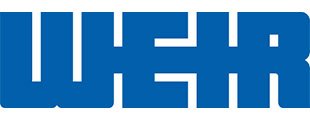
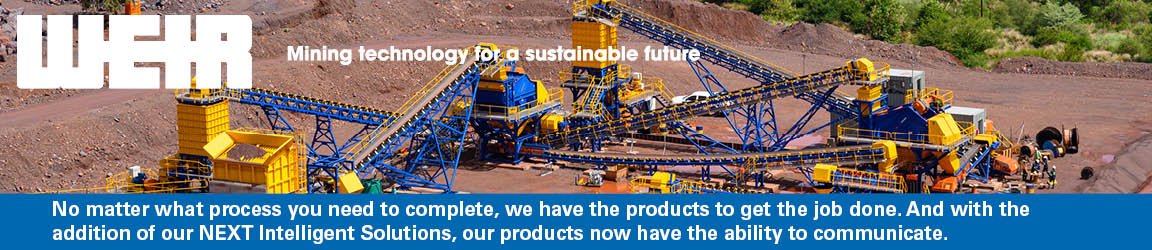
Warman® WRT® technology: the definitive wear life and efficiency upgrade for Warman® AH® slurry pumps
Retrofittable Warman® WRT® impeller and throatbush improve wear life by up to 50% and utilise hydraulically efficient four-vane design to reduce operating costs.
Warman® Wear Reduction Technology (WRT®) impellers and throatbushes add a new tool to the toolbox of miners struggling to cope with mounting operating expenses. A simple, inexpensive upgrade compatible with all Warman® AH®, M and L series slurry pumps, the streamlined parts offer total ownership costs reductions, improving efficiency, reliability and wear life.
Warman® WRT® technology is the culmination of decades of research into the wear patterns and hydraulic performance of the Warman® AH® pump’s impeller and throatbush. Together with a unique vanelet on the back shroud, replacing the five-vane impeller with a modern four-vaned design improves fluid guidance through the pump and represents a step change in impeller design.
“What I love about our Wear Reduction Technology is how it improves on everything our customers expect from the iconic Warman AH pump range. It uses best-practice design techniques leveraged by the world’s top slurry pump engineers to maximise hydraulic efficiency and reduce operating costs without increasing the pump’s complexity. Its advanced wear materials improve reliability and reduce time spent maintaining the pump. It simply makes the world’s most famous slurry pumps even better,” says Marcus Lane, Global Product Manager, Centrifugal Pumps.
Not only do the hydraulic refinements lower the pump’s lifetime consumption, but they reduce the Net Positive Suction Head (NPSHr) requirements of the pump, making the upgrade an ideal way to compensate for process or feed changes which have left a Warman® AH® pump overtaxed.
This technology has already proven its worth in the field, such as at Blackham Resources’ Matilda Gold Mine in Western Australia, where the installation of Warman® WRT® technology more than doubled impeller wear life in a demanding application involving abrasive, highly viscous slurry. The new impeller and throatbush reduced total ownership costs for the pump by AU$27,000 per year due to the parts’ higher efficiency and longer wear life.
“I’m so proud of the way Warman constantly innovates for existing customers. Retrofitting WRT technology into an installed pump couldn’t be easier – next time you need to replace your impeller and throatbush, simply install the Warman WRT parts instead. Nothing changes in your setup, fitment, or general maintenance practices. The pump doesn’t need a speed change and the entire process uses existing maintenance tools. Really, the only thing that changes is that your pump is now a lot better at its job,” Marcus concludes.
All the technical data related to the impeller retrofit kit, as well as a full set of performance curves, are available from your local Weir Minerals Service Centre or support office.
Warman® WRT® impellers and throatbushes are available worldwide.
Marcus Lane is available for comment.
Weir Minerals Africa