quick data collection (QuickCollect sensors) and laser alignment tools (MaPro) to facilitate random equipment spot checks. Siwela adds that SKF’s proposal also included training to ensure the skilful, accurate and efficient use of the SKF maintenance products by Wilmar personnel to optimise tool performance.
Wilmar SA accepted SKF’s complete solutions proposal, signing a Service Level Agreement for monthly vibration condition monitoring and inspections of Lincoln lubrication systems over a twelve-month period as well as Mechanical Field Services on an ad hoc basis. A new lubrication system for the extractor machine at the Randfontein plant was successfully installed and commissioned by the Lincoln team. The customer also placed an order for an SKF TKSA71 Laser alignment tool and a CMDT 391-PRO-KS-SL QuickCollect sensor. Siwela affirms that Basic Condition Monitoring and Laser Alignment training has already been conducted with Wilmar SA technicians.
Siwela notes that as a direct result of this on-going project, plant operation has been optimised through significantly reduced unplanned shutdowns owing to increased equipment reliability and service life. He also points out that, most importantly, machine and operator safety has been enhanced.
SKF delivered several sustainability benefits that curtail costs and contribute to the customer’s green environmental goals. In addition to a reduction in the consumption of material, direct energy and emissions during use, indirect energy consumption from supporting systems has also decreased. This aligns with Wilmar International Limited’s strategy of embracing sustainability in its global operations, supply chain and communities.
To add further value, SKF approached the OEM who supplies most of Wilmar SA’s preparation plant’s equipment/machines, proposing collaboration in terms of the bearings supply for their machines. “Our proposal was successful and the company has become one of our OE customers who now purchases directly from SKF,” confirms Siwela.
“We consider this an extremely successful project, adding value for our customer through overall plant optimisation and subsequent increased production while increasing and fortifying collaboration across SKF’s business units,” concludes Siwela.