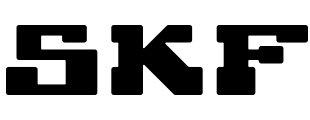
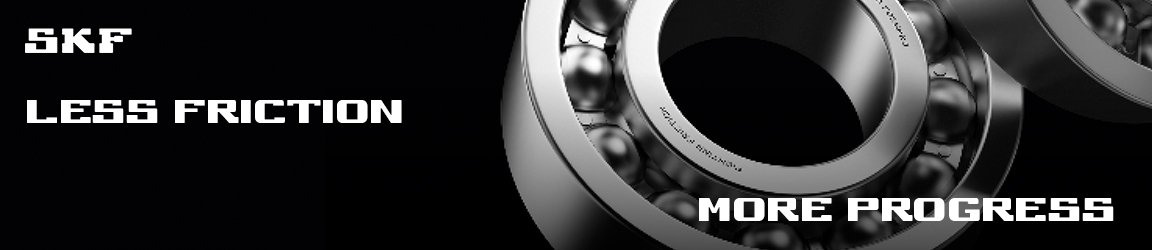
Sealing solutions for wheel end maintenance
According to industry estimates, up to 90% of premature wheel bearing failures are a result of incorrect seal installation and subsequent leakage of lubricant.
A seal formulated from hydrogenated nitrile butadiene rubber (HNBR) elastomeric material is now available. It has stated high temperature capabilities of up to 149°C across a range of road and driving conditions and the promise of an extended lifespan in contaminated conditions. The use of HNBR material is aimed at extending the service life of wheel end components.
The Scotseal PlusXL seal from SKF has been tested and is compatible with a number of synthetic lubricants. Its unified design offers a fresh running surface for sealing lips and aims to repel road contaminants, thereby extending service intervals.
Comprising a ‘fat footprint’ with adhesive-type properties that lock onto the spindle, the seal is able to fit on worn spindles too. Specialised ethylene propylene diene material-blended nitrile ID seals over the gripping shaft of imperfect spindles to remove the leak path. The blend of elastomeric material and an outside diameter design enables the seal to be installed without special tooling. The lube ID, O.D. and the seal are pressed into the hub, which could further extend wheel end life and prevent repeated applications.
Another seal design from the company is the Bore-Tite coated Scotseal Classic which features three lips - a factory pre-lubed spring-loaded primary sealing lip, a dirt exclusion lip and an outer bumper lip that works as a preliminary excluder for extended durability.
The seal’s unified design provides a running surface for the three sealing lips, aimed at preventing oil leaks and contamination ingress.