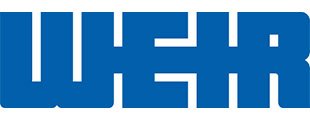
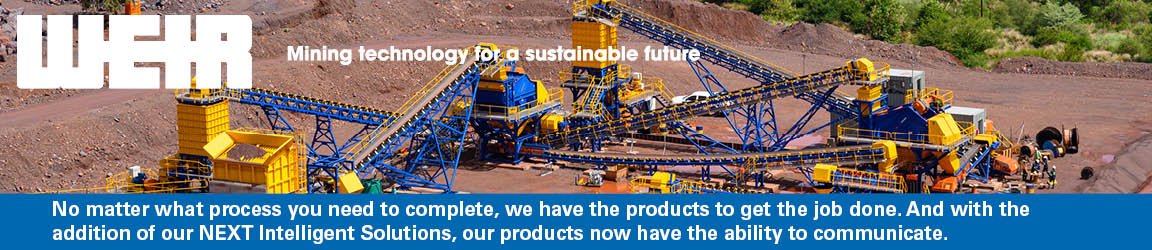
Weir wins record £100m order for Australian magnetite iron ore project
The Weir Group PLC (Weir), one of the world’s premium providers of highly engineered mining equipment and services, has been awarded a £100m order to provide industry-leading energy saving solutions to the Iron Bridge Magnetite Project, a joint venture between Fortescue Metals Group Ltd subsidiary FMG Magnetite Pty Ltd and Formosa Steel IB Pty Ltd. The Project is located 145km south of Port Hedland in the Pilbara region of Western Australia.
The order, which includes a range of Weir crushing and pump equipment including Enduron® High Pressure Grinding Rolls and GEHO® pumps, will reduce energy consumption and wet tailings waste by more than 30% compared to traditional mining technologies.
The Iron Bridge project is a US$2.6bn investment in premium magnetite iron ore reserves with annual production, when the mine is fully operational, of 22 million wet metric tonnes per annum. Delivery of the first ore is expected in 2022.
Responding to the award, Weir Group Chief Executive Officer, Jon Stanton said:
“We are delighted to have secured this landmark contract, which is Weir’s largest-ever individual mining order. Fortescue challenged us to help create one of the most energy and cost-efficient magnetite ore processing facilities in the world. Our engineers have worked relentlessly to design a solution that is truly innovative – delivering significant energy, water and cost savings. This is a great example of working in close partnership with an ambitious customer who shares our passion for using innovative engineering to make mining more productive and sustainable.”
Ricardo Garib, President of the Weir Minerals division, commented:
“Our team are really enjoying working with Fortescue. Our engineers relish a challenge and it has been great to work on a project that demonstrates the substantial cost and environmental savings that our range of solutions can offer. As more mines look to increase productivity, we look forward to even more opportunities to leverage our combination of passionate people, innovative solutions and comprehensive global service capability.”
Weir’s Enduron® HPGRs are increasingly replacing conventional mills in comminution (crushing, screening and grinding) circuits because of their substantially lower energy consumption and potential for significant total cost of ownership reduction. Not only do they require as much as 40% less energy than traditional alternatives, but their wearable components last much longer and the maintenance time required to replace worn out parts is significantly lower.
Stuart Hayton, Managing Director of Weir Minerals Netherlands, where the Enduron® HPGRs and GEHO® pumps are designed and manufactured said:
“We are seeing growing demand for these technologies because of their significant benefits compared to older products. Comminution is one of the most energy intensive processes in the world and the ability to deliver substantial reductions in costs, energy and water use not only supports miners’ profitability but also the sustainability of our industry.”
Weir Minerals Africa