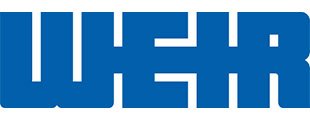
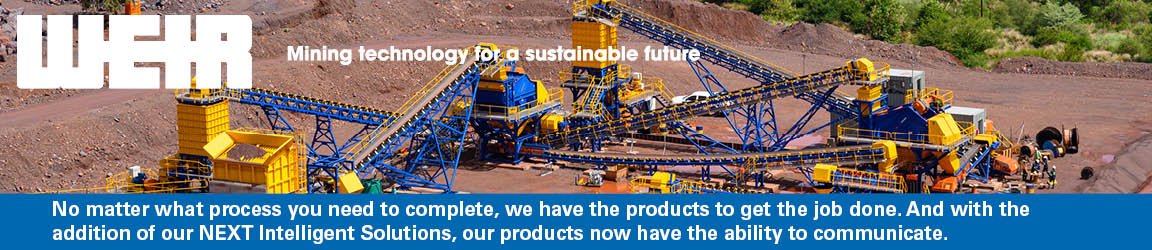
Plant pumps commissioning under way in Limpopo
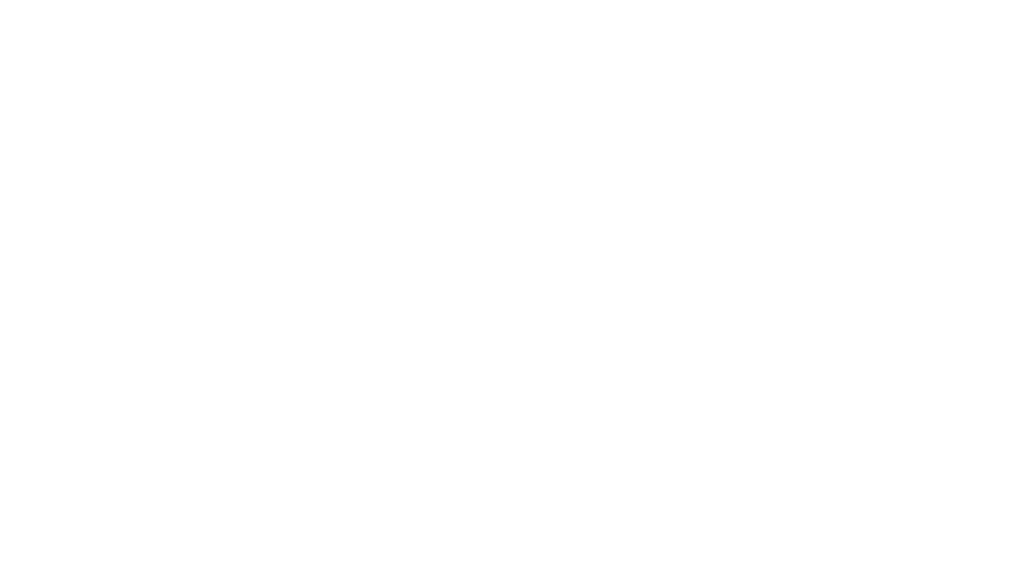
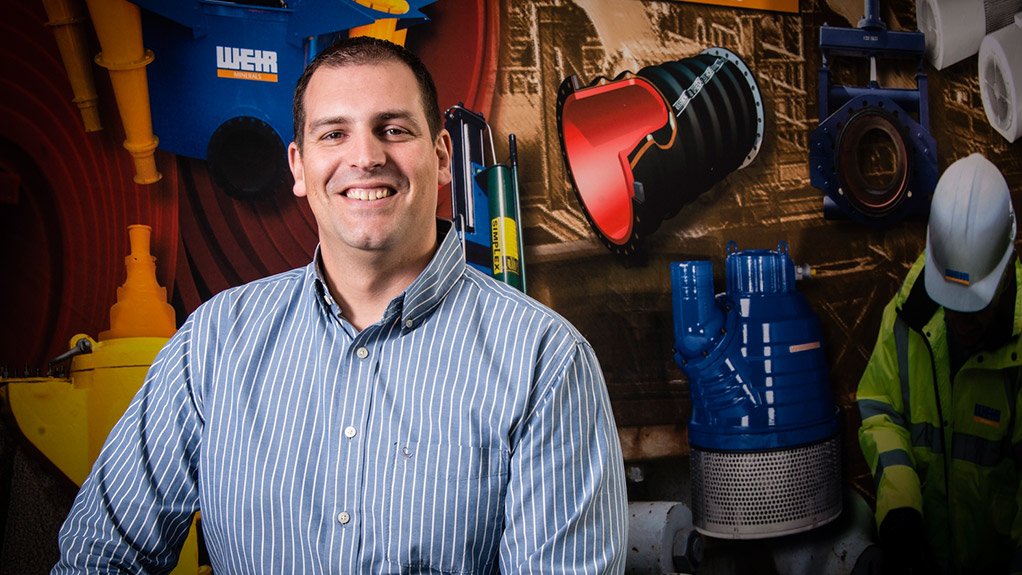
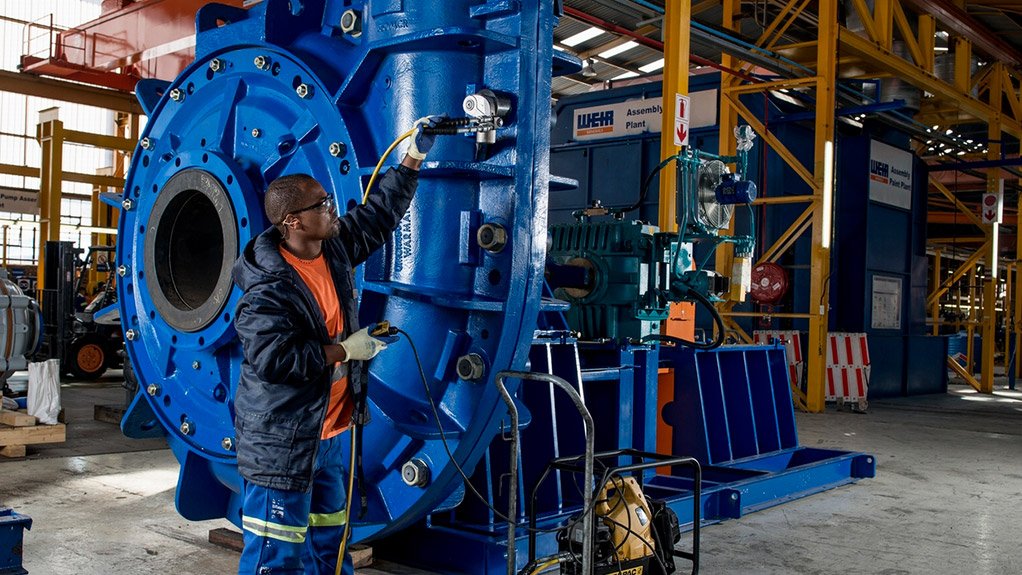
RUI GOMES Weir Minerals works closely with end-users to ensure that they receive the best performance from their on-site equipment
WARMAN WBH Weir Minerals Africa manufactures these pumps locally at its Isando and Alrode facilities in Johannesburg, as well as at Heavy Bay Foundry in Port Elizabeth
Slurry equipment solutions provider Weir Minerals Africa is assisting in commissioning the plant pumps at a platinum mine in Limpopo’s Waterberg area.
The project scope includes the supply of several Warman WBH slurry pumps, with pump sizes ranging from 75 mm to 150 mm, notes Weir Minerals Africa slurry pumps product manager Rui Gomes, adding that the project is scheduled for completion next month.
He highlights that the WBH pumps, which Weir Minerals started supplying at the beginning of the year, have been fitted with expeller centrifugal seals. The expeller seals are designed to eliminate the need for an external water flushing system, typically in the form of gland service water, which is used to seal the pumps at high intake pressures.
“We specified the pumps on this project to ensure sufficient sealing using an expeller seal, which is essentially a centrifugal seal. This sealing arrangement eliminated the need for gland service water, thereby eliminating the need for water consumption to seal the pumps,” he asserts.
Meanwhile, Weir Minerals started the delivery of additional WBH slurry pumps to a brownfield copper project in Limpopo, in June. The supply contract includes rubber- lined 300WBH slurry pumps, which is the largest pump in this range that Weir Minerals manufactures locally, highlights Gomes.
The project is scheduled for commissioning in the third quarter of next year and a number of these pumps employing the latest technology have been specified, with the resulting benefit of significantly improved efficiency, compared with older designs.
Gomes explains that Weir Minerals’ latest technology developments are designed to reduce not only energy costs through optimal hydraulic designs but also maintenance costs by reducing the replacement spare parts required through improved wear life, ultimately reducing a pump’s total cost of ownership.
The WBH pumps address the energy costs through improved efficiency impeller and volute profiles, as well as accurate specification of pumps for specific duties and applications. In addition, proper pump selection will positively improve operating performance and, in most cases, lower the energy-consumption rate, he adds.
Conditions at existing mining operations change, which, Gomes notes, could be because of several environmental changes, including varying feed sources or mining conditions, or increased production demands and climate, resulting in the pumps having to operate under different conditions than they were originally specified for, potentially causing an increase in pump failures.
“To avoid increasing energy costs, Weir Minerals works closely with end-users to ensure that they receive the best performance from their on-site equipment. By understanding end-users’ pumping requirement, we can ensure that a pump is used in applications where it can deliver optimally, rather than according to its initial design specifications only.”
Gomes adds that wear is one of the major contributors to pump failures. A common phenomenon is the increased gap between the impeller and the throatbush, which is caused by excessive recirculation of material within the pump casing.
As part of Weir Minerals’ ongoing development, the WBH pump was designed with a unique adjustment mechanism for the throatbush, which allows for the adjustment of the gap between the throatbush and the impeller. The adjustment mechanism, accessed through a single point of contact on the outside casing of the pump, does not require the pump to be completely dismantled in order to conduct this maintenance. This reduces downtime and provides a safer operating environment.
Gomes highlights that, in addition to the benefit of ensuring pump efficiency, the adjustment mechanism also improves the effective life span of wear parts, further reducing operating costs.
“Having an understanding of what happens in a pumping system enables us to counterbalance the adverse effects,” he asserts.
New Launch
Gomes points out that Weir Minerals will expand its Warman WBH range of pumps next month with the addition of the 25WBH and 40WBH slurry pumps.
The range currently comprises pumps with a discharge diameter ranging from 50 mm to 300 mm.
Gomes explains that the new pumps are in the final design process, after which they will be manufactured, tested and launched onto market. “We have completed the initial design and internal testing of the pumps and are considering which of the group’s manufacturing facilities are best suited to produce the units.”
The units will be manufactured at Weir Minerals Africa’s Isando and Alrode facilities, in Johannesburg, with the larger components being manufactured at Heavy Bay Foundry, in Port Elizabeth.