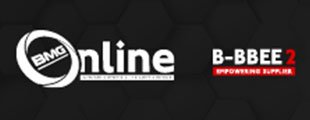
+27 (0)11 620 1500
Droste Crescent, Jeppestown, Johannesburg 2043, South Africa
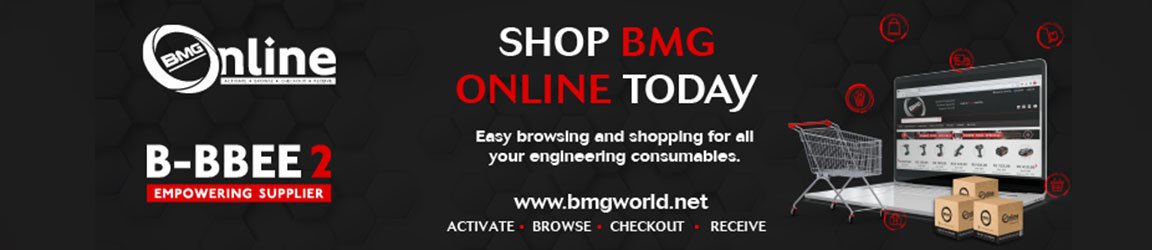
Hydraulic systems need filtration
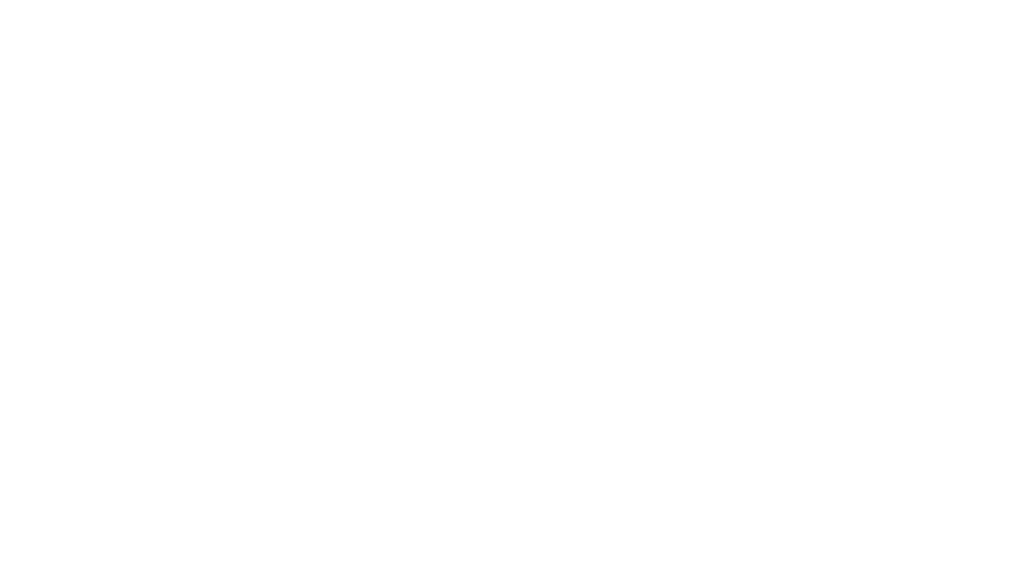
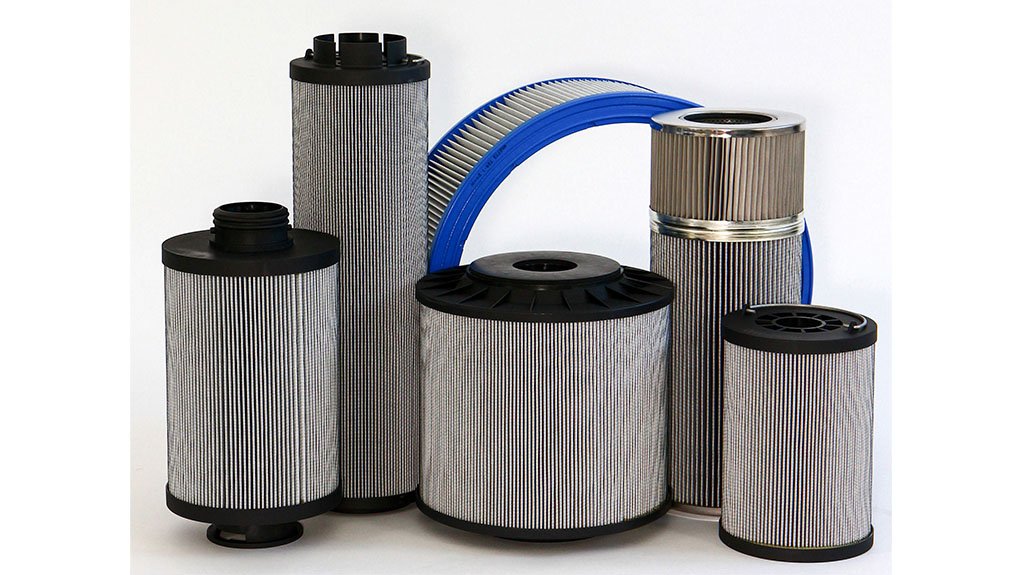
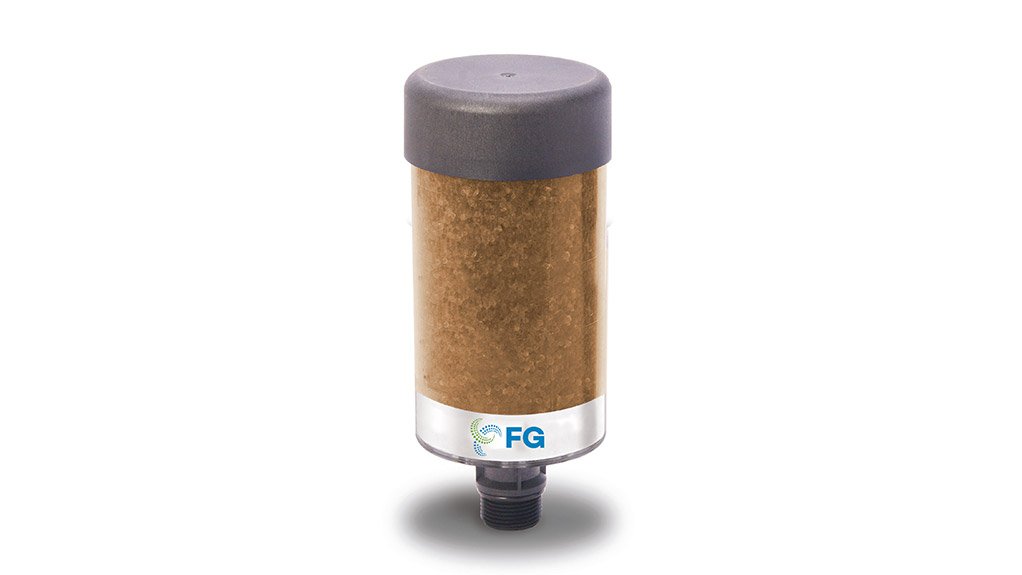
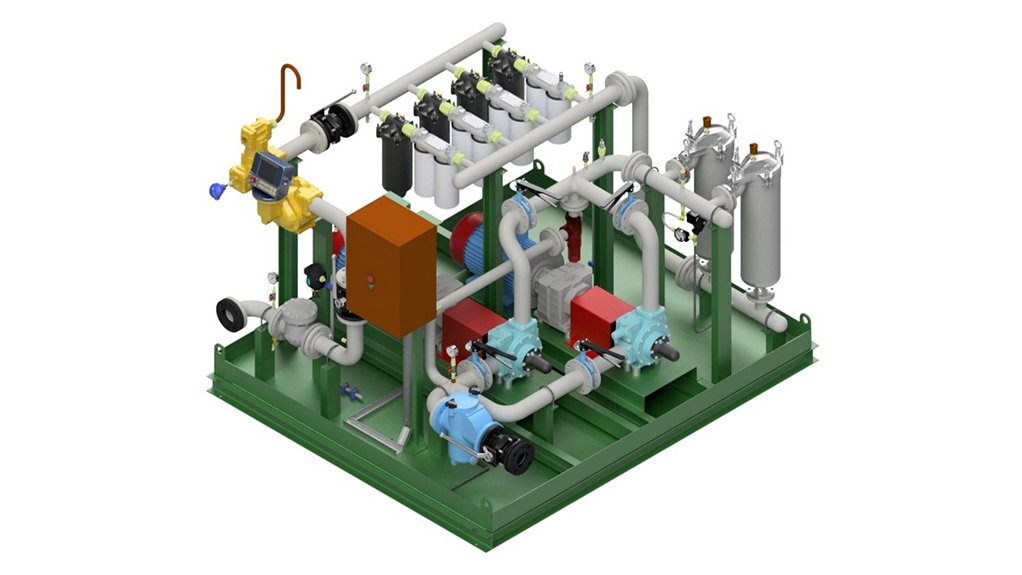
FILTERS Filtration Group manufactures advanced filters that ensure that the fluid in the circuit of the process meets the required cleanliness class
Photo by BMG
TAKE A BREATHER BMG's design of and materials used for the construction of filter housings and elements exceed industry standards
FILTRATION SYSTEM As filtration is the only effective defense against wear and tear, it is critical that effective filter components are used to ensure dependable performance
Hydraulic systems are susceptible to wear from abrasive particles and therefore require efficient filtration to offer adequate protection of equipment, explains industrial equipment supplier BMG product specialist industrial filtration Hanli Schutte.
Contaminants can enter the hydraulic system from several sources – the manufacturing process of system components or exposure to environmental dirt, dust and moisture during production. Problems also result from low quality or unclean hydraulic fluids used during the filling process, or from wear over time, says Schutte.
As filtration is the only effective defense against wear and tear when contaminants are present, it is critical that effective filter components are used to ensure dependable performance, high efficiency and extended service life of machinery and vehicles.
“Without a structured control and contamination prevention programme, premature equipment failure is likely to occur, resulting in unnecessary downtime and costly replacement of parts”.
BMG Fluid Technology’s filtration solutions comprise of a wide range of fluid power components and systems, supported by the team’s broad technical capabilities to ensure fluids – including oil, fuel and lubricant oil – which operate within the required cleanliness standards.
BMG’s premium filtration partner – Filtration Group – manufactures advanced filters that ensure the fluid in the circuit of the process meets the required cleanliness class.
Further, Schutte says design of and materials used for the construction of filter housings and elements exceed industry standards and through the latest technologies, like PulseShield and e-protect, the dirt holding capacity of filter systems is increased to ensure full functionality, even in the most challenging environments and applications.
Filtration Group’s product portfolio comprises desiccant breathers that are designed to replace conventional dust caps or breathers of equipment, such as hydraulic units, where there are high humidity and temperature fluctuations.
With this highly efficient filtration system, contaminated air passes through layered filter media, which blocks particles from entering the breather. A bed of silica gel absorbs any moisture in the air to keep equipment dry. This technology prevents problems associated with condensation, ageing of hydraulic oils, degradation of additives and corrosion.
Schutte notes that within a hydraulic system there are typically four locations where filters are required - suction line, return line, pressure line and reservoir breathers.
Suction filters are designed to remove large particles that accumulate within the hydraulic fluid reservoir, while safety filters can be positioned inside the reservoir or outside the reservoir on the suction side of the pump. The objective of return line filters is to remove contaminants from the hydraulic fluid before it is returned to the reservoir. Pressure line filters – also known as point of use filters – remove fine particles before application and can withstand high operating pressures and temperatures.
Breathers on reservoirs protect the hydraulic system from environmental contaminants such as dust and moisture.
An important feature of Filtration Group filter elements is they are fully compatible with housings of other filter manufacturers and increase the efficiency of the installed filtration system.
Through the acquisition of OMSA in 2013, BMG extended its services into the filtration sector. BMG’s OMSA ECO spin-on elements enable fast and convenient protection for the offloading and dispensing of bulk fuel. This range includes fuel and water separating filter elements for particle removal of 6 µm and 3 µm.
“These filters are used extensively in BMG’s custom-designed offloading and dispensing filtration systems.”
In addition to the design and manufacture of new bulk fuel systems for oil and lubrication purification, BMG’s “technically skilled” team also offers a refurbishment service for existing systems. Typical applications are in machine tools, mining, power generation, sugar, pulp and paper, cement, marine and hydraulic industrial equipment, notes Schutte.
These systems are designed and manufactured to exact customer specifications and generally include all mechanical, electrical and pneumatics as required. Bulk fuel systems can be designed as permanent in-line or off-line systems, as well as portable systems that can be used in multiple applications.
To provide customers with continuous contaminate-free fuels and lubrication solutions, BMG’s Field Services department offers services that include the inspection, service and maintenance of bulk fuel and hydraulic systems. Oil analysis is conducted by BMG’s qualified tribologist, to ensure the required cleanliness of oils and fuel.
BMG’s fluid technology services include solutions for fuel and industrial filtration systems, hydraulics and pneumatics, lubrication, hydraulic hose and fittings, as well as instrumentation, pumps and industrial valves.
Through the company’s specialist skills BMG can meet high demand from customers for dependable filtrations services, throughout the African continent, Schutte concludes.