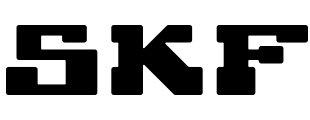
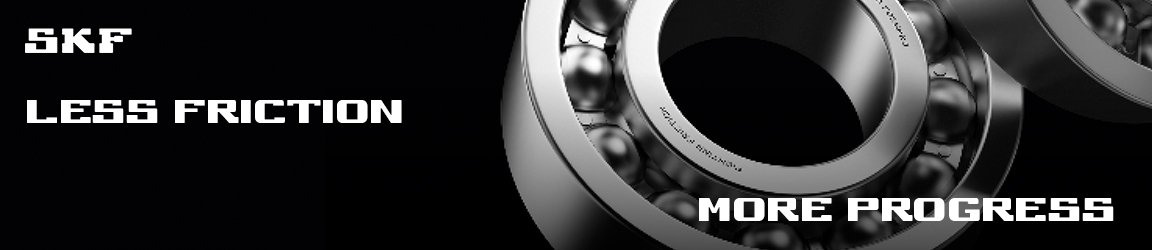
System enhances bearing lifespan, reducing costs
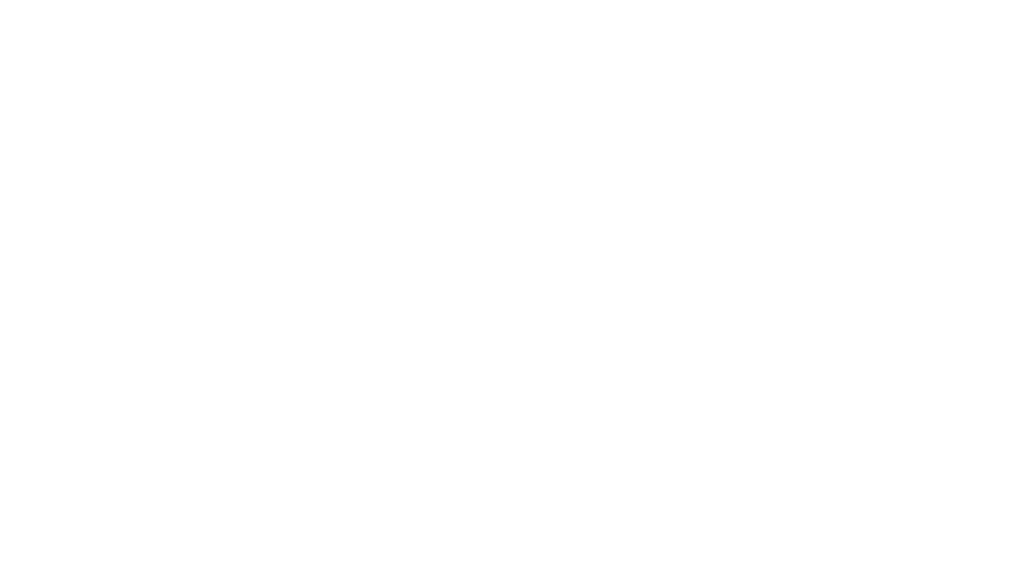
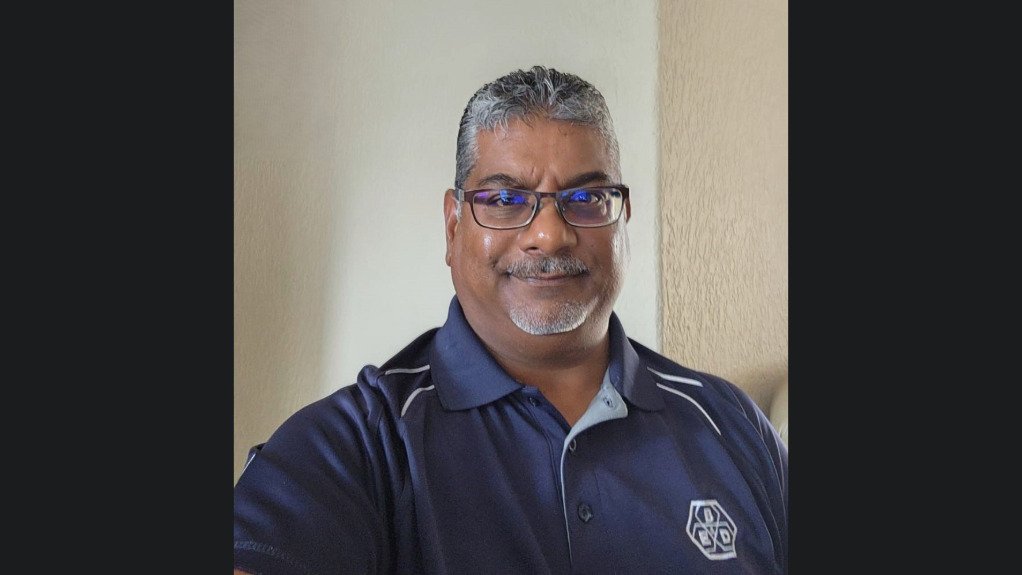
LINGESH NAIDOO B.E.D. recognises the importance of bearing remanufacturing, particularly for large size bearings, which may not be readily available on the market
Bearings are vital components in machinery, as their performance directly impacts on productivity and equipment lifespan, among other key performance metrics, and fastener specialists Bolt and Engineering Distributors Group (B.E.D.) provides a comprehensive approach to managing the life-cycle of these components.
As such, the company is not just focused on selling bearings, but is committed to monitoring and optimising operational performance throughout their lifespan.
Condition monitoring – real-time insights into a bearing’s performance and health – is essential to extend a bearing’s lifespan, B.E.D. industrial bearing specialist Lingesh Naidoo elaborates.
He highlights B.E.D. supplier Swedish bearing and seal manufacturer SKF’s condition monitoring system Axios, which uses AI-driven analytics to process data from sensors monitoring key parameters.
The system will flag deviations from normal operating conditions and provide actionable insights, making this real-time data critical for industrial plants, as it enables the prioritising of bearing maintenance based on wear.
“SKF Axios – among other vibration data acquisition devices in our portfolio – helps companies reduce costs by enabling preventative maintenance,” explains Naidoo.
With the implementation of this system, condition monitoring can “significantly” enhance the safety of workers, as it proactively identifies potential issues with machinery before any failures or accidents can occur.
Naidoo cites companies now being able to detect abnormal vibrations or temperatures in equipment, and alerting their maintenance teams to problems that require their attention.
The system can, therefore, prevent downtime and extend the lifespan of associated machinery components.
A key benefit of this solution is that many components, including bearings, can be remanufactured rather than replaced entirely once they start showing signs of wear. This type of condition monitoring enables companies to catch signs of wear earlier.
Remanufacturing Potential
The remanufacturing of bearings can restore them to their original specifications, at a lower cost than buying new ones, further contributing to cost-savings.
This presents a compelling alternative to the traditional practice of replacing failing components because it not only reduces costs but also reduces environmental impact in terms of waste production and energy consumption, making remanufacturing a sustainable choice for industries that are heavily reliant on bearings.
Remanufacturing can use as little as 10% of the energy required to produce a new bearing, significantly reducing carbon emissions.
This process also prevents the disposal of components, which conserves valuable resources, such as the various metals and/or polymers used in bearing manufacture, adds Naidoo.
“At B.E.D. we recognise the importance of bearing remanufacturing, particularly for large size bearings, which may not be readily available on the market or in cases where bearings have not yet reached the end of their service life,” says Naidoo.
B.E.D. has, for instance, implemented remanufactured bearings in a customer’s bottling plant. In this instance, the plant’s milling-rolls’ work surface often wear before the bearings reach the end of their service life.
Rather than replacing the entire assembly, B.E.D. removed the bearings from the milling rolls and then sent them to SKF for inspection and remanufacturing.
“As more and more customers consider environmental footprint when they choose suppliers, SKF Remanufacturing Services comes with a technical inspection report of the product, documented CO2 emission reduction [data] and a warranty that is virtually the same as for a new bearing.”
Naidoo adds that SKF has also developed an Avoided Emission Calculator, an application that can easily show the amount of CO2 emissions that are averted by purchasing remanufactured components instead of new ones.
Opting for remanufacturing services reduces CO2 emissions by an average of 90%, when customers select SKF Remanufacturing Services.
“They receive documentation from SKF that shows them how they are contributing to the circular economy, which, in combination with the real-time monitoring ability of the Axios system, ensures that companies can significantly lower their maintenance and replacement costs.”
He adds that SKF also has RecondOil, which makes it possible to reuse oil, and can be retrofitted to most systems.
Naidoo concludes that this holistic approach not only enhances overall asset reliability, but also fosters a more sustainable operational model in industries across South Africa.