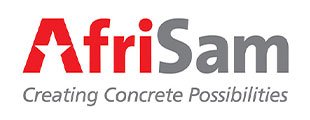
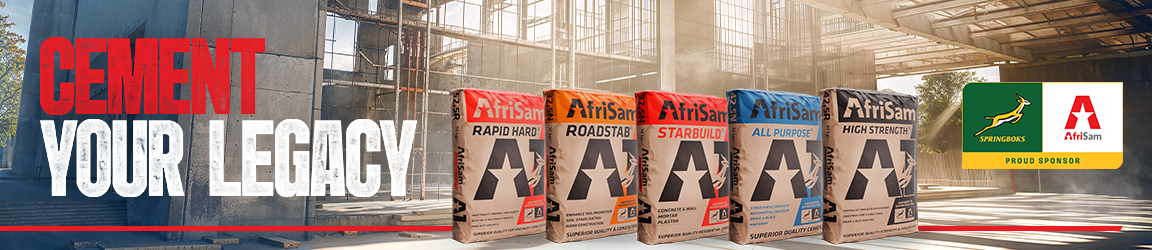
Updating Technology With Planned Maintenance – AfriSam
To stay at the cutting edge of cement production technology, construction materials leader AfriSam ensures that its maintenance programme is well planned with future production targets and energy efficiency goals in mind.
According to Hannes Meyer, executive - cementitious at AfriSam, the company’s maintenance standards are codified as part of its corporate ‘AfriSam Way’ programme, and comprise three areas: preventative maintenance, corrective maintenance and capitalised maintenance.
“Capitalised maintenance is vital to ensuring that you stay abreast of current technology and upgrade regularly in a way that improves the performance of equipment continuously,” says Meyer.
At its Ulco plant in the Northern Cape, for instance, the capitalised maintenance plan is allowing production to be raised from its original production capacity of 3,500 tonnes per day of clinker to a targeted output of 4,750 tonnes per day in the near future. The plant – built in 1984 – already runs comfortably at over 4,000 tonnes per day.
In addition to the production increases, the plant upgrades conducted as part of the maintenance schedule are also driven by the need to reduce energy costs and environmentally negative nitrous oxide (NOx) emissions. He highlights that energy has become one of the most costly components of cement production – comprising electricity costs and thermal energy mainly in the form of coal.
“Installing a high efficiency separator gave us an immediate reduction in energy consumption, while an upgraded clinker cooler also facilitated higher output at the same time as reducing energy costs,” he says. “The gearbox in the raw mill was also replaced with a view to reaching our 4,750 tonne target. We replaced the electrostatic filter with a bag filter, not only to comply with more stringent emission standards but also to cope with the added volumes of air through the kiln.”
Another imminent upgrade will be to raise the capacity of the pre-calciner, which will in turn increase the output of the kiln while reducing the energy it consumes.
“The new pre-calciner will also have a positive impact on our nitrous oxide (NOx) emissions, by ‘splitting’ the energy input between the firing end of the kiln and the pre‑calciner,” he says. “This reduces the temperatures or the energy load in the kiln, which cuts down NOx formation.”
In a further innovation, AfriSam is helping to address the environmental issue of old vehicle tyres by using them as an alternative fuel at its Dudfield cement plant; the project is also designed to be labour-intensive, creating local jobs as part of the company’s positive social impact in its areas of operation.