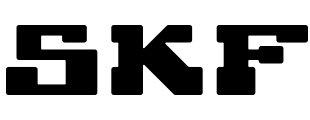
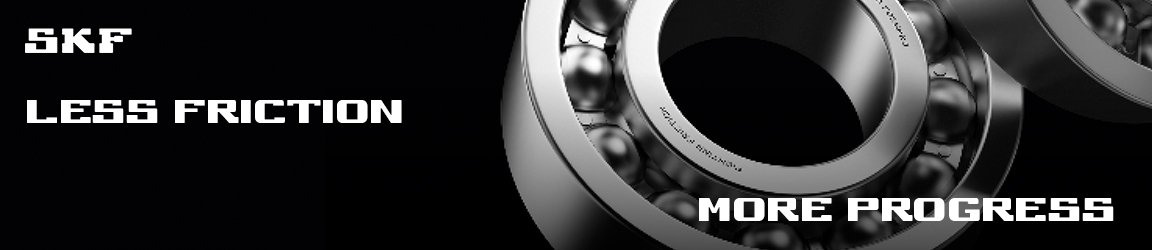
The gold standard for planter bushings
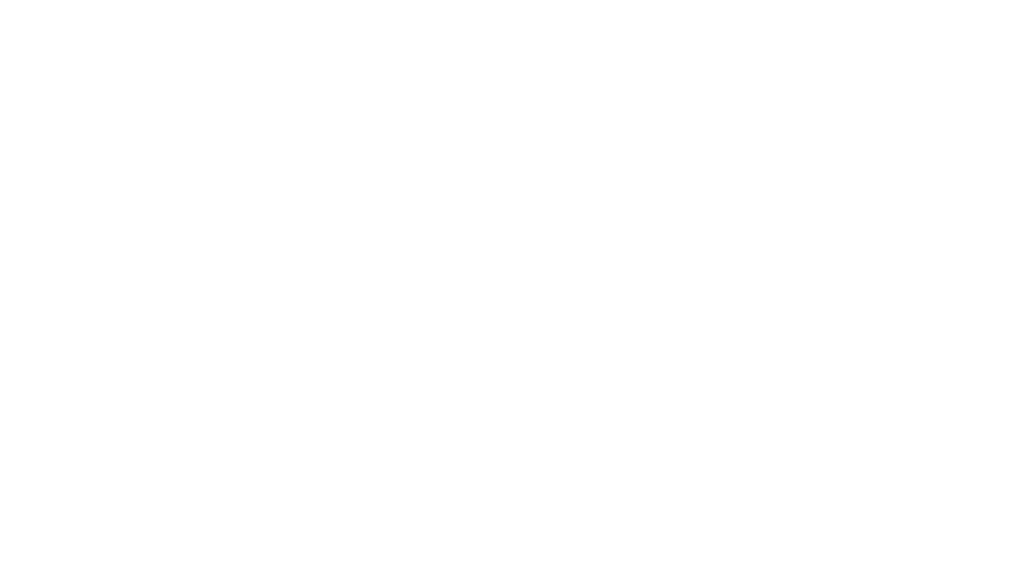
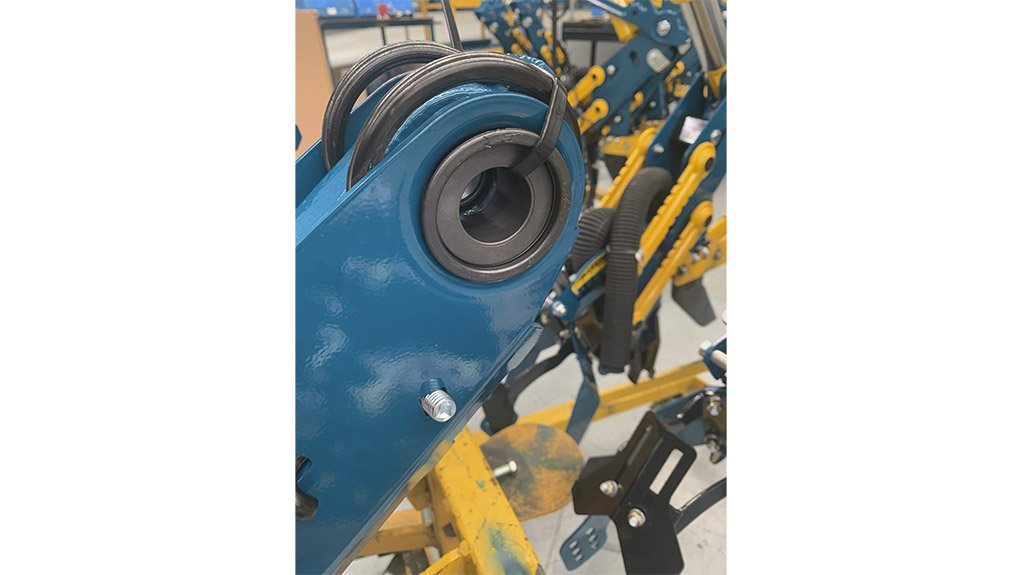
Vesconite planter bushings assist in ensuring continuous and accurate seed placement, in the harshest of conditions, all in the pursuit of better yields and higher efficiency
Anyone involved in agriculture will tell you that maintenance is crucial to your equipment life and performance and will quickly come back to bite you if it is neglected. A planting row unit has many moving parts, all of which need to work in harmony to ensure continuous and accurate seed placement, in the harshest of conditions, all in the pursuit of better yields and higher efficiency.
“Equalizer aims to use only the best quality and fit-for-purpose components on the market, to ensure that we manufacture world-class machines, which meet any farmers highest standards,” states the head of design at Equalizer AG, a company that specialises in the design, manufacture and global distribution of planting and seeding equipment for grain production.
“To ensure all parts keep moving as intended for as long as possible, we spec SKF hubs and bearings on all our machines. We also use Vesconite bushes on almost all of our oscillating pivot points, as many years of in-field feedback has led us to believe it is the best self-lubricating engineering polymer on the market for our applications.”
Before Equalizer made the switch to low-friction, wear-resistant, no-swell, self-lubricating Vesconite bearings on its row units, it had been utilising nylon bushings on the pivot points. These bushings would typically be used on the parallel arms and closing wheel pivots.
All of these oscillating points are under high loads, as hydraulic or spring force are used to ensure the row unit has adequate downforce to plant at a consistent depth and create proper seed-to-soil contact for the best germination and even emergence. Add to that rough undulating terrain or rock filled fields - these bushings work extremely hard!
With the ever increasing push to extend part life, Equalizer identified that an alternative to the nylon bushings needed to be sought. To quote: “The main reason for the material change was to increase the life of the bushes and therefore increase the time between maintenance intervals. This keeps the equipment running as intended for longer especially on larger farm setups due to the fact that mid-season maintenance is not feasible with the narrow planting windows. The other advantage of increased bush life is a reduction in maintenance downtime, allowing clients to go through a number of seasons before needing to do anything more major than the standard greasing, which also has a significant cost saving when considering the labour component.”
“Under higher loading cases, the Vesconite resists deformation more than our previous nylon. This keeps the bushes in shape, which prevents the joints getting ‘floppy’.”
“I can’t give exact values on the difference in service life between the two materials as there are many factors that would need to be considered, but what I can say is our clients have been more than happy with our change over to Vesconite, which has solidified our feeling that we have made the right ‘fit for purpose’ material choice.”