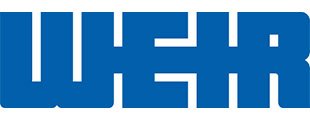
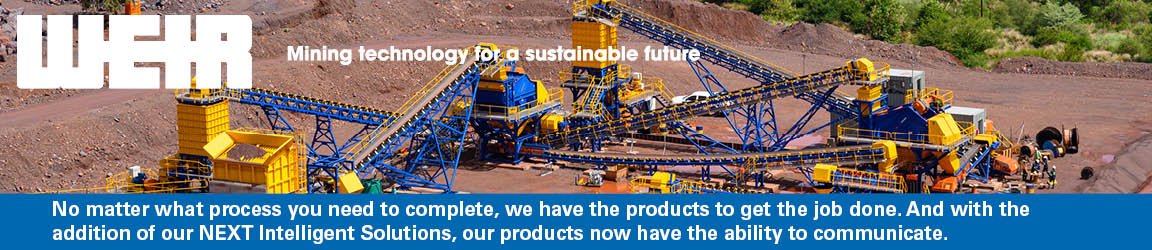
OEM keeps miners’ cost consciousness top of mind
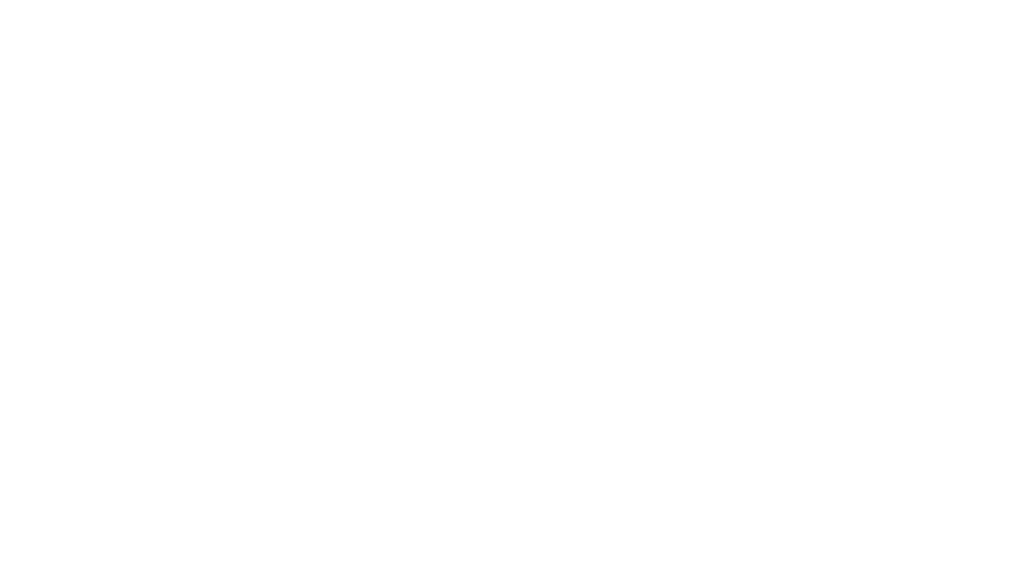
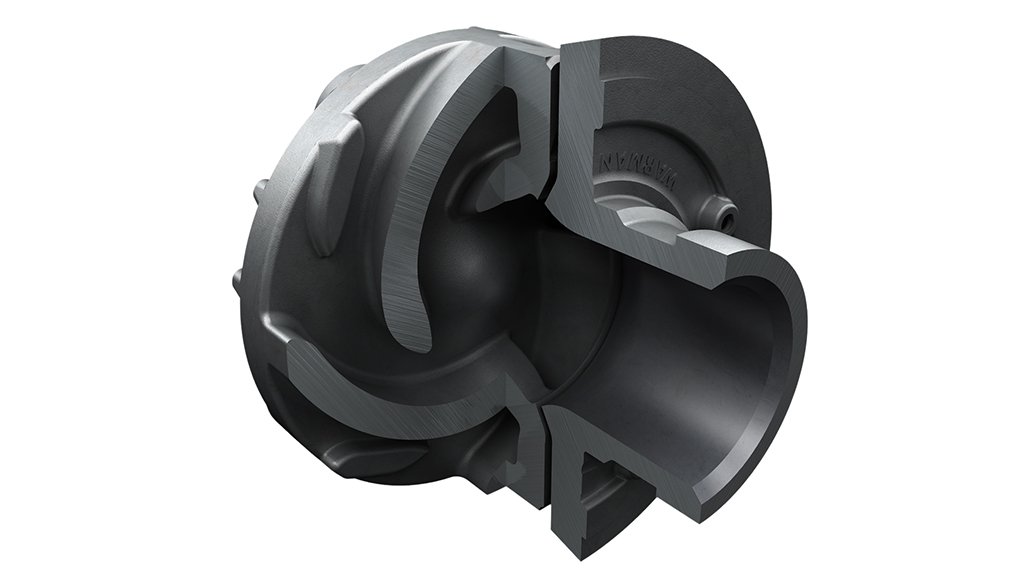
BACKED UP The Warman WRT impeller and throatbush is a culmination of decades of research into wear patterns and hydraulic performance of the Warman AH pump’s impeller and throatbush
At a time when mines have come under even more pressure to maintain profitability and sustainability, original-equipment manufacturer (OEM) Weir Minerals Africa has put operational cost reduction and added value at the forefront of its research and development (R&D) strategy and product offering.
Weir Minerals Africa product manager Marnus Koorts tells Mining Weekly that all its specialised R&D teams – including the wear, hydraulics and advanced materials technology teams – combined their efforts to produce the Warman WRT impeller and throatbush.
He explains that pumps and their components make a significant contribution to a mine’s bottom line, owing to it being one of the largest consumers of energy on any site.
Miners can look to pump optimisation to improve their on-site energy efficiency, as well as save on costs associated with maintenance and downtime, which is especially important amid a constrained economy and global commodity price volatility.
The Warman WRT impeller and throatbush combination is an upgrade to the Warman AH slurry pump, which Koorts mentions is the most widely installed slurry pump in the world, and serves the tough African mining conditions particularly well.
He says the Warman AH pump is reliable, dependable and easy to maintain, but the Warman WRT product makes “a great pump perform even better”.
Weir Minerals understands that mining projects often proceed only when a commodity reaches a certain price and, with high input and operational costs, the company recognised the need to offer an upgrade option for the AH slurry pump to the market that can, ultimately, reduce operational costs for miners even further than the Warman AH.
The company’s assertion that the Warman WRT impeller and throatbush can increase pump efficiency by between 3% and 8%, compared with a standard AH pump, coupled with improved wear life, means that the product upgrade could potentially result in “significant energy and maintenance cost savings”.
Koorts elaborates that the retrofittable Warman WRT impeller can improve wear life in a Warman AH pump by up to 50%, in addition to it using a hydraulically efficient four-vane design to reduce operating costs.
The hydraulic refinements not only lower the pump’s lifetime consumption but also reduce its net positive suction head requirements, making the upgrade an ideal way of compensating for process or feed changes, which often causes a Warman AH pump to become overtaxed.
Further, the Warman WRT product is also compatible with the Warman M and L series slurry pumps.
“Warman WRT technology is the culmination of decades of research into the wear patterns and hydraulic performance of the Warman AH pump’s impeller and throatbush.
“The design includes a unique vanelet on the back shroud, replacing the AH standard five-vane impeller with a modern four-vane design, improving fluid guidance through the pump and representing a step change in impeller design,” Koorts avers.
The Warman WRT is suitable for slurry transportation duties as well as the power generation industry, flue-gas systems, dewatering applications, quarrying and sugar mills.
Weir Minerals Africa said in a statement released in July that the Warman WRT technology had proved its worth at Blackham Resources’ Matila gold mine, in Western Australia. Using a Warman WRT product resulted in double the wear life of the impeller, despite having to work with abrasive and highly viscous slurry.
The new impeller and throatbush reduced total ownership cost for a single pump at Blackham by A$27 000/y, owing to the part’s higher efficiency and longer wear life.
Koorts concludes that all the technical data of the impeller retrofit kit, as well as a full set of performance curves, is available at Weir Minerals Africa’s service centres or support offices.