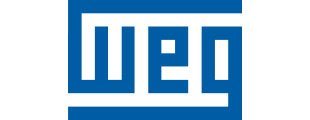
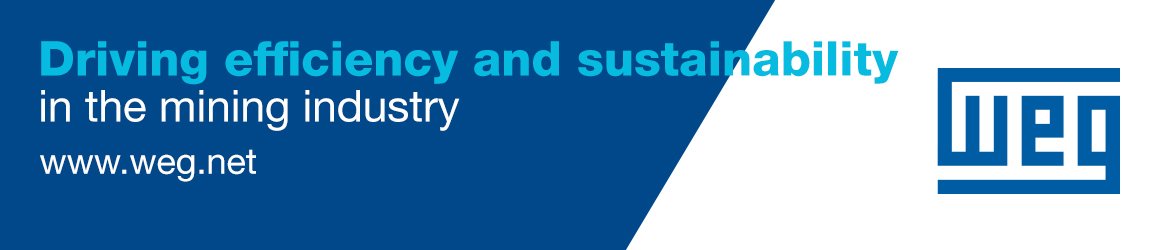
Kusile power plant project, South Africa
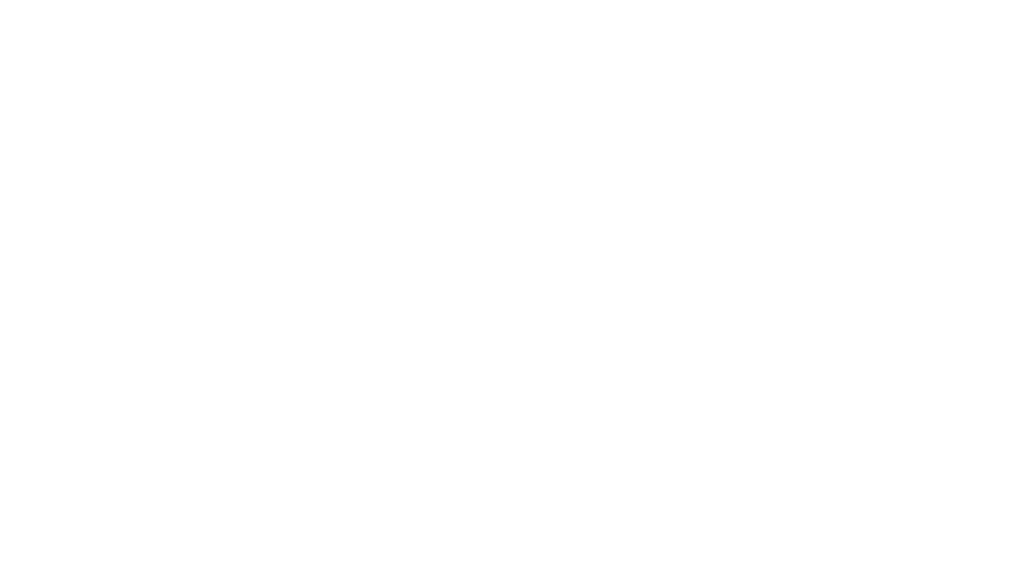
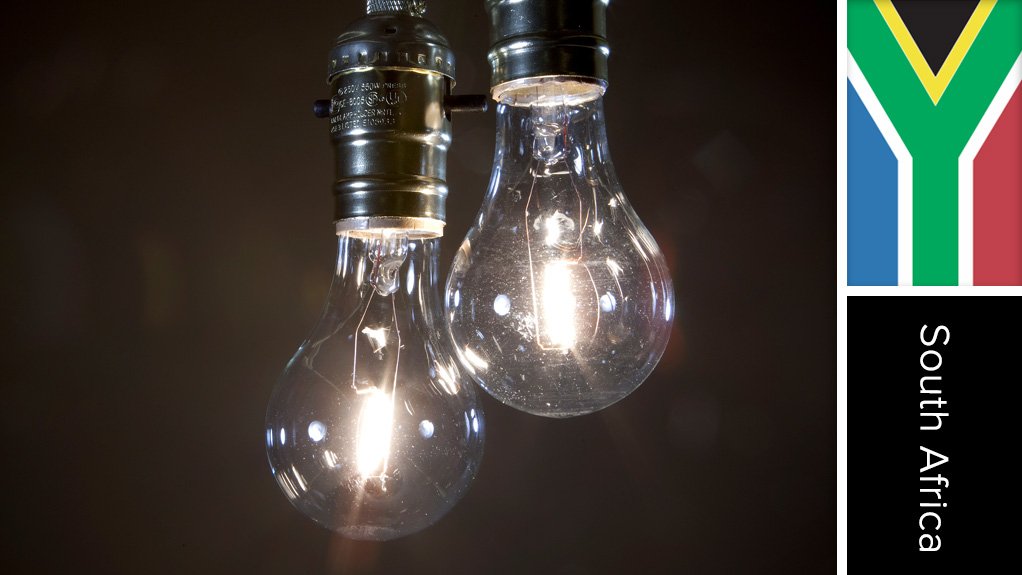
Name and Location
Kusile power plant project, Mpumalanga, South Africa.
Client
State-owned utility Eskom.
Project Description
The Kusile power station project, which is located near the existing Kendal power station, in the Nkangala district of Mpumalanga, will comprise six units, each rated at an 800 MW installed capacity for a total capacity of 4 800 MW. Once completed, Kusile will be the fourth-largest coal-fired power station in the world.
The Kusile project will include a power station precinct, power station buildings, administrative buildings (control buildings and buildings for medical and security purposes), roads and a high-voltage yard.
The associated infrastructure will include a coal stockyard, coal and ash conveyors, temporary and permanent water-supply pipelines, temporary electricity supply during construction, water and wastewater treatment facilities, ash disposal systems, a railway line, limestone offloading facilities, access roads (including haul roads) and dams for water storage, as well as a railway siding and a railway line for the transportation of the limestone supply (sorbent).
The power station will be the first in South Africa to install flue-gas desulphurisation (FGD) – a state-of-the-art technology used to remove oxides of sulphur, such as sulphur dioxide, from exhaust flue gases in power plants that burn coal or oil. This technology is fitted as an atmospheric emission abatement technology, in line with current international practice, to ensure compliance with air-quality standards, especially since the power station is located in a priority air shed area.
The FGD plant is a totally integrated chemical plant using limestone as feedstock and producing gypsum as a by-product. Each supercritical tower boiler (highly efficient) will be about 115 m high. The air-cooled condensers will be constructed on and supported by twenty 60-m-high concrete columns.
The plant will use an air-cooling system to help conserve water. A total of 16 000 t of structural steel was used for the first unit’s boiler construction and it is expected that 115 400 t of structural steel will be used for all six units and the balance of plant.
The operational life of the power station is expected to be 60 years. The total estimated cabling to be installed for each Kusile unit is 5 300 km per unit.
The bulk of the coal will be sourced from mine mouths in the local area, with further exploration continuing.
Value
Costs as at the January 31, 2015, inception date: R82-billion, excluding interest during construction.
Total cost is estimated at R118.5-billion excluding interest during construction, cost of cover and inflation.
Duration
Eskom indicated that the first synchronisation of Kusile Unit 1 is now scheduled for the first half of 2017, with the 800 MW unit expected to enter commercial operations only in the second half of 2017.
Latest Developments
Amid the confusion about whether the technical requirements had been fully met during the recent Medupi Unit 6 blow-through, Eskom and Mitsubishi Hitachi Power Systems Africa (MHPSA) have set up a joint technical task team to review and optimise the blow-through procedure ahead of future blow-through tests on the 11 other Medupi and Kusile units.
MHPSA, previously known as Hitachi Power Africa, is the main boiler contractor at the power projects, which have been plagued by delays, strikes and funding difficulties.
Eskom, which is facing major claims across both sites, is yet to provide a final cost estimate for the projects and, besides promising that Medupi Unit 6 will be synchronised in February, it has also not provided a definitive update regarding the expected interval between units.
However, it recently reported that the first synchronisation of Kusile Unit 1 is scheduled for the first half of 2017. The schedule for Kusile Unit 1, contained in CEO Tshediso Matona’s most recent state of the system presentation, represents a major delay from earlier indications that the milestone could be achieved in the first half of 2016.
Kusile recently achieved a few project milestones as a build-up towards Unit 1 synchronisation.
The 910 MVA generator step-up transformer weighing 300 t was put on its foundation, assembled with all its auxiliary systems and filled with 128 000 ℓ of mineral oil in October 2014. All electrical integrity tests were performed successfully to confirm that the transformer was ready to receive power. Unit 1’s TurboGen set was put on electrical barring in the same month.
A lubricating oil flush was conducted on all the bearings on the turbine train in September 2014 to ensure that sufficient oil would be supplied to the bearings for lubrication and to also confirm that there were no leaks and blockages in the pipework.
The main civils joint venture contractor, comprising Wilson Bayly Holmes-Ovcon (WBHO), Group Five, Steffanuti Stocks and Basil Read, also completed the concrete pour of Unit 6’s TurboGen foundation, comprising 3 600 m3 of concrete. This is a 36-hour continuous concrete pour that proceeded without hindrances. About 300 employees were involved in preparing and placing rebar and concrete shutters. All this took about three months to execute. The same contractor re-accessed the Boiler 1 area to build the foundation of the submersible scrapper conveyor of the boiler. This is where the hot ash from the combustion chamber falls into a tub filled with water and is removed by a steel chain.
MHPSA also finished lifting the gantries of the inclined coal conveyor system onto the concrete plinths. These gantries will house the 3-mm- × 750-mm-wide coal conveyors feeding 390 t/h of coal for each boiler. The incline conveyors rise from the ground under the 1 000 t surge bin coal silo to about 60 m into the boiler house.
The blow-through is one of the final commissioning steps ahead of grid synchronisation and is used to flush out construction debris, cleaning the steam of residue and particles prior to feeding it through to the turbine.
Temporary pipework is used to ensure the turbine is bypassed until specific steam velocity, flow rates and disturbance criteria are achieved so that the steam is cleaned to the point where it cannot damage the turbine. A steel target plate is installed inside the temporary piping under the direction of the turbine supplier, in this case Alstom, to test the cleanliness of the steam.
Meanwhile, Kusile has spent more than R100-million on corporate social investment (CSI) projects. Kusile, in partnership with Alstom, is building a school in the Wilge area estimated at R28-million. It is expected that the school will be operational in the 2016 school year.
In addition to doing work on CSI, Kusile is committed to enterprise development. Since the inception of the project, Kusile has spent more than R6.2-billion on 604 companies in the Mpumalanga area.
Key Contracts and Suppliers
Ninham Shand Consulting Services (environmental-impact assessment, geotechnical investigation and traffic impact); AirShed Planning Professionals (air-quality impact); Jongens Keet Associates (noise impact); Strategic Environmental Focus, or SEF (visual impacts); Makecha Development Association (impacts on terrestrial fauna and flora); Golder Associates, through Ecosun (aquatic-ecosystem impact); Groundwater Consulting Services (groundwater impact); Ilitha Riscom (risk assessment); Northern Flagship Institution (archaeological impact); University of the Free State (impacts on agricultural potential); Urban-Econ (socioeconomic impacts); Seaton Thomson & Associates (planning implications); Mark Wood Environmental Consultants (process review); Eskom, in partnership with Black & Veatch International (project management and engineering services); Mitsubishi Hitachi Power Systems Africa, or MHPSA, a subsidiary of Hitachi Power Europe, or HPE (boiler contract); Actom, formerly Alstom S&E Africa (main turbine area); Alstom (turbine contract and distributed control system); Mikropul, subcontracted by Alstom (axial-flow fans and auxiliary equipment for the turbine halls' ventilation); Murray & Roberts, or M&R (boiler construction contract); Roshcon, a subsidiary of Eskom (enabling civils, terracing construction and site services); Concrete Finishing Equipment (dust filters and silo and environmental safety); the Kusile Civil Works, or KCW Joint Venture (JV), comprising Stefanutti Stocks, Basil Read, Group Five and WBHO Construction (main civil works); Siemens (generator transformers and electrical and auxiliary power); EsorFranki Geotechnical, formerly Franki Africa and Stefanutti Stocks Geotechnical JV, under a subcontract to the KCW JV (piling works for the turbine, boiler and air-cooled condensers); Concor Karrena JV (construction of chimney shells/structures); Tubular (engineering, supply and installation of FGD system); DSE Structural Engineers & Contractors, subcontracted by Genrec Engineering (fabrication of steel columns for boilers 1 to 3); Steel Services Direct, or SSD (steel, pipes and wax plants); GB Bearings (supplier of HSR horizontal bearing assemblies and profile bore bearings); Sulzer Pumps South Africa, subcontracted by Actom (supply of booster and boiler feed pumps); Steloy Castings, subcontracted by Sulzer Pumps South Africa (supply of chrome steel components for the pumps); Clyde Bergemann Power Group, subcontracted by MHPSA (supplier of sootblowers for boilers); Clyde Bergemann Africa (fly ash handling system); ABB (supplier of medium-voltage switchgear and associated equipment); PD Naidoo & Associates, or PDNA, Industrial Projects (main water and wastewater treatment contractor); GE Water Engineered Systems, subcontracted by PDNA Industrial Projects (advanced water and wastewater treatment equipment); Bateman Africa (coal stockyard and terrace materials handling systems); Lesedi Nuclear Services (procurement and supply of the balance of plant equipment); Grinaker-LTA Metals and Minerals (supply and erection of piping, steelwork and free-issue chemicals); US Export-Import Bank, or Ex-Im Bank (loan finance); TBD (railroad construction and combustion water terrace construction phases 1 and 2); Zest WEG Group (auxiliary transformers); Aberdare Cables, a Powertech company within the JSE-listed Altron Group (cables); Konecranes (heavy-duty cranes); Energy Engineered Products (supply of valves) and Turnmill Proquip Engineering (material for boiler ducting).
On Budget and on Time?
The synchronisation of Kusile’s Unit 1 has been delayed from the first half of 2016 to the first half of 2017.
Contact Details for Project Information
Eskom media desk, tel +27 11 800 3304/3343/3378, cell +27 82 805 7278, fax +27 86 664 7699 or email mediadesk@eskom.co.za.
Kusile power station communication department – media relations, tel +27 13 699 7405/ 7377 or email kusilelimelight@eskom.co.za.
ABB media relations, tel +41 43 317 6568 or email media.relations@ch.abb.com.
Actom, tel +27 11 820 5111 or fax +27 11 820 5100.
AirShed Planning Professionals, tel +27 11 805 1940, fax +27 11 805 7010 or email mail@airshed.co.za.
Alstom press, tel +33 1 41 49 2982/3308.
Basil Read investor relations, tel +27 11 418 6375 or fax +27 11 418 6334.
Bateman Africa, tel +27 11 899 9000, fax +27 11 899 4903 or email enquiries-africa@batemanengineering.com.
Bateman Engineered Technologies, tel +27 11 201 2300 or email enquiries@bateman-bet.com.
Black & Veatch media relations and communications, tel +1 913 458 8001 or email Mediainfo@bv.com.
Clyde Bergemann Africa, tel +27 11 704 0580, fax +27 11 704 0597 or email enquiry@cbz.co.za.
Clyde Bergemann Power Group, tel +49 281 815 101, fax +49 281 815 184 or email info@clydebergemannpowergroup.com.
Concrete Finishing Equipment, tel +27 82 788 8265.
DSE Structural Engineers & Contractors, tel +27 11 871 4111, fax +27 11 871 4141 or email dse@grinaker-lta.co.za.
EsorFranki, tel +27 11 771 3906.
Ex-Im Bank, tel +1 202 565 3200.
GB Bearings, tel +27 11 974 1291 or fax +27 11 974 1468.
GE global communications, tel +1 215 942 3409.
Golder Associates, tel +27 12 366 0100 or fax +27 12 366 0111.
Grinaker-LTA Metals and Minerals, tel +27 11 681 2200 or fax +27 11 681 1810.
Group Five, tel +27 11 806 0111.
Hansen Transmissions, tel +27 11 571 9611.
MHPSA head of sales and business development David Milner, tel +27 11 260 4300, fax +27 11 656 3609 or email info@za.mhps.com.
Mitsubishi Hitachi Power Europe, tel +49 203 80 38 0 or fax +49 203 80 38 1809.Jongens Keet Associates, fax +27 21 794 5643 or email jongens@yebo.co.za.
Lesedi Nuclear Services, tel +27 21 525 1300 or fax +27 21 525 1333.
Mikropul, tel +27 478 0456, fax +27 478 0371 or email sales@mikropul.co.za.
M&R group communications executive Ed Jardim, tel +27 11 456 6200, fax +27 11 455 1322 or email eduard.jardim@murrob.com.
Ninham Shand Consulting Services, tel +27 21 481 2400 or fax +27 21 424 5588.
Northern Flagship Institution, tel +27 12 322 7632 or fax +27 12 322 5560.
PDNA Industrial Projects, tel +27 11 566 8300, fax +27 11 566 8600 or email johannesburg@pdna.co.za.
Roshcon, tel +27 11 629 8000 or fax +27 11 626 3460.
Seaton Thomson & Associates, tel +27 12 667 2107, cell +27 82 920 6115, fax +27 12 667 2109 or email seaton@yebo.co.za.
SEF, tel +27 12 349 1307 or fax +27 12 349 1229.
SSD, tel +27 11 828 0439 or fax +27 11 828 2810.
Stefanutti Stocks Civils, tel +27 11 571 4300.
Stefanutti Stocks Geotechnical, tel +27 11 571 4300, fax +27 11 393 3150 or email geotech@stefstocks.com.
Steloy Castings, tel +27 13 933 3331, fax +27 13 933 3653 or email info@steloy.com.
Sulzer Pumps South Africa, tel +27 11 820 6252 or fax +27 11 820 6205.
Tubular, tel +27 11 553 2000, fax +27 11 450 2160 or email th@tubular.co.za.
Urban Econ, tel +27 13 752 4932, fax +27 13 752 4952 or email nelspruit@urban-econ.com.
University of the Free State, tel +27 51 401 2707.
WBHO Construction, tel +27 11 321 7200, fax +27 11 887 4364 or email wbhoho@wbho.co.za.
Konecranes, tel +27 11 864 2800.
Aberdare Cables, tel +27 11 396 8000 or fax +27 11 396 8010.
Zest WEG Group, tel +27 11 827 3458/9 or email info@wegtransformersafrica.co.za.
Energy Engineered Products, tel +27 11 466 1926 or fax +27 11 466 1692.
Turnmill Proquip Engineering, tel +27 16 986 0030 or fax +27 16 986 0127.