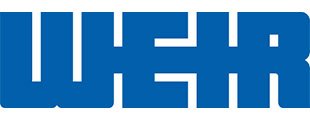
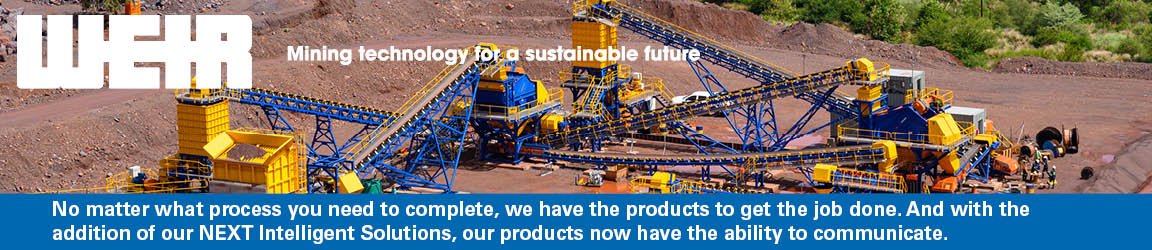
Innovation key as mill circuit pumps perform
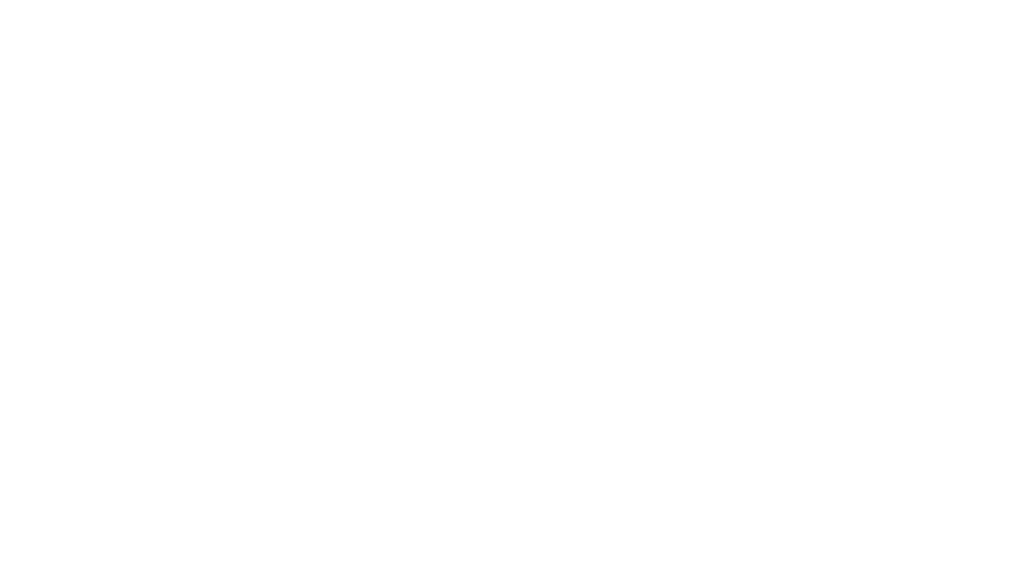
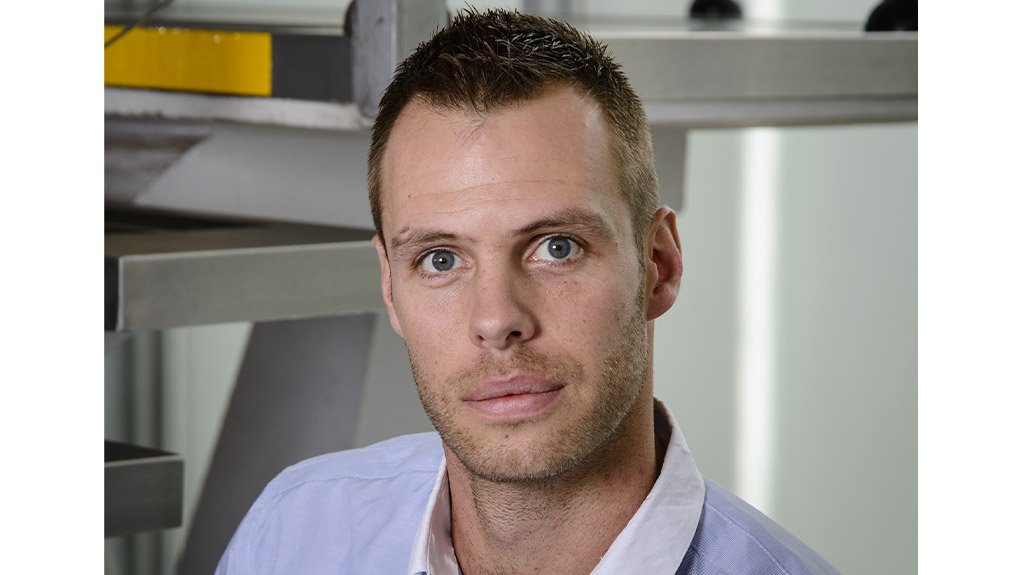
MARNUS KOORTS Innovation, partnership and optimisation have enabled the company to double the wear life of its pumps
Weir Minerals’ focus on development and continuous product improvement has contributed to the success of the company’s Warman mill circuit (MC) pumps.
Mill pumps, the largest pumps in the milling circuit, manage large-size particles in highly abrasive slurries in large volumes, which leads to increased wear and consumes a significant amount of power.
“Mill pumps get a lot of attention because of their scope and size, as well as their impact on the business,” says Weir Minerals Africa pumps product manager Marnus Koorts.
Innovation, partnership and optimisation have enabled the company to double the wear life of its pumps and ensure efficiencies that allow for the same output, but with lower electricity consumption and ease of maintenance.
“We have been developing these for well over eight decades and a strong point for the company is the continual upgrade of existing installations with new technology,” he tells Mining Weekly.
The Warman MC pump is the company’s global flagship, with advanced technology to deal with wear, reduce recirculation, diminish the formation of eddies and obtain better hydraulic efficiency.
“It boils down to the power of continuous optimisation. A plant today should not look the same as one from 1980, as there have been extensive technology advancements since then. Weir Minerals ensures the ease of transition to the newer technologies,” he says, adding that this includes capturing data, computational fluid dynamic analysis on the flow of the material going into the pump and civil work, when required.
Coupled with improved wear life, product upgrades, optimisations and the integration of products and services, this results in significant energy and maintenance cost savings.
As an original-equipment manufacturer, there is a need to ensure the pump is as efficient as possible, as these types of pumps are often operationally more costly than the cost required to install it, Koorts explains, noting that efficiencies are often overlooked during pump selection.
An incorrect pump selection will result in suboptimal pump performance with an associated increase in operating costs and a subsequent decrease in the operation’s bottom line.
While the company’s Warman MC pump is larger than standard, this contributes to its increased wear life, as it turns slower resulting in less wear.
“Efficiency, for Weir Minerals, is a really big deal – that is where we want to make our mark,” he says, adding that reducing the carbon footprint is becoming increasingly key for customers.
By making some internal changes, even a two to three percentage point boost in energy efficiency can save hundreds of thousands of rands in power on some of the motors associated with these larger pumps.
Unique Attributes
Weir Minerals introduced an adjustable throatbush, which maintains an optimal gap between the throatbush and impeller front shroud for the particles to flow through without catching and tearing the rubber.
“As the impeller wears, the gap naturally increases and reduces the efficiency of the pump; so, by pushing it back, the pump will be as efficient on the last day of operation as it was on the first day it started up,” he explains.
The throatbushes feature pre-swirl vanes, allowing for slight changes in direction to produce more of a natural flow, which, in turn, improves wear life, reduces downtime and provides reliability.
Further, the Warman MC pump’s split casing design allows for easy access when replacing the impeller and its quick changeout design allows for the entire bare shaft to be switched out with a refurbished one, allowing easy maintenance, with minimal plant downtime.
“It makes a traditionally very difficult-to-handle product quite convenient in terms of maintenance,” Koorts says, highlighting that maintenance is one of the core selling points.
Another unique attribute is the availability of metal, rubber and metal/rubber composite ranges.
The various Warman pump models feature interchangeable materials from a wide range of high chrome proprietary alloys like Ultrachome and Hyperchrome and compression-moulded elastomers, which allows for changing from one material type to another.
This allows for not only optimum materials selection for every specific application, but also ensures that the wear characteristics for every component are balanced.
The Warman MCR pump features thick elastomer liners inside a ductile iron outer casing, with a metal impeller, a metal or elastomer throatbush and frame plate liner insert, while the Warman MCR-M pump has high chrome iron metal liners inside a ductile iron outer casing with a metal impeller, throatbush and frame plate liner insert, which can also be converted to rubber liners. The Warman MCU pump boasts an all-metal unlined high chrome iron casing with a metal impeller, throatbush and frame plate liner insert.
While technology advancements are being made, the Weir Minerals Research, Innovation and Technology teams are always expanding the boundaries and improving technology, Koorts comments: “We are continuously investing in the product and we see a future where we can further double the wear life”.