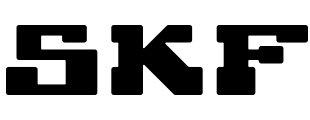
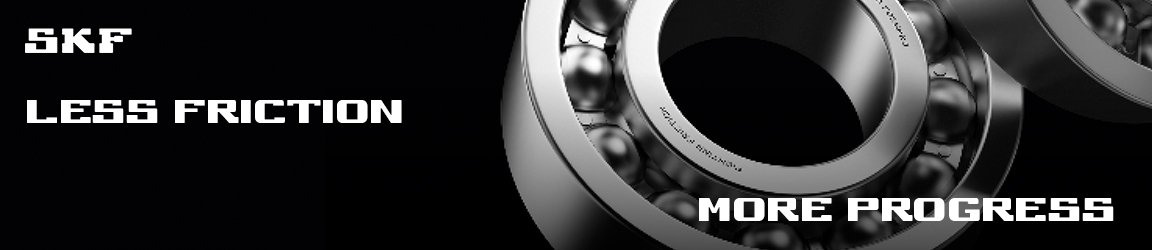
SKF/Lincoln’s CNA-lube audit hits the solutions sweet spot for a key customer
The upgrade by SKF/Lincoln of a lubrication store at Durban Harbour has boosted bearing life and machine availability, subsequently delivering significant cost savings for a key customer who is involved in sugar storage for mostly export purposes.
The customer was concerned over their lubrication practices and general procedures and, having heard about the lube audit through a SKF authorised distributor who was servicing them, requested more information. The SKF/Lincoln team was subsequently called in to conduct a Customer Needs Analysis (CNA)-Lube audit at three sugar terminals at Durban Harbour.
The audit identified the customer’s lubrication store as an area of serious concern. According to SKF Product Manager – MaPro, Eddie Martens, the audit raised flags around extremely high contamination risks. “Alongside a lack of organisation, the absence of dedicated dispensing tools compromised dispensing procedures as the customer had no control over lube dispensing; this was also resulting in costly wastage. Additional areas of high concern were contamination and cross-contamination of oils as well as the inadvisable practice of working on a first-in-first-out principal for the lubricants, especially when it came to the lubricants used for servicing the fleet of wheel loaders.”
Martens points out that contamination contributes to 14% of all bearing failures while poor lubrication, the use of incorrect lubricants and inappropriate lubrication procedures can account for up to 36% of bearing failures. He stresses that in total this contributes to 50% of all bearing failures. “We recommended a three-phase solution; the first phase would comprise an upgrade of the lubrication store followed by phase 2, the fitment of System 24 lubrication systems on the conveyors, and finally the installation of centralised lubrication systems and Muster Fire Suppression systems on the customer’s wheel loaders during the third phase. Understanding the risks related to contamination of the lubrication, the customer gave us the green light to proceed.”
SKF/Lincoln’s scope of supply for the lubrication store upgrade included the installation of five drum pumps and one Versamatic AODD pump complete with hose reels and dispensers. “The pump units will improve control over dispensing by ensuring that correct dispensing procedures are being implemented and adhered to for clean, accurate dispensing of the customer’s lubricants and paraffin,” explains Kevin Mills, Regional Sales Manager – KZN & Eastern Cape at SKF/Lincoln. “Additionally, by significantly reducing the risk of contamination, our solution will unquestionably lead to cost savings for the customer over the long term.”
Phase 1, the lubrication store has been completed. Phase 2, which involves the gradual implementation of System 24 single point lubricators onto the conveyer systems throughout the plant, is currently in progress. Phase 3, the conversion and upgrade of the loading vehicles, is also in progress which Mills explains is being carried out as and when the machines are available. He confirms that SKF/Lincoln will be providing training to the customer on the machine’s lubrication systems once these upgrades and installations have been completed. He adds that the dispensing systems in the lube store are straight forward so no training is required.
“Ultimately, all lubrication points will eventually be serviced either via single point lubricators or automated lubrication systems, which will reduce the need for time consuming and costly manual lubrication,” notes Mills. “And as we continue to roll out these system installations, more cost savings will follow for the customer. Our target is to have this plant a fully SKF-lubricated facility by the end of 2022.”
“When we were originally approached to do the audit, we stressed that we were not looking for a customer but rather a partner as we see this as a journey of solving problems together,” says Martens. “And I can say with confidence that we are walking the talk. Since the audit commenced in Q2 2021, it’s been an on-going process as we develop more opportunities that the initial audit uncovered. Also, importantly, the CNA-Lube audit has enabled us to highlight SKF’s ability to provide solutions in all areas, not only bearings. Moreover, showcasing our expertise in supplying a wide range of solutions has resulted in the customer placing further orders with us and requesting an introduction to some of our other solution platforms.”