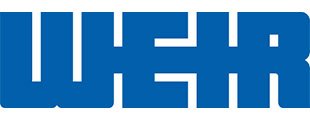
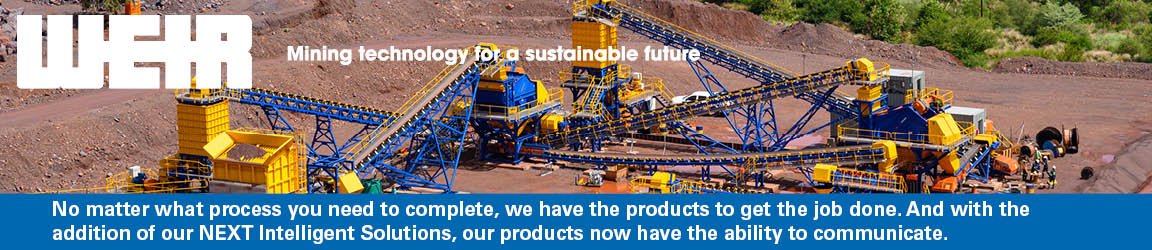
Integrated Solutions delivers plant efficiency
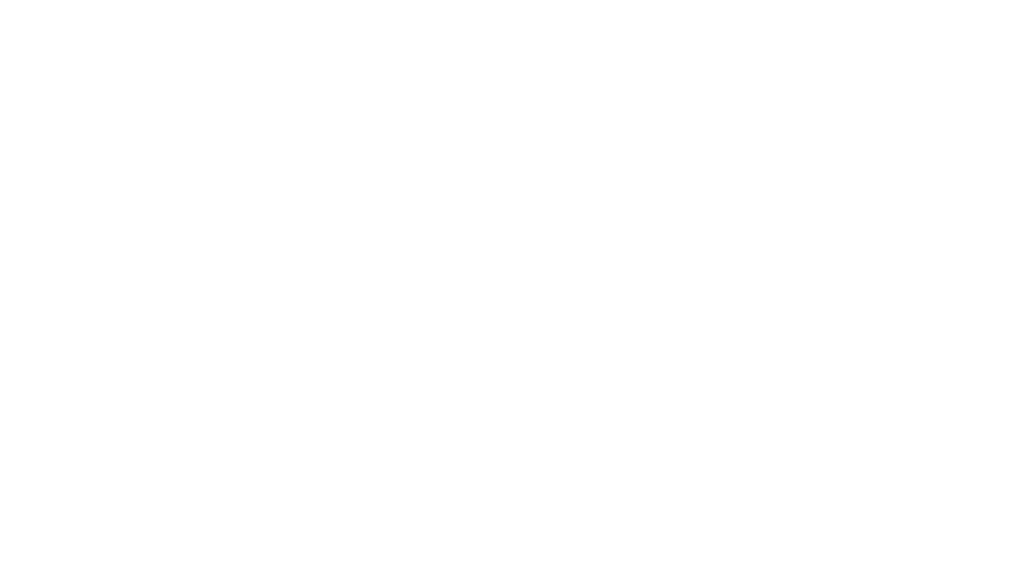
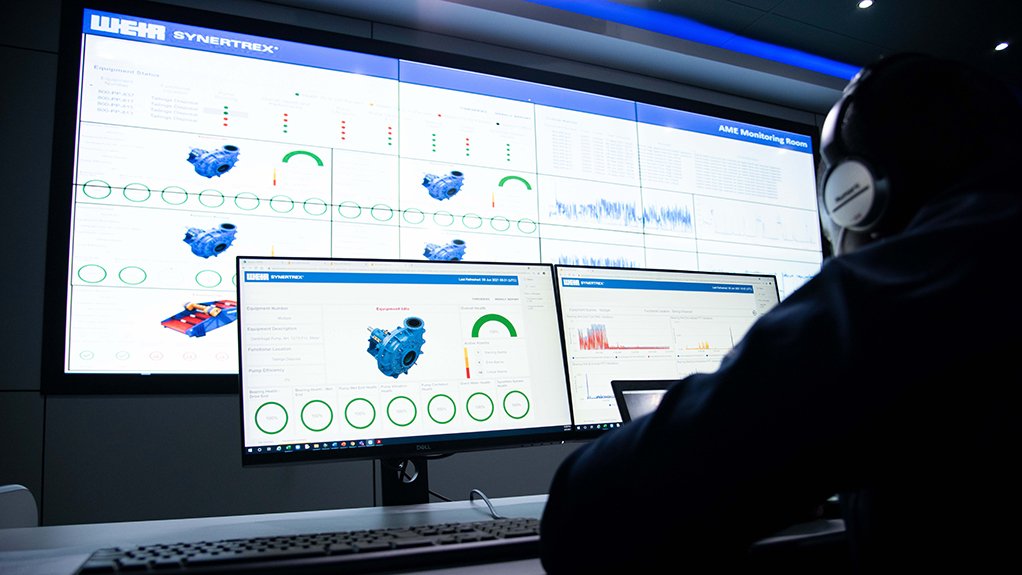
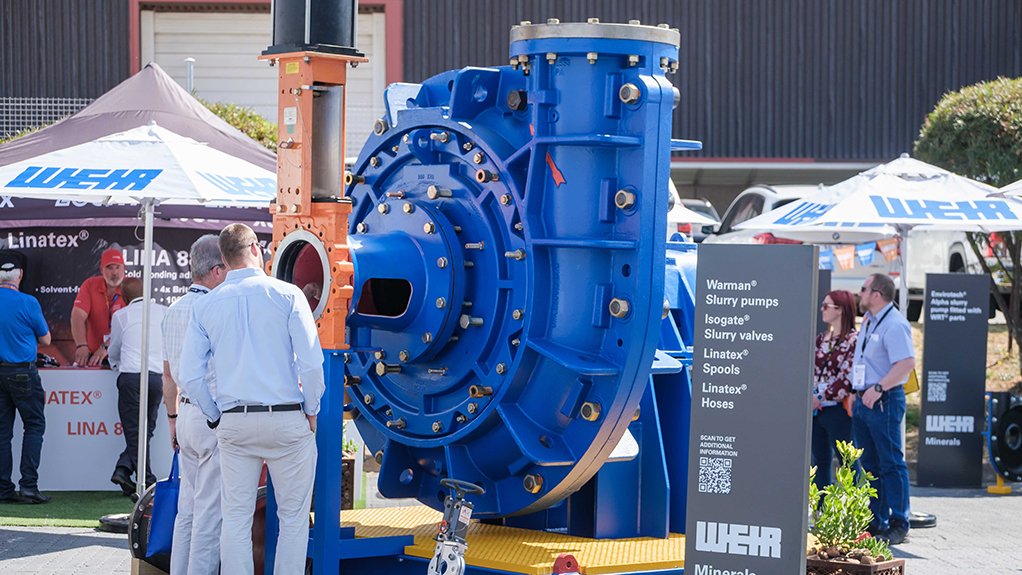
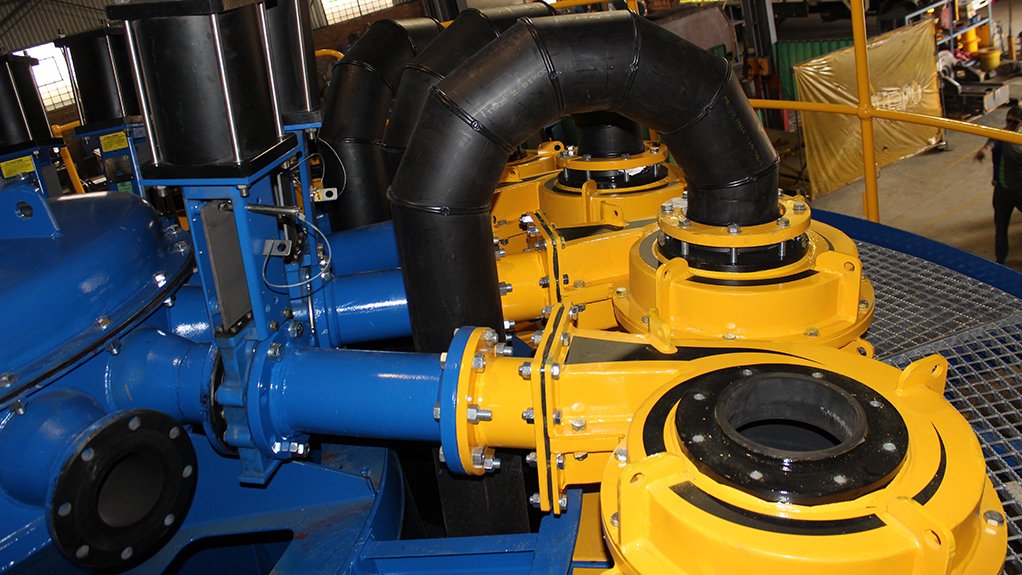
Weir regional MD Rajen Govender speaks to Creamer Media's Simone Liedtke at this year's Investing in African Mining Indaba. Video and editing: Nicholas Boyd.
Synertrex intelligent platform conveys real time data of the customer’s equipment performance and health
Weir Minerals showcased their Integrated Solutions capability at the recent Electra Mining 2022 exhibition
The Integrated Solutions teams work with the customer to understand their operation in order to offer the best solution for their process
Through its Integrated Solutions approach, Weir Minerals Africa can provide fast and effective assistance to customers who are engaged in brownfield optimisation of their operations or looking for solutions to particular problems hindering efficient production.
Weir Minerals’ dedicated Integrated Solutions teams combine diverse experience – ranging from comminution to tailings and from chemistry to hydraulics – and typically include process engineers, design engineers and product experts, as well as local Weir Minerals Africa personnel, who will have a thorough knowledge of customer sites in their areas.
“Our multi-disciplinary teams ensure that a problem is considered from all perspectives, identifying potential issues and opportunities to optimise the circuit with upstream and downstream benefits,” says Weir Minerals Africa Rest of Africa sales director Pieter van den Berg.
He adds that the teams can perform process audits during site visits to identify bottlenecks and then use flowsheets, mass balances, three-dimensional layouts and feasibility studies to advise on the most appropriate solution to a particular problem.
Weir Minerals Africa’s extensive footprint is one of the cornerstones of the company’s Integrated Solutions strategy.
“Our unrivalled manufacturing and service network, featuring service centres within 200 km of most major mining areas, is at the heart of the value we deliver to customers,” states Van den Berg. “We believe it is essential to be close to our customers and to understand their operations in detail. We expect our engineers in any particular area to be completely familiar with the installations and circuits they service.”
He says Weir Minerals Africa’s local service centres, in combination with its Integrated Solutions teams, have delivered some outstanding results to customers, allowing them to reduce maintenance costs, achieve significant water and power savings and increase throughput at their facilities. Among recent successes have been a $8-million integrated solutions order received from a diamond mine in the Southern African Development Community region, as well as a $2-million order from a Central African copper mine.
Digital solutions can often form part of an integrated solution. In the digital field, Weir Minerals continues to strengthen its capabilities with the Synertrex® intelligent platform at the heart of its digital offering. The Synertrex® IntelliWear™ wear monitoring system for spools and hoses in slurry pipelines is the most recent addition to Weir Minerals’ digital range.
“This allows pipeline operators to check their equipment in the critical wear areas and perform predictive maintenance to prevent unplanned disruptions and downtime from occurring,” says Van den Berg. “Most importantly, safety on site is increased, as spools and hoses are replaced prior to failure, thus removing the risk of slurry leakage which can cause injury to workers on site and damage to the environment.”
Summing up, Van den Berg says Weir Minerals Africa takes the time to understand customers’ problems before providing them with solutions. “We go the extra mile in trying to understand their processes to really figure out how we can help. This combined with our products really sets us apart. Our product lines have been proven through the years and our reputation has stood the test of time throughout the world across different environments. Our Integrated Solutions teams have the experience and know-how to tackle any given problem.”