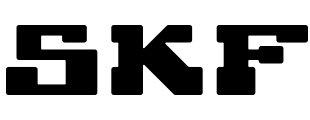
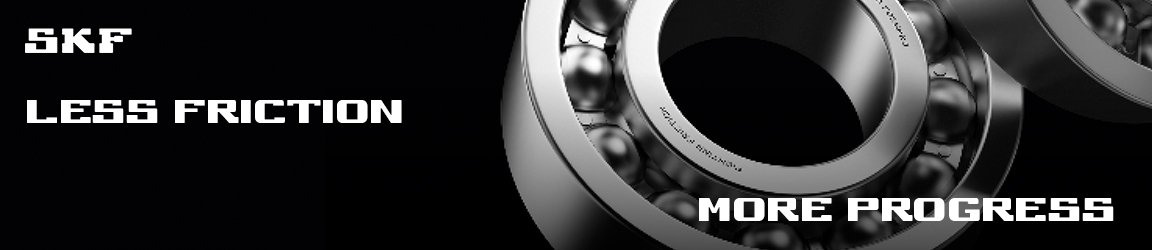
Diagnostic services optimise operations and protect critical plant assets
Early diagnosis of potential problems before they escalate is key to the protection of critical plant assets and the optimisation of operations, says bearing and seal manufacturing specialist SKF.
The company’s Rotating Equipment Performance (REP) Centre, previously known as the SKF remote diagnostic centre, based at its Jet Park head office in Johannesburg, offers a comprehensive suite of condition monitoring, analytical, and diagnostic solutions.
“Customers simply need to collect necessary data from their plant equipment and upload it to the Cloud. Applying our integrated engineering expertise, software, and analytical tools, we convert this critical data into actionable engineering insights on how to better protect and optimise plant assets for enhanced operational performance,” explains SKF connected technologies manager John Storm.
Capabilities include the remanufacture of critical components, such as large sized bearings, offering cost-savings and environmental benefits through the reduced use of raw material and lower CO2 emissions compared to manufacturing new bearings.
The company says it has scaled up its diagnostic and reporting services and capabilities and it can use the Cloud to deliver analysed diagnostics and machine health insights to SKF engineering specialists who develop quick-response solutions for potential issues in the field.
The company has also integrated its authorised distributor partners into its digital ecosystem by creating a platform for sharing insights from the REP Centre.
“By providing our authorised distributors with access to information, dashboards, and reports, we empower them to enhance their machinery health-related services for customers,” asserts Storm.
Rather than developing stand-alone black box systems, SKF explains that it uses flexible architecture specially designed to offer a range of integration levels and possibilities, spanning from local SKF hardware solutions to fully connected Cloud-based systems.
"We never impose a single connectivity architecture on plant operators, offering instead, versatile solutions that can be seamlessly integrated into any environment with straightforward, flexible onsite implementation,” stresses Storm.
“Moreover, our solutions also support long term evolution and global positioning system wireless networks when ethernet connectivity is unavailable. And if there is zero connectivity, we have the capability of manually downloading data from SKF devices to a cellular device, which can then be taken to a location with data access for uploading to the Cloud."
Handheld devices include the SKF Quick Collect sensor, the next-generation Microlog analyser DBx, Axios, and the wireless IMx-1 condition monitoring systems. SKF recommends the Quick Collect, Axios, and IMx-1 systems for high-speed applications, above 600 rpm, and lower criticality assets that require less data uploading.
More sophisticated solutions are needed for low-speed vibration monitoring, typically associated with critical, large, and heavy equipment such as conveyor drives, crushers, and grinding mills. These complex machines are often found in challenging environments such as mining sites or fixed processing plants. For such advanced applications, SKF recommends fully wired online sensor systems connected to the SKF IMx-8 or IMx-16 data logging systems specifically designed for low-speed rotating equipment analytics that require high-resolution data in the lower frequency ranges to get the spectral quality required for detailed analysis.
The company also offers a semi-online solution that features the installation of wireless sensors on plant equipment, connected to SKF Enlight Collect IMx-1 gateway devices. The IMx-1 mesh-able device has a range of 20 m to 30 m from the sensors, depending on plant density. It can support up to 100 sensors connected using a 2.4 GHz wireless mesh network to a single gateway. Typically set to collect data daily, the IP69-rated, battery-powered wireless sensors are designed with an expected nominal battery life of five years.
SKF notes that it has extended its REP services into the rest of Africa, prioritising mining as a key growth sector.