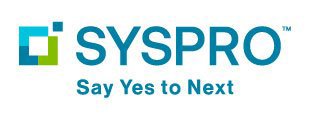
+27 11 461 1000
Block A, Sunninghill Place, 9 Simba Road, Sunninghill, 2191
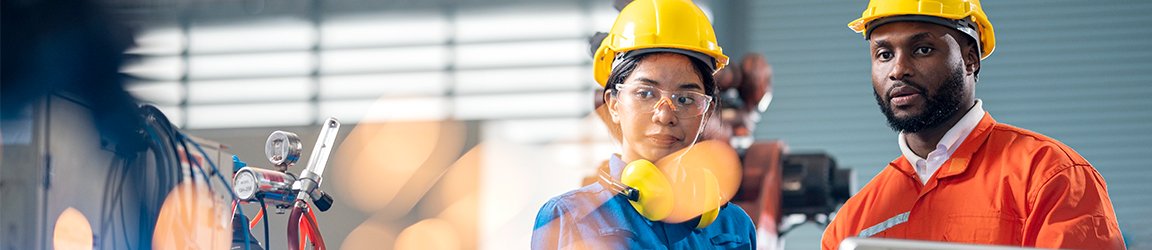
Company upgrades its ERP for companies in food and bev industry
Software company SYSPRO is working on upgrades to its SYSPRO Enterprise Resource Planning (ERP) Version 8, including additional functionalities suitable for two large consumer products companies in South Africa as well as implementing the solution at two other food companies.
“The SYSPRO ERP solution includes a specific functionality that food and beverage companies require, such as batch management, to ensure that material sourcing is known. Recipe management and formulations significantly enhance the normal bill-of-materials functions for this industry,” says SYSPRO Africa professional services manager Doug Hunter.
A bill of materials is a structured list of all the items required for a job, process or production. Such a list provides the input for all the orders to be executed for all the relevant persons such as the purchase department.
The creation of the bill of materials in advance serves as a base for the computation of the timed material requirements and cost in respect of a job or production order, and for quoting the price of the production order.
He mentions that batch traceability is another key requirement for the food and beverage sector, where the SYSPRO ERP allows for the complete tracking of ingredients in a particular batch, which were included in the finished goods, and which sales orders contained these finished goods.
“This allows for the effective and rapid management of any recalls. As a safety precaution, SYSPRO has a trial recall function, which identifies in advance what effect may occur if there is a problem with the ingredients in the batch.”
Further, Hunter tells Engineering News that the company has implemented the SYSPRO ERP at a wine farm and a large brewery, both in Ethiopia; a beverage bottler in Nigeria; and a beverage bottler and distributor in Kenya. The software has been live at the facility in Kenya for the last three months.
“We have also upgraded an existing large beer producer and distributor in India to the latest version of the SYSPRO 8.”
Hunter explains that the SYSPRO ERP empowers a team to efficiently manage all aspects, from recipe quality control and compliance to traceability, purchasing, inventory management, shop floor operations, sales and financials.
SYSPRO provides business owners with instant insight into the status, condition or health of key performance indicators aimed at promoting proactive action while driving improved business behaviour.
He mentions that the latest version of the software includes Avanti – a hypertext markup language-based front-end system – which has an impact on the networking requirements of a company while increasing user experience. Avanti enables customers to link branches through an Internet connection rather than using older and more expensive Terminal Server technology.
The software includes aspects such as social ERP, through SYSPRO Harmony, which allows managers and key users to ‘follow’ and ‘like’ products or ingredients, customers or suppliers, orders and activities as well as note quality assurance failure.
As a result, this will fuel feedback about when specific companies’ products or orders are active and when issues arise that need to be addressed.
“We have included artificial intelligence with machine learning to ensure that predictive analytics learns from the ERP data and transactions to constantly improve accuracy of analytics such as forecasting or predicting supplier performance or potential lateness for attention.
“We have recently introduced SYSPRO Manufacturing Operations Management for advanced scheduling and work-in-progress tracking,” says Hunter.
He adds that, if required, direct factory data integration, such as completions or delays to ERP, will help optimise overall equipment and labour efficiencies in line with Industry 4.0 expectations.
Moreover, with the food and beverage sector, one of the leading markets in terms of business information technology currently, services by SYSPRO throughout Africa and globally are a key focus of current and future development in the sector, notes Hunter.
A key differentiator between SYSPRO and other software vendors is that its focus is on passionately serving clients with manufacturing and distribution processes suited to the food and beverage sector.
To fuel this, the company trains all its developers, sales and service staff in the manufacturing and distribution business processes used by the key customer groups it deals with.
“Typically, SYSPRO ERP enables the entire supply chain, from the importing and costing of raw materials or ingredients, and preparing and sorting these materials for production – and then for batch or process production – to sales order processing, shipment and distribution to customers.”
“It also allows for inventory management and production planning . . . [making] it the main transaction-based business system,” he says.
Hunter adds that this is achieved as one integrated system; however, SYSPRO also allows for external or third-party specialist systems to integrate through e.Net Business Objects, which ensures properly governed database integrity in and out of SYSPRO.
Such integrated systems include detailed warehouse management and on-line Web portals for e-commerce orders, as well as laboratory systems to enhance food security and link laboratory results to SYSPRO’s quality management.
Further, SYSPRO ERP enables companies to manage their supply chain transaction effectively through role-based security, ensuring that user access enables sales departments to take orders, but not overcommit on excessive or unauthorised discounts.
It also ensures that procurement buyers buy only from approved suppliers at the right price, making the products more cost effective.
“SYSPRO ERP also manages product shelf-life, ensuring that stock is allocated to clients, preserving the longest shelf-life of the products for clients to use or sell. These functions are essential to food and beverage companies,” he states.
Through demand forecasting, material requirements planning, production and work-in-progress management, production from the same assets or machines is increased, leading to lower manufacturing costs and labour working on the right orders, he concludes.