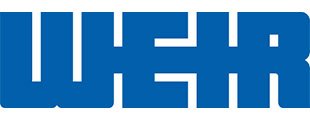
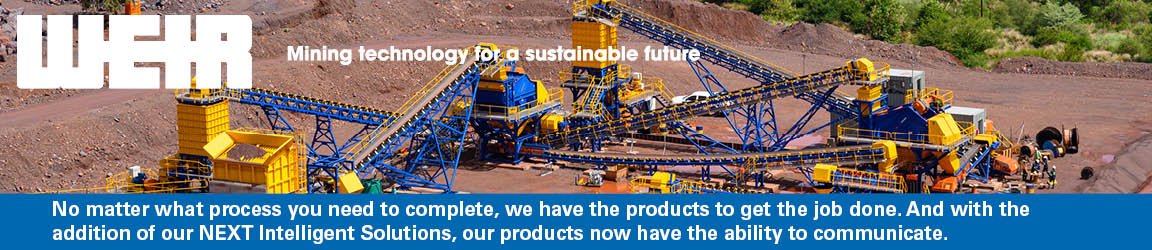
GEHO® pumps are the lifeblood of SIMEC mining’s operation in Whyalla, Australia
SIMEC mining produces iron ore concentrate for the Whyalla steelworks. It’s the GEHO® positive displacement pump’s responsibility to pump the slurry 67km from the plant to Whyalla, where it is then dewatered and converted to pellets for the steel making process. SIMEC mining has two GEHO® PD pumps, which are the most critical pieces of equipment on site. The main purpose of the high pressure GEHO® PD pumps is to ensure the material stays suspended in the pipeline throughout the 67km journey to Whyalla. “The GEHO pumps transport the slurry about 250 cubes an hour, 300 tons an hour into town. They run every day, all day and are very powerful pumps. They have defined maintenance intervals that allow us to run each pump for the nominal amount of time without any risk of breakdown,” states Chris Stanton, Senior Process Engineer, SIMEC Mining. As the GEHO® pumps are critical for both the plant and the steelworks industry, it’s crucial that both pumps are well maintained so they continue to perform year after year, and this is made possible through the close partnership between Weir Minerals and SIMEC Mining.“If the GEHO pumps didn’t operate properly then the pipeline would be at risk, and that would be a major issue as the pipeline is the lifeblood for both our operation and the entire township of Whyalla,” states Anthony Sheely, Concentrator Operations Coordinator, SIMEC Mining.
Going the distance
Pumping long distance is a critical requirement for many mines around the world, but often comes with challenges and key design considerations that operators must be mindful of.
“The biggest challenge of long distance pumping is generating slurry with a suitable particle size distribution for the application. Operators must concentrate the particle size distribution to make it a pumpable slurry whilst trying to minimise the amount of water used in the process,” states Peter Thissen, Global Product Manager for GEHO® pumps at Weir Minerals.
“We deal predominantly with high solids concentrations, which is becoming more important in both a water constrained and environmentally sensitive industry. Our depth of experience and knowledge together with the delivery of innovative designs has provided effective solutions to meet our customers’ needs around the world.”
Designing a long distance pipeline is a complex balancing act between the rate of flow, the concentration of slurry and the size of particles. For solids in slurry to remain in suspension, they need to be moved by the liquid at a particular minimum velocity.
Another challenge operators are faced with is the pipeline route, it has to be the most economic means of transportation and suitable for the flow behaviour of the material.
“It’s much easier to build a pipeline on flat land as it stays horizontal and the operational condition for the materials is constant, as long as we can keep the particles in suspension. However, if we have to cross rivers, mountains or valleys then the pipeline will be built on an angle and great consideration must be given to the design of the pipeline, transport velocities and starting and stopping the pipeline,” states Peter Thissen.
Why GEHO® PD pumps are ideal for long distance slurry transportation
Weir Minerals’ GEHO® crankshaft driven pumps are among the world's most advanced positive displacement pumps, expertly designed to transport slurry over long distances, reaching up to 550km and more than 2,000 metres uphill.
“Our GEHO pumps are designed to handle high-density slurry with solids up to 85%. With extremely high availability, low energy consumption and operating costs they ensure uninterrupted, trouble-free operation,” says Thissen.
The diaphragm in the pump separates the abrasive slurry from the operating components, with the exception of the valves, protecting them from wear and ultimately prolonging the life of the pump. What this means for the operator is significant savings for wear parts, resulting in a very economic and extremely reliable product for pipeline transportation. If maintained properly the GEHO® pumps continue to run year after year, 24 hours a day; with references of GEHO® pumps in operation for 30+ years.
“As long as the make-up of the slurry doesn’t change and pumping conditions remain the same, our GEHO pumps will continue to operate indefinitely. Combined with long maintenance intervals and highly dedicated service engineers, they keep processing plants operating at peak performance while delivering a low total cost of ownership,” Thissen concludes.
The innovative pump technology behind GEHO® pumps is backed by continuous advanced research and in-house laboratory test facilities, resulting in superior efficiency, reliability and availability.
Weir Minerals Africa