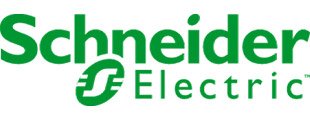
+27 (0)11 0461900
Private Bag X139 Halfway House 1685
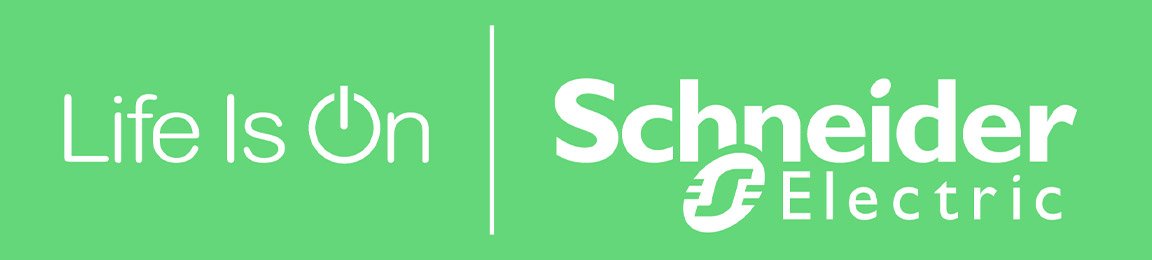
The digital mining frontier - future developments for process automation in mining
By Hennie Colyn, MMM - Strategic Account Executive at Schneider Electric
The digital process automation market is expected to reach a staggering 24.2 Billion by 2028, with a Compound Annual Growth Rate (CAGR) of almost 14%. This is according to The Business Research Company’s Digital Process Automation Global Market Report 2024 which attributes the growth to various factors such as legacy system modernisation, cost reduction initiatives, regulatory compliance requirements, the imperative to improve customer experience, and the pursuit of business agility and adaptability.
It is also the above (cited factors) that is making a strong case for process automation in the mining, minerals and metals industry. The promise of improved efficiency, elevated safety standards, increased productivity, and informed decision-making processes is undoubtedly compelling.
The wheels that drive process automation
To make the most of process automation, mining operators will have to invest in systems that feature advanced automation technologies such as Artificial Intelligence (AI) and Machine Learning (ML), robotics and other autonomous systems whilst also establishing the seamless integration of IT and OT.
For example, by integrating process automation with AI and ML, mines will be able to predict equipment failures and prevent costly downtime. AI tools can analyse current machine performance against baseline data and identify subtle reductions in efficiency that may signal the need for maintenance. This will mitigate potential breakdowns and optimise operational continuity.
Looking at safety, robots and autonomous systems can perform dangerous and repetitive tasks in mining operations, such as drilling, blasting, and haulage. These systems can autonomously navigate hazardous environments by utilising cameras and sensors to identify minerals, enhancing safety and operational efficiency.
Effective process automation relies heavily on the integration of IT and OT systems which is enabled by digitising physical (OT) equipment by fitting it with advanced IoT sensors as well as implementing machine-to-machine (M2M) communication.
This digitised physical equipment offers real-time monitoring, analysis, and autonomous operations, ultimately enhancing uptime and efficiency.
Considering the above, process automation offers the following important benefits to mines.
- Data management and analytics - utilising the power of data to drive informed decision-making and optimise operational efficiency.
- Remote monitoring and control - enabling real-time monitoring and control of mining operations from anywhere, enhancing safety and efficiency.
- Smart sensors - leveraging IoT sensors to digitise physical equipment, enabling predictive maintenance and enhancing operational performance.
- Connectivity solutions - establishing robust communication networks to facilitate seamless integration of IT and OT systems
- Autonomous systems - robotics and autonomous technologies automate tasks, improve safety, and increase productivity.
Other considerations and benefits
Mines will have to prepare their workforce for the transition to process automation by proactively implementing programmes focusing on key areas such safety, risk management and operational discipline. These all with require leadership commitment to ensure a smooth and safe transition in automated mining environments.
Furthermore, process automation presents an opportunity for mining companies to reduce their environmental impact and operate more sustainably. By, for example, using process automation to implement reforestation (by removing mining infrastructure and waste), companies can minimise their footprint on the land and ensure the responsible use of natural resources.