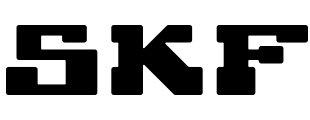
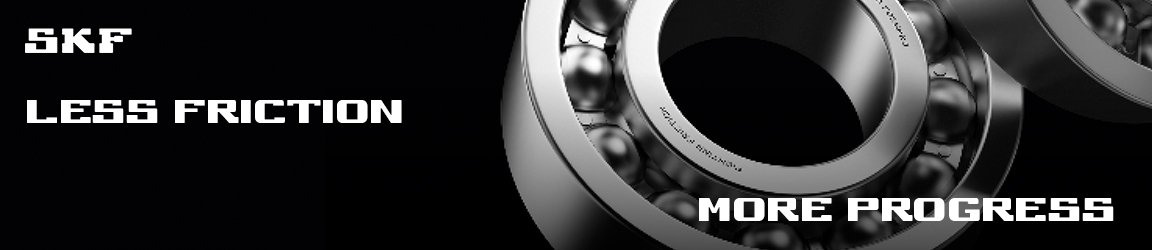
New generation of BEAM and BEAS angular contact thrust ball bearings for machine tools
SKF has developed the double direction angular contact thrust ball bearings for machine tools where space is limited and easy mounting is required. The high-precision bearings serve as support bearings for the ball screws, which are commonly used to drive the various axes in the machine tool.
This application requires a particularly reliable radial and axial guidance, which can be achieved with the bearings of the BEAS (for shaft diameters from 8 to 30 mm) and BEAM series (for bolt mounting and shaft diameters from 12 to 60 mm).
SKF has now optimised the ready-to-mount bearings for higher load capacities and speeds. To this end, SKF engineers have modified the internal geometry of the bearings to increase the dynamic load capacity of the latest BEAS models by up to 17 percent compared to their predecessors. The BEAM models reach up to 20 percent more. These higher load ratings ultimately improve the service life and availability of the machine.
In addition, the latest BEAM bearings allow up to 15 percent higher speeds, depending on size, while the new BEAS versions even achieve up to 35 percent higher speed limits.
The higher speeds can help to reduce the required machining time per workpiece. This further increases the productivity of the machine.
On top of this, the standard sealed and lubricated bearings are equipped with a new, low-contact seal. It prevents the ingress of dirt better than many comparable products, but still causes less friction. This is not only more energy efficient, but also minimises heat development - which on the one hand extends the service life of grease and bearings and on the other hand minimises the thermal deformation of the machine structure.
This in turn contributes to higher machining precision, especially as a newly developed, ball-centered cage made of glass-reinforced polyamide significantly reduces the risk of vibrations.
The more durable BEAM and BEAS bearings are also easy to install due to their increased number of bores. At the same time, the interchangeability of the bearings is fully maintained, thus reducing maintenance effort.