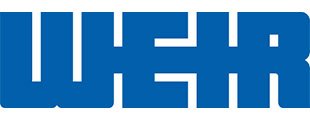
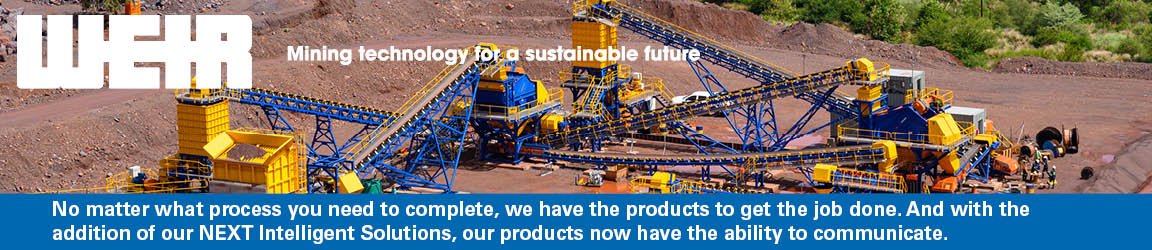
Pumps manufacturer to launch mechatronics solution this quarter
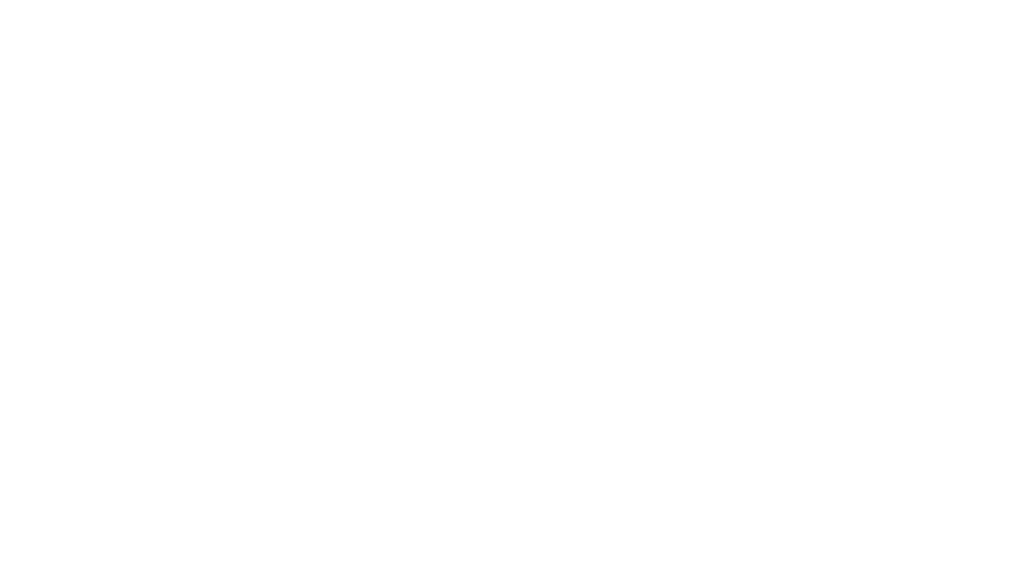
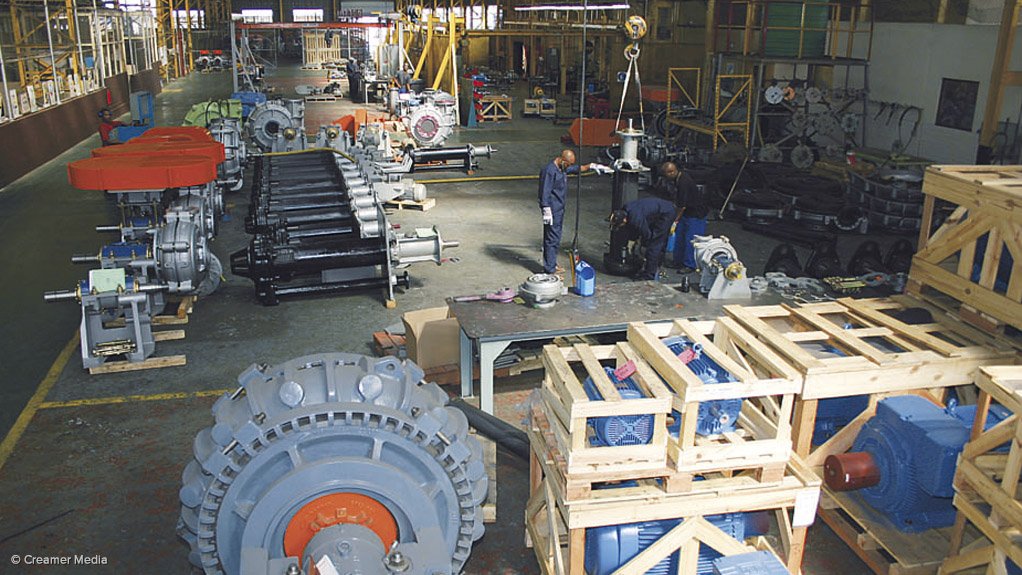
PROBLEM PREDICTION Weir's design teams are looking for solutions to challenges that have yet to materialise
Industrial equipment supplier Weir Minerals will launch its mechatronics solution, Synertrex, before the end of the first quarter. The solution leverages the Internet of Things (IoT) – combining integrated equipment technology with everyday electronic and mechanical equipment with network connectivity – to capture pertinent equipment data and relay it to service centres, service technicians, their customers and, ultimately, to Weir’s design centres for trend monitoring, proactive components supply and product improvement.
Weir Minerals Africa and Middle East sales and marketing director Rob Fawcett explains that the Synertrex system comprises hardware and software for industrial equipment control, monitoring and analysis. “Once we have units on the ground, we’ll be able to extract equipment data, interpret it and act on it.”
The the system will inform the service personnel that there is a problem with a piece of equipment or component thereof at a customer’s site and prompt the organisation to react well before the customer realises there is an issue, Fawcett adds, further stating that “it will completely change the philosophy behind maintenance and service provision”.
He notes that Synertrex’s offering is enhanced through Weir’s partnership with software company Microsoft and computer technology company Dell: “Microsoft developed and provides the predictive software, while Dell developed and provides the robust and adaptive hardware, which remains functional, even in the extreme conditions found in many areas we operate in throughout the world.”
The Synertrex system can record, organise, transmit and manipulate data for various applications, including asset management, product inspection, condition monitoring, predictive and prescriptive analytics, the generation of predictive and preventive maintenance reports, asset tracking and, with further development, will even enable the remote control of industrial equipment and processes.
The Web-based, nondownloadable software will be developed to enable Weir to monitor the ordering of inventory, thereby enabling logistics management and asset monitoring services in terms of inventory control and management related to the specific equipment monitored.
The interactive, secured-access website of the Synertrex system will feature technology that enables users to input, access and synthesise information, generate reports, forecast the life of their assets and troubleshoot problems.
Fawcett says the ultimate aim of Synertrex is to provide a system that is self-learning, rather than just a repository of information; its predictive capability will also enable users and customers to become more proactive.
“The current mining downturn has forced companies to push equipment to new extremes . . . to increase production and limit downtime . . . This means that a standard, regimented maintenance programme is no longer viable, because the equipment is no longer working under standard, regimented conditions.”
He notes that Synertrex as a brand will be fluid and adaptive to developments in IoT and technology. Weir will introduce system and software upgrades as required to remain relevant to customer needs.
Novel Pumping Solutions
Fawcett states that Weir Minerals has established itself firmly as a solutions provider rather than just an equipment supplier. He notes that this is evident in the ways in which the company has adapted its technology for new or alternative applications, generating total cost of ownership (TCO) savings for clients. He cites a South American project, where Weir staff converted potential energy produced by a slurry pipeline into electricity. In South America, as a result of the mountainous geology, mines often pump slurries down steep declines, he says.
“A lot of the time, mining companies need to decelerate the slurry as it gets to the base to reduce equipment wear. Our engineering team, working with the customer, developed a solution using the potential energy stored in the slurry to generate a small amount of electricity.”
The team is investigating the viability of using this solution to drive the mine’s return water pumps.
Fawcett believes that similar solutions will be investigated and implemented more often, as global electricity costs are expected to continue increasing. “These kinds of regeneration schemes will become more viable to mines in the future.”
He also points to Weir’s willingness to break from the norm by altering its existing technology, such as the fundamental design areas of its MCR mill circuit pump, to meet client requirements.
Weir introduced a preswirl technology for the Warman MCR range of products in late 2014. “Mill slurries tend to have particle grading from fine to large, with the heavier particles tending to settle. When these particles reach the pump’s impeller, they have a lower velocity than the pump’s rotational velocity, increasing shock loading causing wear. The preswirl technology significantly reduces the shock loading, improving impeller wear."
Previously, this addition was implemented only in specific cases, but, with the success to date, it will become standard across the mill circuit range.
“The mill circuit design team is also investigating variations on Weir Minerals’ leading R55 rubber compound. Initial results suggest that we can achieve at least a 12% improvement on wear.
“Additionally, our material sciences division in Sydney, Australia, continues to analyse the microstructure of metals and their interaction with complex slurries, testing various types of Hyperchrome alloy and the use of new alloy materials as part of Weir’s efforts to reduce TCO,” Fawcett explains.
Regional sales manager William Cumming adds that the adaptation of technology often furthers product development, citing the introduction of the Warman MDC pump, a spin-off of the MCR pumps range.
The MDC pump was specifically designed for use in dense-media separation (DMS) plants. During the recent installation of six MDC pumps at a coal mine in Middelburg, Mpumalanga, Weir achieved a 60% improvement in DMS plant start-up time. “It used to take the company about 30 minutes to start module and, only then, could they feed coal into the DMS. Now, it takes about ten minutes [per] module. Further, the stability around the cyclone pressure has also improved,” Cumming explains.
Fawcett says Weir Minerals’ product and process innovation is focused on cost reduction and improving efficiencies. It is constantly exploring new possibilities. “Our design teams are looking for solutions to challenges and problems that don’t even exist yet.” This, he concludes, is why Weir remains one of the most successful pump manufacturers to date.