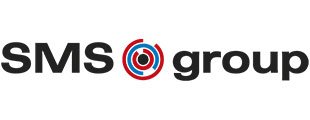
+27 (0) 11 480-1800
204 Rivonia Road, Morningside, Sandton, 2196
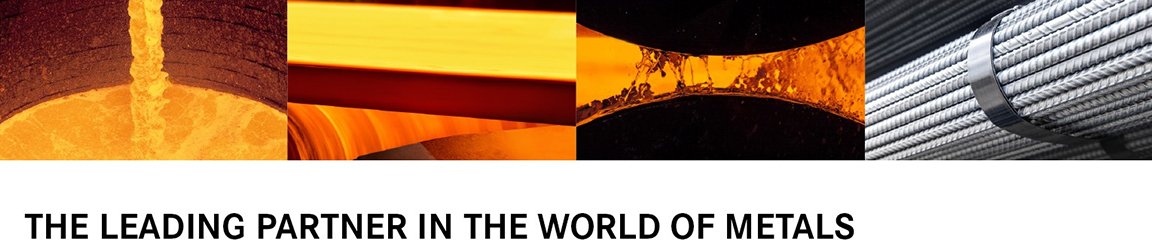
SMS group's advanced technology upgrade ensures unparalleled rolling stability and high-quality strip production at Çolakoğlu Metalurji
- Stabilized rolling process and enhanced quality thanks to integrated strip guidance solution
- New control system provides correction signals for each mill stand
- Lower maintenance costs through process optimization
SMS group has successfully implemented the technological upgrade of the hot strip mill complex it originally supplied to Çolakoğlu Metalurji for its site in Kocaeli, Türkiye. The upgrade has brought significant benefits in terms of rolling stability and high-quality strip production, especially with regard to strip flatness and coil shape, with less maintenance required in the finishing mill.
SMS group’s scope of supply included the integrated strip steering package, consisting of mechanical side guides, roll alignment control strategies, and camera-based measuring systems for real-time feedback on the strip position. Six X-Pact® Sense hotCAMs designed for harsh environmental conditions, such as high strip temperature, mist, steam, dust, and vibration, were installed on top of the finishing mill stands (F2-F7) to provide a view of the strip on the interstand looper. X-Pact® Centerline Control uses a closed-loop algorithm to calculate any deviation from the strip centerline and provides a levelling correction signal for the mill stands. Various control methods are used for the different rolling sequences (head, filet, and tail end). A smooth transition between the control actions in each individual phase is ensured and the operators are assisted by corresponding visual displays.
As a result, unplanned roll changes are reduced and rolling stability is improved throughout the hot strip mill. Fewer tail-end problems when rolling thin strip, improved strip surface and strip geometry, especially in terms of the strip wedge, ensure high-quality production. In addition, the low number of rework coils and spare parts significantly reduce maintenance work at Çolakoğlu Metalurji, boosting the productivity levels of the hot strip mill.
“SMS group’s extensive expertise in commissioning as well as its newly developed technological concept for integrated strip guidance were decisive factors in choosing SMS group as our partner. The installation of guides and centerline control has been a game changer for our mill. We see improvements in rolling stability, coil shape, and strip flatness, and are now able to reduce our maintenance effort,” said Özgür Özsoy, Plant Director at Çolakoğlu Metalurji, following the successful modernization.
As a partner for integrated solutions, SMS group takes on the challenge of paving the way for autonomous rolling and enhancing the performance of its customers’ plants throughout their entire lifecycle. Intensive preparation and close cooperation between both parties enabled the upgrade to be carried out during the regular weekly and annual shutdowns, without the need for additional downtimes.
The perfect match between mechanical equipment and automation systems was in itself key to the quick ramp-up of the compact hot strip mill at Çolakoğlu Metalurji, which SMS group commissioned in 2011. The rolling mill’s main equipment included the four-high reversing roughing stand with edger, a mandrel-less coilbox, a seven-stand finishing mill, a laminar strip cooling section, two fully hydraulic coilers, and a pallet conveyor system. The plant is designed for a capacity of three million tons per year, producing hot strip from 800 to 1,650 millimeters wide and 1.2 to 25.4 millimeters thick. Strip production down to 1.1 millimeter is possible. With the new technology from SMS group, Çolakoğlu Metalurji is strengthening its market position in the production of thin hot strip.