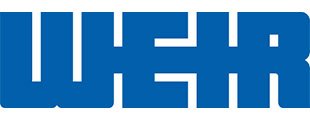
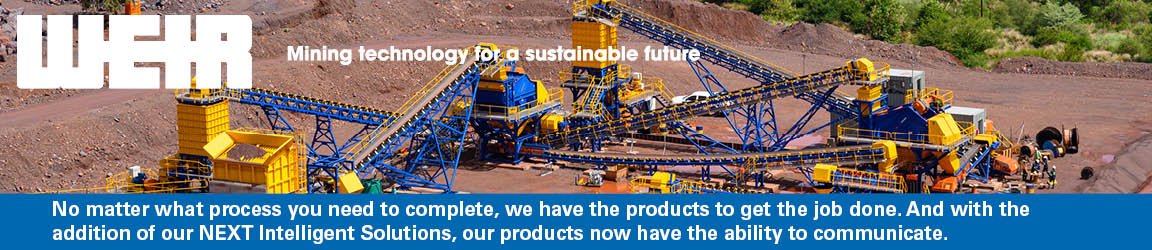
Rubber increases wear life
Mines are well aware of the significant cost savings that can be achieved by using rubber to increase the wear life of equipment; however, selecting the right product for the application is vital. Rubber lining is a highly skilled process which – when done correctly, with the correct type and thickness of rubber – can contribute considerably to the life and profitability of a plant.
Perhaps the first issue to clarify is that there is no single lab test to provide a definitive answer, says engineered processing solutions provider Weir Minerals Africa rubber products, hoses and spools product manager Yatheen Budhu.
The industry standard test for rubber materials is the ISO 4649 dry abrasion test; however, most wearing materials on a mine exist in a wet environment, he says.
“For this reason, our Weir Minerals specialists developed a modified version of the ISO 4649 test, the Wet Abrasion Resistance Index (Wet ARI) test which can be used for wet abrasion testing and is better matched to what actually happens on the mine. The test was developed specifically to replicate wet slurry wear conditions for elastomers and over many years of testing has become the standard by which we can predict the wear of not only our rubber, but that of our competitors and then rank these side by side.”
He points out that the same wear material – such as slurries, sand or aggregate – will behave differently in varying conditions. For this reason, Weir Minerals’ Wear Testing Programme includes unique tests such as the Weir Coriolis test, which is particularly suited for mill pumps, as well as the Wet ARI test.
“The range of options can seem overwhelming, but it is vital to select the right material for the job,” he emphasises, adding that getting this wrong means shorter wear life and raises the risk of premature failures that could lead to unplanned stoppages for maintenance.
Budhu highlights the proven ability of natural rubber to withstand abrasion, especially when its composition is close to the natural latex found in the rubber tree. This is where Weir Mineral’s innovative manufacturing process makes all the difference.
“Each additional step in the production of rubber can damage its molecular chains and compromise the raw natural rubber’s excellent abrasion resistance,” he explains. “Through our unique liquid phase compounding process, we ensure that our premium rubber retains the essential properties of raw natural rubber and this allows it to deliver excellent wear life.”
After almost a century of successful operation in both industrial and mining applications, Linatex rubber is renowned for reducing long-term wear caused by fine particles, including the wet and abrasive conditions in mining. It is especially suitable for low angle applications, and its uses include the lining of pumps, piping, hoses, chutes, valves and tanks.
Where coarser materials are involved, Weir Minerals offers its Linard range of natural rubber compounds. This material combines high flexibility with excellent resistance to cutting, says Budhu. Linard compounds also resist deformation while providing anti-stick properties.
“The choice of liner solutions goes beyond natural rubber to include synthetic rubbers. The latter are formulated to be used where corrosive chemicals and high temperatures become a factor,” he says.
For these applications, Weir Minerals developed its Linagard range of synthetic rubbers. These withstand the effects of leaching acids and hydrocarbons, as well as slurries which are hotter than 70 ºC.