Supplier keeps up with tech revolution
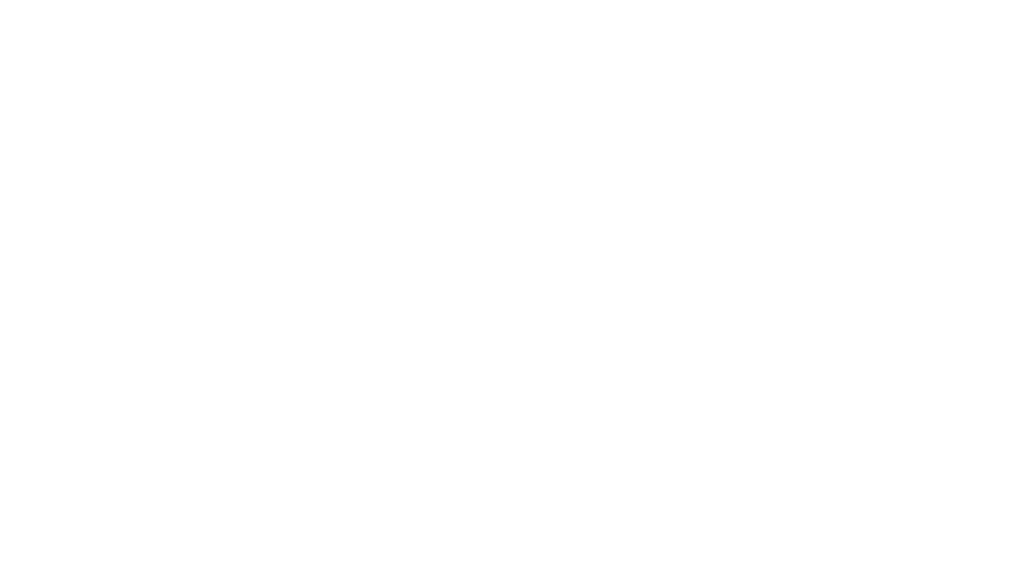
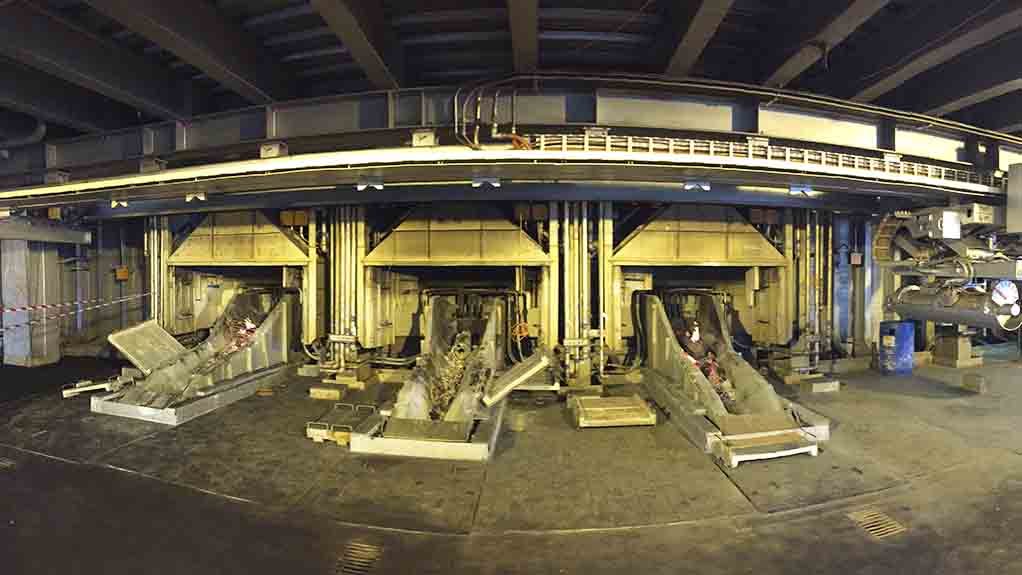
BLUE GROUP SMS group has implemented its range of BlueTechnology offerings at a greenfield plant in Russia for the recycling of waste electrical and electronic equipment
Based on its BlueTechnology philosophy, metallurgical industry supplier SMS group has significantly broadened its expertise in processing, supplies and services for nonferrous metals production over the past year to meet the highest requirements of customers.
“BlueTechnology in nonferrous metals production takes into account the importance of sustainability for production lines and raises awareness of ethical and ecological metals production,” SMS group nonferrous metals and alloys VP Dr Rolf Degel tells Mining Weekly.
These technologies include the group’s BlueSmelter, BlueMetals, BlueCat, DrySlag, PowerSlag and BlueControl, as well as hydrogen-ready systems.
“There has been an increase in demand for hydrogen burners in Europe, and this demand is expected to follow in other countries,” he enthuses.
Degel explains that BlueTechnology has been asserted as a key enabler of a circular economy, enabling environmentally balanced solutions, including efficient water and off-gas treatment; carbon neutrality; minimised power, media and water consumption, as well as reduced waste accumulation.
BlueTechnology also includes “highly efficient processes” that maximise metal and by-product yield, as well as recycling rates.
Digital transformation allows for transparent, accurate process modelling with real data calibration for efficient and predictive operation practice.
Degel suggests that the BlueMetals Technology is the most efficient, profitable method for waste electrical and electronic equipment (WEEE) recycling.
SMS provides solutions for the efficient recycling of WEEE to recover the contained noble materials, such as gold, silver, platinum, palladium, copper, nickel and cobalt.
The company provides custom-fit solutions as part of the BlueMetals family, which recovers up to 98% of these metals and completely converts them into pure products.
The central furnace of SMS group’s WEEE concentrate recycling concept is either the BlueSmelter or the top blown rotary converter (TBRC).
The BlueSmelter can handle lower-grade WEEE concentrates with higher organic contents, with one plant being able to process between 3 000 t and 120 000 t of e-scrap concentrate every year.
It can be installed as a complete greenfield plant or as a supplement to existing copper or nickel smelters.
“When high-grade WEEE concentrate is available, the TBRC can be applied as the primary smelter and refinery producing raw copper,” says Degel.
He points out that SMS group has successfully commissioned a complete WEEE recycling plant, with one TBRC as a primary smelter, at luxury automobile company Aurus, in Mtsensk, Russia.