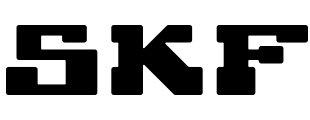
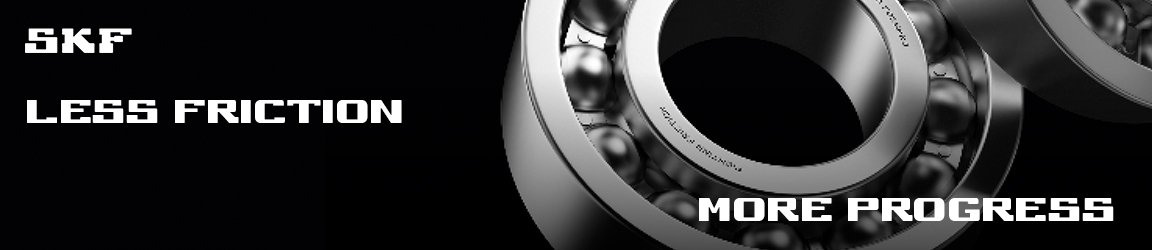
The hygienic design of SKF Food Line ball bearing units, sets the industry standard in safe food production
SKF’s innovative Food Line ball bearing units feature a cutting-edge hygienic design that delivers improved reliability, reduced maintenance costs and increased sustainability for the global food and beverage industry.
Known as the Blue Range, these bearings offer a solution to companies who are striving towards perfecting their proactive approach to food safety, which extends to a hygienic-design mentality to bearing unit components for food-processing equipment.
A prominent rise in food recalls by the Food & Drug Administration (FDA) is urging companies to proactively address their food safety practices. While practices such as purchasing hygienically designed ‘food grade’ machines are important, focusing on contamination risks at the component level is just as crucial. Traditional relubrication, frequent wash-downs with abrasive cleaning agents and dry cleaning of bearings can cause corrosion and create hidden means by which contaminants such as airborne droplets, wastewater or contaminated grease thrive.
SKF’s Blue Range has been specially designed to eliminate these food-safety threats and is fully compliant with food safety regulations. Owing to their ingenious hygienic design, these units reduce the risk of bacteria build-up in hard-to-clean areas and minimise the spread of bacteria during cleaning.
With an innovative sealing system, high performing bearing grease, and complete seal-ability of the units where it’s needed, these Food Line ball bearings deliver outstanding performance benefits. Subsequently OEMs are able to innovate the performance and hygienic design of their food processing equipment through bearing units that last longer, are relubrication-free and highly cleanable. Furthermore, as the bearings units do not require relubrication, there is no need for equipment stoppages to allow for lubrication activities. Less time is also required for cleaning excess bearing grease, resulting in increased production uptime and maximised production opportunities. In addition to the removal of relubrication costs and reducing bearing replacement frequency, re-greasing material and labour costs are eliminated.
The Blue Range also reduces environmental waste; with less hot water needed for cleaning, grease-free waste water and components that can be 100% recycled and energy recovered, companies can foster a preventive- versus disposal-oriented environmental culture.