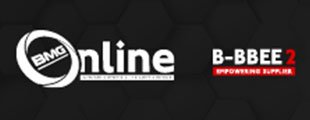
+27 (0)11 620 1500
Droste Crescent, Jeppestown, Johannesburg 2043, South Africa
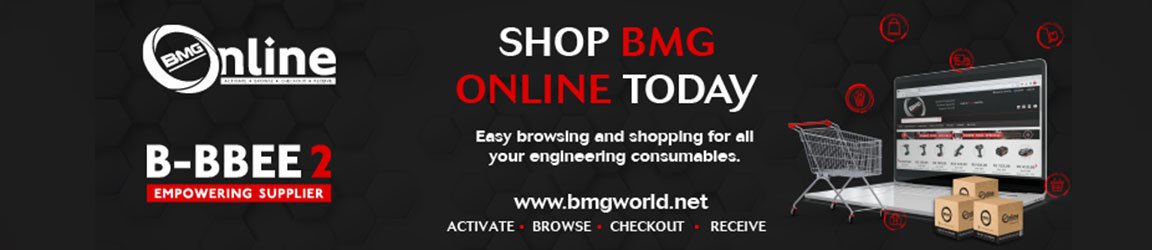
SAPICS members visit BMG World distribution facility
BMG hosted 30 SAPICS members at the end of last year, for a walkthrough of the BMG World distribution facility in Johannesburg.
“BMG World - our 16 000 m² distribution facility - serves as a central hub from which we support over 70 000 customers operating in diverse industries, across at least 15 countries,” explains Chantelle Shepherd Pietersen, BMG’s Logistics Manager, “Our state-of-the art facility reflects BMG’s ability to efficiently provide integrated engineering and supply chain management solutions throughout the sub-Saharan region.”
“It is a pleasure for BMG to be associated with SAPICS – a professional organisation that strives to elevate, educate and empower the community of supply chain professionals in South Africa and across the continent. BMG enjoyed hosting our SAPICS visitors on a guided walkthrough of various areas of BMG World – including the receiving and sortation facilities, the advanced conveyor system, as well as the distribution processes.”
Functional operations at BMG World include a product warehouse and distribution centre for the entire product range, a manufacturing centre and general engineering workshop. There are also specialist assembly and repair workshops for drives, conveyors, hydraulics and pneumatics, as well as electric motors, electronics, gaskets, lubrication systems and filtration.
BMG has invested in the latest materials handling equipment, including high bay and narrow aisle turret trucks, to optimise volumetric efficiency. Specialised machinery also includes dock levellers for efficient container handling and a regenerative 200 kW load test rig that has been developed in response to demand from local industry for absolute reliability from new gearboxes. This system uses the latest technology to transmit and apply loads of up to 30 000 Nm, with the lowest energy consumption. This is sufficient torque to test the majority of Paramax gearboxes in BMG’s range, within at least a third of each unit’s rated capacity.
BMG’s technical resources centre offers services which positively influence a company’s operating efficiencies, by ensuring maximised mechanical reliability of plant and machinery.
The technical resources team partners with each customer to ensure dependable solutions – from the initial design concept, specification, manufacturing quality control, commissioning and support of equipment in use. Services include technical applications consulting, product and system design, on-site process analysis, lab and on-site oil analysis, product quality control and assurance, as well as condition monitoring services.
BMG World is also home to field services. A team of mobile technicians, with specialist technical skills and equipment, conducts breakdown and routine maintenance on all types of plants; carrying out trouble shooting and advising on productivity improvements, to ensure the highest level of plant availability and reliability.
BMG’s ISO 9001:2008 internationally recognised quality management system endorses the meticulous standards and procedures that have been developed and entrenched throughout the Group. Quality is of paramount importance and the procedures and instructions that have been developed and entrenched, ensure that the quality of all products and services meet local and global specifications and exceed customers’ expectations.
The BMG team is committed to providing 24-hour customer process support for production efficiency and reliability centred maintenance. These critical services are enhanced by advanced technical and design support and professional supply chain management solutions.
The company - which was established as a single bearings shop in Durban nearly 50 years ago - now has a branch network of almost 100 outlets across Africa.