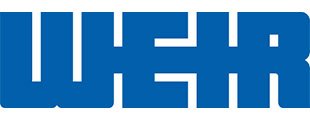
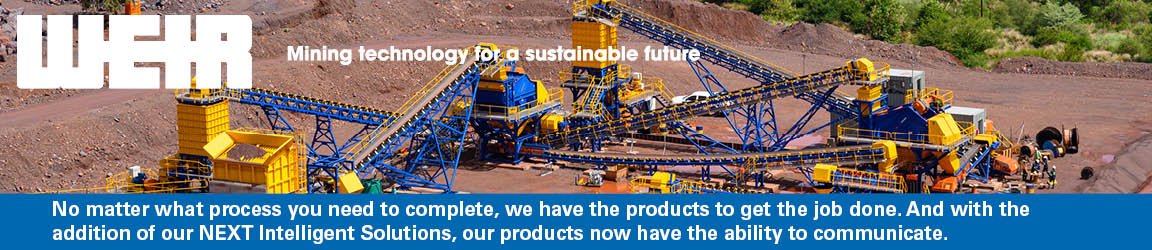
Custom-made rubber hoses produced locally
South African rubber hose manufacturer Weir Minerals Africa designs and builds mining hoses from 50 mm to 1 000 mm nominal bore up to 10 m in length and up to 1 100 mm bends.
The hoses are designed to the specifications of customers around the world, using an option of Linatex, Linard, Linagard and Linacure abrasion-resistant internal wear liners. The hard wall mining hose is built for suction and discharge applications, with a heavy spring steel wire helix to cater for high dynamic loads. For discharge applications with no vacuum or suction that could collapse the hose, the soft wall mining hose is usually used as it allows for ease of movement and flexibility.
“Our state-of-the-art manufacturing facility in Alrode, Gauteng, comprises advanced semi-automated processes to produce both hard wall hoses, soft wall hoses and bends,” says Weir Minerals Africa product manager rubber products, hoses and spools Yatheen Budhu.
“The safety of our people is our number one priority, and the investment included system improvements in the hose building process protecting our employees from harm at all times,” he says.
“Among the innovations we have introduced is a wear-indicator system, for critical applications where unexpected hose failure carries an unacceptable level of risk,” says Budhu. “The wear-indicator system gives operators early warning of wear on the liner, and allows proactive replacement to be planned and conducted.”
The company’s local manufacturing capability gives a number of benefits to mining companies, including a quicker lead time, he says.
For mines across the commodity spectrum, Weir Minerals asserts that its rubber hoses deliver long wear life – from demanding conditions in mineral sands dredging operations to tailings, cyclone feed or thickener underflow.
“Our hoses must deal not only with abrasive materials, but also unexpected foreign objects in slurry, some of which may be sharp,” says Budhu. “Nonetheless, as an example, we have seen our hoses in mineral sands applications last up to seven years – considerably longer than the customer is used to.”
The company also manufactures related equipment such as flexible distance pieces (instead of normal bellows) to customer specifications. With its Linatex wear liner, these items last considerably longer and can be used to connect pipework that is not well aligned, he adds.