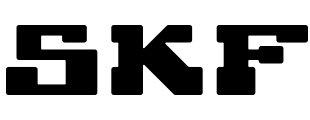
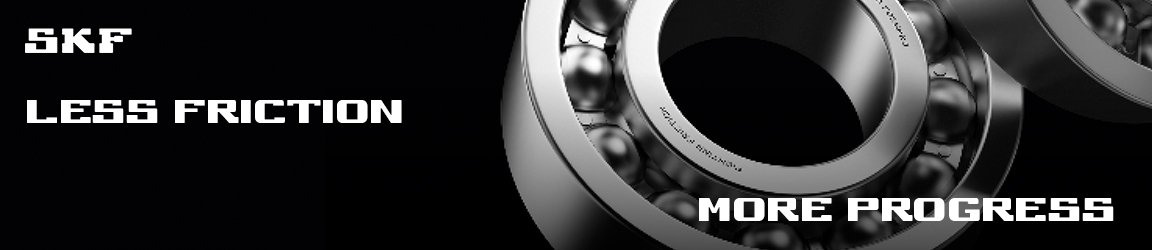
Machined seal solution extends uptime
Seals installed in a vertical boring mill’s hydraulic rotary joint two-and-a-half years ago were recently inspected and found to have remained in working condition and continue to operate optimally, according to the manufacturer.
The seals were installed in response to frequent, costly downtime experienced by a steel manufacturer, owing to the failure of the hydraulic rotary joint on a vertical boring mill. The repair of this component was seen to be expensive and time consuming, owing to the positioning of the equipment. The company explains that despite sourcing original-equipment manufacturer (OEM) spares from the overseas OEM supplier, the problem persisted.
The customer then approached SKF to investigate the problem. Customised K35 design seals were recommended for the vertical boring mill application. According to the company, the piston seal’s individualistic profile for machined type seals, its ability to avoid rolling or twisting in the seal groove and its Hydrolysis resistant seal material made it suitable for the application.
Fifteen custom K35 seals were manufactured on the company’s NG60 Sealjet machine without altering any of the customer’s hardware parameters. The seals were installed and commissioned by the OEM’s local agent, with the support of the seal manufacturer.
In addition, the company shared aspects such as the material and design benefits of the design seals with the customer during the validation of the product.