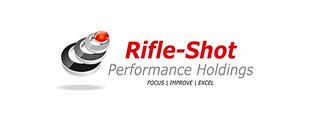
+27 11 463 5073
Suite 109 Bryan Park Offices 46 Grosvenor Rd Bryanston 2153
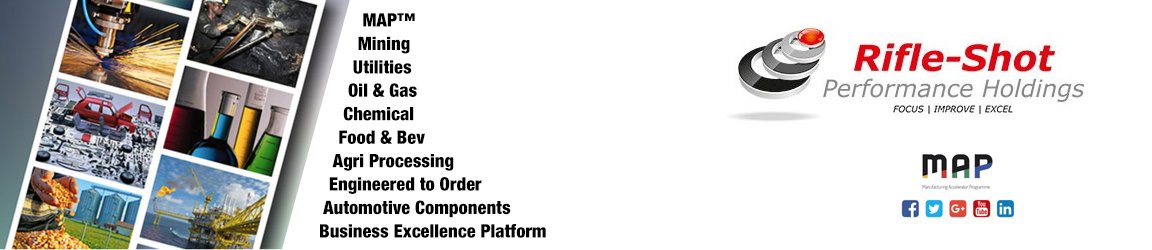
What’s reliable data worth
By Caroline Carter
The Challenge
What is the real VALUE of Quality Data?
Whether we’re talking about a refinery or a gold mine, losses resulting from yield losses, theft and/or the processing of raw materials amount to millions of dollars per year, whether it is in mining or the oil value chain.
London-based Ernst & Young (EY) audit and consulting company estimates that around $133 billion worth of crude oil and refined products are stolen or adulterated every year.
Barberton Mines manager, Casper Strydom told Engineering News, “We estimate that around 10kg to 15kg of gold is stolen monthly – it could be more”. That equates to roughly R9.43 million, and R18.91 to the dollar.
While it seems there’s not much to be done about that until finding the rough, inaccurate estimation of the amount after the fact, this is not the case.
When it comes to material and composition tracking, accurate data from multiple sources allows one to identify very small percentage variances quickly. What’s the difference in monetary terms? A variance of 1% in a South African Energy company (Fuel, Chemicals, Energy) which equates to around $60m per year.
Managing loss-reduction programmes is extremely time-consuming when managed manually, and usually reporting on losses incurred during the processing alone can take up to a month to complete, leaving no room for loss detection, let alone error correction.
The Solution
Estimated savings from an oil loss-reduction programme for a refinery or large fuels consumer such as a power station are typically between 2 to10m$/year for an average sized oil refinery, and on a gold or platinum loss-reduction programme, between 2 and 9M$/year. However, for these savings to be attained, reconciled data has to be accurate, and received in near real-time.
When looking at component mass balancing, there are several factors we have to take into account:
Analysis frequency – hourly, daily, etc.
Component Balance Flag - Choose where the Component Balance is applied, or where a simple material balance is required.
Reconciliation of all components - Provide consistent set of reconciled masses and components, and provide reconciled data for unmeasured quantities.
The complexity of analysis in Mass Balancing, Volume Balancing, Energy Balancing, Component Balancing, Material Tracking and Quality Tracking can all be managed in one place. Allowing you the ability to minimize losses almost immediately, saving millions of dollars, whilst complying with ever more stringent regulations and enabling enormous top and bottom-line savings.
Register here:https://www.rsph.co.za/upcoming-events/
Rifle-Shot Performance Holdings