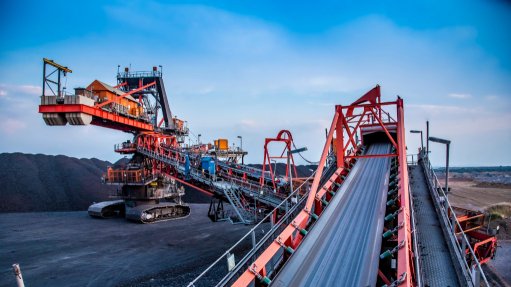
Conveyor belts channel ore into a Weba Chute
Johannesburg-based Weba Chute Systems asserts that its customised chute designs optimise material flow and reduce wear, ensuring minimal downtime in abrasive ore handling applications.
Weba Chute Systems technical manager Dewald Tintinger highlights that the company systematically assesses customers’ requirements, taking into account factors such as the area around transfer points, material characteristics, throughput tonnages and speed of travel, to inform its chute design.
The design is built on scientific calculations using the anticipated trajectories, impacts and pressures on the structure. The main conceptual options are Weba’s Cascade chute with dead boxes, the Weba Superflow chute with liners or a combination of both.
“A key element of our popular Cascade chute is the use of dead boxes and lips on the inside of the structure, which traps material and allows other material to flow over it,” says Tintinger. “This ensures that up to 70% of the wear surface is protected by stationery material, which substantially reduces wear and maintenance costs while extending service intervals.”
As material enters the chute and flows through, it lands mainly on other material which absorbs the impact more effectively, which helps protect the underlying wear plates and structure from undue damage. This also reduces dust creation, he notes, which is an ongoing health and safety concern on mines.
“Controlling material flow through the right chute design also protects costly equipment like conveyor belts,” adds Tintinger, citing an example where Weba Chute Systems installed a Cascade chute at a Southern African copper mine to better control the flow of material onto conveyor belts, helping to save belt costs while boosting productivity through improved uptime.