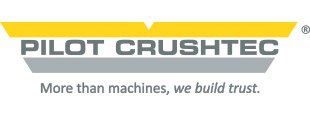
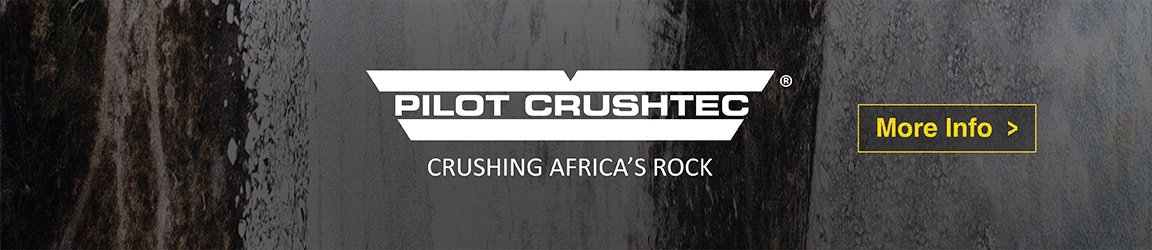
Local mobile coal crushing solution boosts output
Pilot Crushtec says its DoppiaTrac DR400 mobile crusher helps coal mines to boost output while meeting size and quality specifications. The locally designed and manufactured double-roll crusher is a track mounted, self-powered, single-stage double-roll crushing, sizing and stockpiling machine.
“We designed the DR400 from the ground up to give us the flexibility to produce a truly great crushing solution,” says Pilot Crushtec director: technical support Jorge Abelho. “It has proved itself through its combination of throughput, reliability and economy.”
The company notes that the DR400 is Africa’s only locally manufactured, fully mobile double-roll crusher and is capable of averaging production rates from 300 t/h to 350 t/h and reaching 400 t/h. While a horizontal shaft impact crusher is said create more coal fines as a result of impact energy, the double-roll crusher forces material through a constant gap which reduces the generation of fines.
“The crusher uses just enough energy to break the material down to the size of the gap,” explains Pilot Crushtec sales engineer Ben Armitage. “The DR400 generates less than 5% of 0 mm to 6 mm fines, compared to around 12% created by impact crushers – depending on coal hardness and crushing ratios.”
The DR400 boasts a large hopper that is readily fed by loaders or excavators. To increase the average production rate, the unit can be interlocked as part of a crushing train. Connected with a Metso LT106 jaw crusher, the two units can communicate to synchronise the feed-rate. This optimises throughput by automatically adjusting the rate of material moving between the machines. The on-board hydraulic rock breaker on the Metso LT106 also allows oversize material to be quickly broken, avoiding blockages and preventing downtime.
Crushing efficiency is enhanced by feeding material into the crushing chamber at exactly the same speed that the drums are spinning, which minimises attrition and friction, even at high throughput rates.
“The safety features on the DR400 ensure that it is compliant with demanding safety protocols applied by mining companies,” says Armitage. “These include full guarding around all moving parts, access points, nip points and crushing points – as well as pull cords and emergency stops to quickly isolate the unit when necessary.”
He asserts that the Volvo engine delivers the lowest kilowatt per tonne of any mobile double-roll crusher working in the coal sector. Depending on coal characteristics, the engine’s 160 kW output can convert to a ratio of just 0.4 kW/t.
“The fuel consumption is also a significant factor for operators, and this crusher can run on as little as 17 l/h,” he says. “This is achieved with a hydraulic load sensing system and an optimised crusher chamber design, which reduce the power needed to crush the coal.”
Over 25 DR400 machines are currently in operation around South Africa – one of which exceeds 22 000 hours of operation, notes Pilot Crushtec.