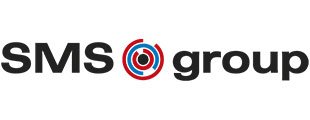
+27 (0) 11 480-1800
204 Rivonia Road, Morningside, Sandton, 2196
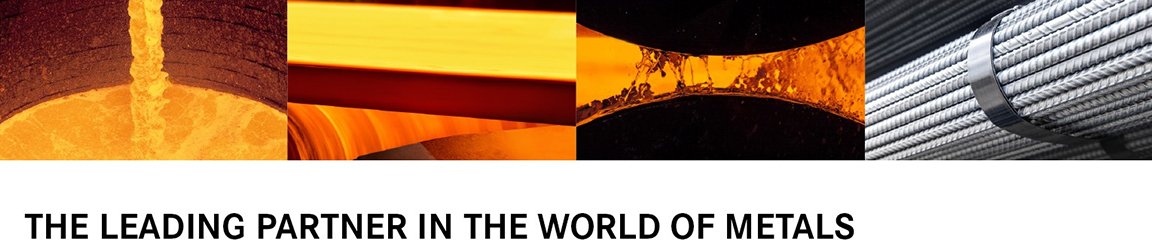
Sophisticated modernization concept for the production of high-quality structural steel, boiler, tube and heavy-plate grades
ArcelorMittal Asturias (Avilés) has contracted SMS group for tailor-made conversion of slab caster No. 2
ArcelorMittal Asturias, Avilés, Spain, has contracted SMS group www.sms-group.com for a comprehensive conversion of the company’s two-strand slab caster No. 2. With this modernization, ArcelorMittal Asturias responds to the increasingly higher quality demands in the growing market for special steels such as grades for tube and heavy-plate production.
The two-strand slab caster No. 2 was originally supplied by SMS group in 1987. Since then it has produced approximately 1.9 million tons per year of steel slabs with thicknesses of 235 and 280 millimeters and a maximum width of 1,600 millimeters.
After the modernization, the continuous caster will be able to produce up to 2.7 million tons of steel slabs per year with thicknesses of 235, 300 and 365 millimeters and widths from 800 to 2,200 millimeters.
The greatest challenge of this project was the customer’s request to expand the slab width from 1,600 to 2,200 millimeters without extensive rebuilding of the foundations and the resulting prolongation of the building phase, which would have made the overall project less efficient. The special design of the segment carrying frames to be installed by SMS group will allow the existing foundations and anchor bolts of continuous caster No. 2 to be maintained without any modifications.
The tailor-made modernization concept, based on the innovative design developed by SMS group, convinced ArcelorMittal Asturias also in terms of profitability.
The continuous caster will be completely rebuilt from the mold down to the exit section, maintaining the curved mold design. The curved mold provides significant advantages especially when casting slabs with a thickness of more than 320 millimeters from steel grades particularly susceptible to cracking.
Although the maximum slab thickness will be extended to 365 millimeters, the radius of 10.5 meters will be retained, while increasing the metallurgical length from 33.2 to 36.7 meters. The continuous caster will be designed for a maximum casting speed of 1.6 meters per minute; the spray cooling concept will take into account a future increase in casting speed.
The caster will be equipped with SMS group’s remote-adjustable mold, which allows width adjustment and automatic adaptation of the mold taper during production without having to reduce the casting speed. The system takes into account the steel grade and the current casting speed. The mechanical oscillation system will be replaced by a hydraulically actuated oscillation system by means of which both the stroke length and the frequency can be changed during the casting process.
The straightening segments and the segments in the horizontal section will be equipped with an online gap control system operating with position-controlled clamping cylinders. The new slab caster No. 2 will work with various X-Pact® Level 2 process models for quality control. The Mold Monitoring System will monitor the temperature distribution in the strand shell. In this way, stickers can be detected and the risk of break-outs can be eliminated early in the process.
Furthermore, SMS group will implement a new secondary cooling concept with a width-dependent air-mist cooling system and DSC® (Dynamic Solidification Control).
DSC® calculates the solidification process of the strand and controls the various secondary cooling zones based on selectable parameters such as casting speed maximization or – in the case of steel grades particularly susceptible to cracking – optimization of the straightening temperature as a function of characteristic values of the processed material.
The metallurgical process model Dynamic Soft Reduction® allows a targeted compression of the slab in the final solidification zone to improve the internal microstructure. The data specifying the most suitable location and amount of compression are provided by the DSC®.
The cooling circuits for the mold, the casting machine and the spray cooling system will be completely renewed; the hydraulic equipment will be adapted and enhanced.
For the workshop of ArcelorMittal Asturias, SMS group will supply its new HD LASr plant assistant. HD LASr is already in use in the workshop of continuous caster No. 1. Already when ordering the HD LASr assistant for that caster, ArcelorMittal Asturias had been so convinced of the new system that no rulers for conventional measurement of the mold and segments had been included in the contract.
Thanks to the high quality of the laser measurement, the exact and reliable recording and the meaningful evaluation of the measured objects, HD LASr is far superior to the systems used up to now. Considering the high sensitivity to cracking of the steel grades to be cast and the greater slab thickness, more exact alignment of the strand guide system may significantly contribute to preventing crack formation in the slab.
Continuous caster No. 1 was successfully commissioned in late 2016, after modernization by SMS group, which involved the conversion to a vertical bending plant. Only five weeks after commissioning, the monthly production rate had already reached pre-conversion figures. The customer rates the quality of the rolled coils as very good.
The integrated steel plant of ArcelorMittal Avilés produces high-quality steel grades for the automotive and tinplate industries as well as for heavy plate production.
(93 lines of max. 65 characters per line)
Slab caster from SMS group for high-quality steel grades.
Reliable measurement of continuous caster segments and molds using the HD LASr plant assistant system from SMS group.