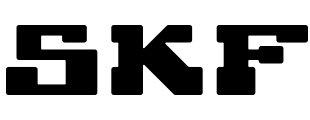
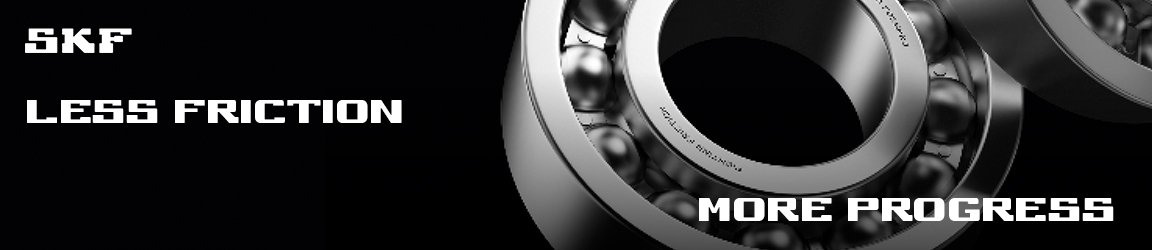
Paper and pulp operation benefits from automated lubrication solution
The use of an automated lubrication solution has shown a number of benefits compared to the manual lubrication of machines, ensuring effective process monitoring and timely, accurate lubrication.
The Maxilube automated system from SKF was recently installed at a paper and pulp plant in Tunisia, operating in extreme temperatures with machines that allowed limited access to lubrication points while running.
During a planned shutdown, SKF Tunisia successfully installed and commissioned the system, collaborating closely with their local authorised distributor and subcontractor.
Equipped with a combination of SG dual-line and VPG progressive dividers, the Maxilube system services 130 lubrication points on the paper machine.
“This advanced configuration allows for precise control of grease dosage at each point, ensuring optimal performance and efficiency,” explains SKF sales engineer: lubrication Northwest Africa Hassan Missaoui. “We also replaced the previously used concurrent known grease, with LGHB 2 grease that is specifically suited to this application, enabling us to accurately calculate the exact quantity of grease required for optimal bearing lubrication.”
Missaou adds that this calculation also provided a clearer understanding of the actual expected grease consumption per bearing, resulting in a more efficient and measurable reduction in overall grease usage for the customer, noting: “In addition to reducing grease consumption, the implementation of this complete lubrication solution also significantly extends bearing life by improving lubrication performance, ultimately leading to better resource utilisation and substantial cost savings for our customer.”
The new system also almost completely eliminates direct human interaction with machinery, significantly lowering the risks associated with working in high-temperature environments near high-speed equipment.
By enhancing lubrication monitoring and enabling predictive maintenance, the customer says that the new automated lubrication solution has improved operator safety, reduced equipment failures, extended bearing life and increased machine uptime, all contributing to more reliable production. In addition, grease consumption was optimised, reducing operating costs and environmental impact. The customer also noted cost savings from reduced bearing replacements and lower grease usage, as well as a boost in uptime, leading to higher productivity and improved output.