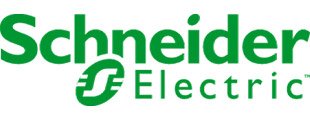
+27 (0)11 0461900
Private Bag X139 Halfway House 1685
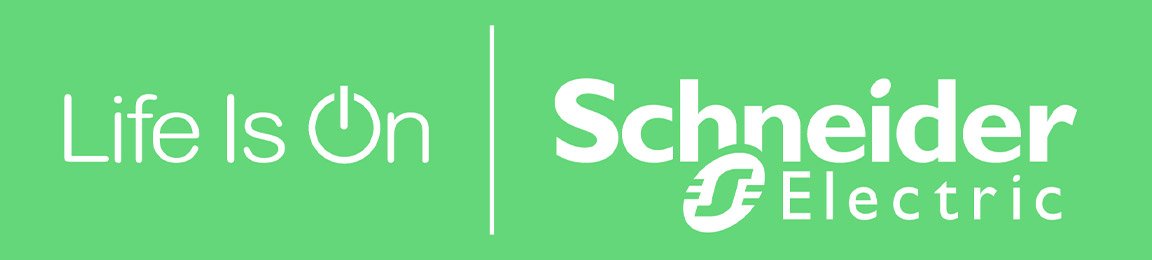
Predictive maintenance is built on digitisation and automation
By Obinna Uche, Sales Director, Power Systems Division at Schneider Electric Anglophone West Africa
The predictive maintenance marketplace is set to grow by at a CAGR of 17% until 2028, according to the Predictive Maintenance and Asset Performance Market Report 2023–2028. According to the report, the marketplace was valued at $5.5 billion in 2022 already which reinforces its considerable role in organisations’ asset maintenance and monitoring efforts.
Driving this growth, says the report, are industries with heavy assets and high downtime costs, such as mining, minerals and metals.
In West Africa, we’ve seen digitisation and automation emerge as two critical components in companies’ predictive maintenance efforts. Digitisation entails organisations integrating sensors and connected devices across their operations. These devices enable them to collect valuable data on equipment health, performance trends, and potential failure patterns.
Access to accurate, real-time data allows maintenance teams to make informed decisions, prioritise tasks, and allocate resources effectively.
In the case of automation, it allows companies to swiftly and accurately processing this data. Advanced analytics and machine learning (ML) techniques are used to develop predictive maintenance algorithms and models.
These tools then enable companies to forecast equipment failures with precision, facilitating timely maintenance interventions that prevent operational disruptions It also aids in planning for future production and market trends.
Furthermore, automation enhances the implementation of predictive maintenance by utilising smart products and equipment that can collect and process data independently. These devices are equipped with processing capabilities that enable them to raise alarms when anomalies are.
It’s a logical and prudent move
For West African businesses, moving from reactive to proactive maintenance practices offers numerous benefits:
- Efficiency - digitisation and automation enhance operational efficiency, minimising downtime and maximising productivity.
- Profitability – proactive maintenance strategies reduce maintenance costs and prevent revenue loss from unplanned shutdowns.
- Predictive Maintenance - leveraging data analytics and ML, businesses can anticipate equipment failures and take timely actions to prevent disruptions.
Schneider Electric’s EcoStruxure IoT architecture integrates IoT devices, automation, and data analytics to enable real-time monitoring, anomaly detection, and predictive maintenance scheduling.
EcoStruxure operates on three layers: Connected Products, Edge Control and the Apps, Analytics, and Service. This structure ensures comprehensive coverage of all aspects of predictive maintenance, from data collection to actionable insights.
In the case of Schneider Electric’s EcoStruxure Plant offering, it provides predictive maintenance through advanced analytics and real-time data evaluation:
- Data collection: EcoStruxure Plant collects live data from critical connected assets within the plant environment.
- Advanced analytics: The system applies sophisticated analytics to this data, identifying potential threats and anomalies.
- Early warnings: EcoStruxure Plant provides early warnings for equipment issues, allowing proactive intervention.
- Decision-Making: Users can choose to take action themselves or leverage Schneider Electric’s Service Bureau for expert assistance.
Lastly, Schneider Electric offers a range of services to help businesses optimise their maintenance strategies. These services include audits and modernisation, consulting, implementation support, and ongoing maintenance.