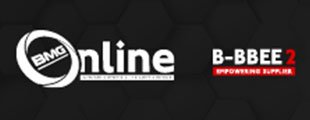
+27 (0)11 620 1500
Droste Crescent, Jeppestown, Johannesburg 2043, South Africa
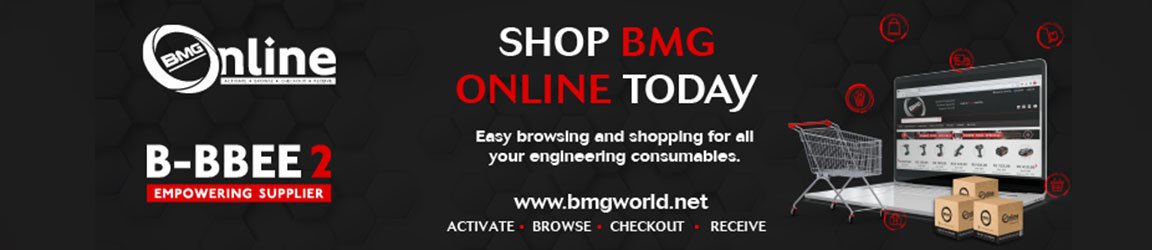
Firm’s products mitigate challenges
In the competitive fastener industry, substandard products often present a significant challenge, one that industrial machinery manufacturer Bearing Man Group (BMG) aims to mitigate through providing solutions that conform to the highest standards and which are manufactured to precise specifications, says BMG fastener division sales manager Maryna Werner.
When it comes to heavy-duty, high-vibration applications such as sugar processing, secure fastening becomes paramount for ensuring long-term joint reliability, she says, noting that BMG’s range of lock bolt pins and collars ensures increased productivity and reliability in heavy-duty, high-vibration applications – especially where structural integrity is critical and where safety cannot be compromised.
“BMG’s Lock Bolt pins and collars – which efficiently replace bolted and welded joints – provide high-strength, vibration-resistant fastening that reduces downtime and improves safety standards, by removing sheet gap and maintaining tension over time,” she further notes.
She explains that this robust two-piece fastening system is vibration-resistant, tamperproof, and fast and easy to install.
“An important advantage for users is that re-torquing is not necessary because of the annular locking groove design. Added to this, the lock bolt fastening system ensures high clamp force, tensile and shear strength and is fully compatible with existing tooling,” Werner says.
Lock bolt technology works on a different principle to regular bolting, she explains to Engineering News, outlining that “instead of a threaded nut, a cylindrical collar with a smooth internal bore is used”.
She adds that the collar is placed over a pin with locking grooves that follows the form of the annular grooves.
During installation, this collar is mechanically “swaged” permanently with an installation tool. The joint is maintenance-free, Werner notes, as once it has been swaged, “it will not loosen under vibration”.
“Not only does this provide major cost savings in labour costs, but the major safety benefit is that the joint maintains the clamp, and it does not become compromised over time.”
An installation tool is used to swage the collar into the lock groove portion of the pin, which creates a permanent fixture of materials that will not loosen under high vibration, thereby ensuring structural integrity, Werner adds.
Lock Bolt pins and collars are suitable for applications where structural integrity is critical, where welding is not an option and where safety cannot be compromised.
“Reliable structural joints ensure improved performance, greater productivity and profitability, as well as greater safety,” Werner says, noting that unlike standard bolts and nuts, which lose preload under service load, “pins and collars never need to be tightened, owing to the annular locking design”.
Lock Bolts are available from BMG in diameters ranging from 10 mm to 30 mm in round and countersunk heads. High vibration stress tests prove that these fasteners consistently maintain 98% of their preload and that the uniform clamp force is consistent for long-term joint reliability.
According to BMG specialists, vibration and shock can quickly impair joint integrity and negatively affect overall product performance, especially in demanding applications in sugar mills, like vibrating screens.
“Our Lock Bolt fasteners have been extensively tested and conform to the very same specifications as the industry standards, making it compatible and interchangeable with existing tooling,” Werner comments.
Apart from sugar mills, applications for Lock Bolt pins and collars include railway coach and truck body manufacturers and for petrochemicals, mining, agricultural and construction operations. These fastening components are also suitable for solar panel frames and for lattice towers in electrical power generation.
BMG specialists work closely with customers in all sectors, to offer a complete service solution, where the team’s technical expertise supports quality structural fasteners and fastening components.
“Training is done on an ongoing basis to ensure our salespeople are up to date with technical objectives to enable us to provide our customers with the best possible solutions,” Werner concludes.