Active seal solution to mitigate corrosion
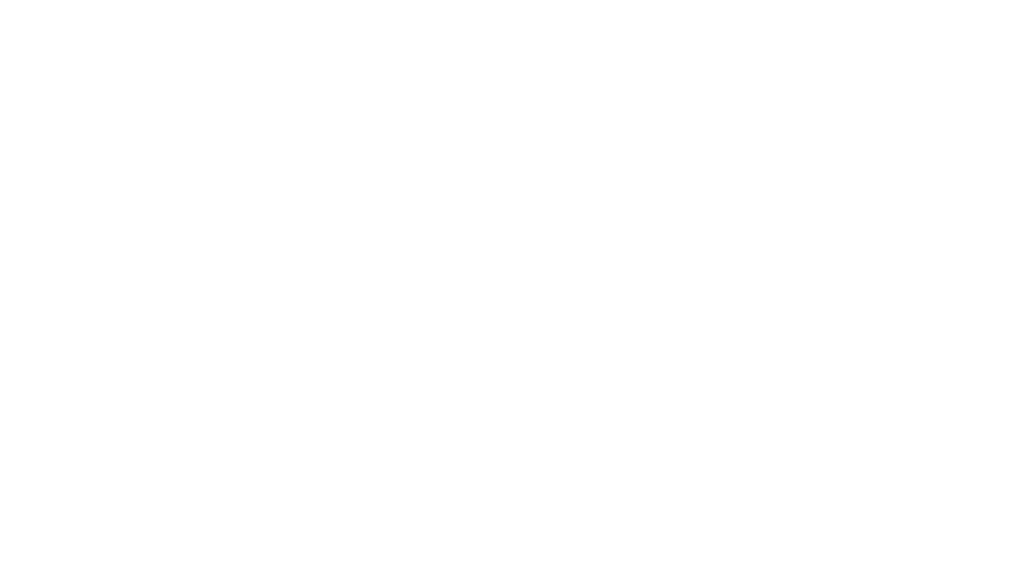
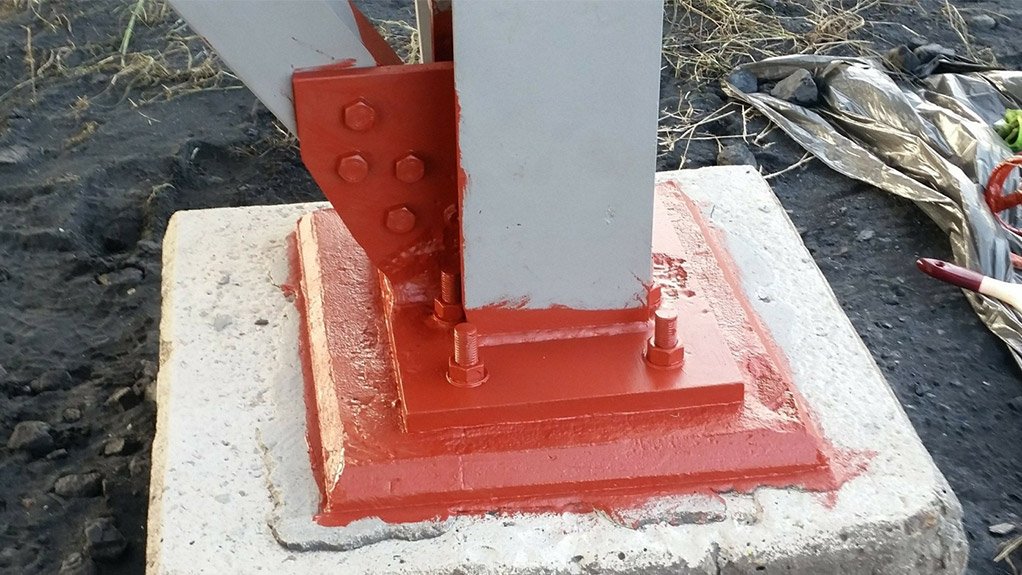
NEW PRODUCT HRCSA coating technology has been used in the US to prevent crevice corrosion
Companies and industries affected by corrosion should consider Afrisun’s High Ratio Calcium Sulfonate Alkyd (HRCSA) coating to mitigate the threat of corrosion at production plants in the metals and industrial sectors, says local corrosion solution provider Afrisun Coating Enterprises CEO Quentin Erasmus.
HRCSA is an “active sealant” that is compatible with concrete and a perfect duplex/overcoat for hot dip galvanising and forms a homogenous seal over concrete and metal. Passive barrier coatings are simply a film applied over the substrate separating the atmosphere from the substrate but when damaged, under-creep and corrosion will occur. However, the HRCSA coating reacts with the zinc carbonate layer on the surface of the zinc, pushing the pH > 10.1.
By doing this it mitigates corrosion, making it an “active seal”. Further, the calcite in the coating is the most common form of calcium carbonate, which is also insoluble in water and compatible with concrete. The calcite makes the HRCSA hydrophobic thereby eliminating moisture (electrolyte).
The HRCSA seal is not conductive, thus eliminating the formation of a galvanic cell that would corrode steel. The active seal also prevents any abrasive dust from entering a jointed area.
The HRCSA coating technology has been used in the US to prevent crevice corrosion of vehicles and protect most of the US Department of Transport’s metal bridges against corrosion, according to Afrisun.
HRCSA is also suitable for use in coal handling facilities such as structural supports, conveyer belt support base plates that are fixed to foundations or gusset plates that are bolted together to keep segments of structures together.
The process of crevice corrosion starts with oxygen depletion in a near stagnant moisture in crevices, which lowers the pH in the crevice causing an acidic environment which exacerbates corrosion. Extended periods of moisture (condensate) and conductive runoff onto foundation assemblies leads to substation foundations being threatened by crevice corrosion,” explains Erasmus.
Currently, most companies use conventional “passive barrier” coatings to mitigate general corrosion; these are simply not working effectively because these coatings become hardened on the substrate and crack, with no seal having been formed, allowing the ingress of moisture and oxygen into the crevice leading to corrosion, he explains.
In instances where an abrasive material, such as coal dust, can accumulate on each component, the passive barrier coating allows for moisture ingress and, crevice corrosion. Therefore, conventional coatings provide protection for a short life cycle.
Locally, the company started testing the active seal solution with State-owned power utility Eskom to prevent corrosion. The evaluation at Eskom’s Koeberg Insulator Pollution Testing Station (KIPTS) was done from 2013 to 2015. One of the tests exceeded two years at KIPTS, in the Western Cape, with results proving that HRCSA eliminates crevice corrosion. By seeping into the crevices, HRCSA prevents the micro-environment corrosion factors from forming. This development needs to be shared with all who are going to participate in the energisation of sub-Saharan Africa. HRCSA technology, once implemented, will minimise asset maintenance requirements.
“HRCSA provides significant joint protection because of its chemical reaction to steel surfaces. Adhesion of the coating to the metal is owing to the Van der Waals forces and the substrate therefore does not need a profile.”
An added advantage is that HRCSA requires minimal surface preparation and provides a cost-effective, long life cycle, protecting metal. The coating also has a long shelf life, provided that it has been stored according to industry standards.
HRCSA will provide significant protection for infrastructure in Africa, minimising maintenance requirements and thereby being cost effective, as maintenance programmes are costly and disruptive.
Comments
Press Office
Announcements
What's On
Subscribe to improve your user experience...
Option 1 (equivalent of R125 a month):
Receive a weekly copy of Creamer Media's Engineering News & Mining Weekly magazine
(print copy for those in South Africa and e-magazine for those outside of South Africa)
Receive daily email newsletters
Access to full search results
Access archive of magazine back copies
Access to Projects in Progress
Access to ONE Research Report of your choice in PDF format
Option 2 (equivalent of R375 a month):
All benefits from Option 1
PLUS
Access to Creamer Media's Research Channel Africa for ALL Research Reports, in PDF format, on various industrial and mining sectors
including Electricity; Water; Energy Transition; Hydrogen; Roads, Rail and Ports; Coal; Gold; Platinum; Battery Metals; etc.
Already a subscriber?
Forgotten your password?
Receive weekly copy of Creamer Media's Engineering News & Mining Weekly magazine (print copy for those in South Africa and e-magazine for those outside of South Africa)
➕
Recieve daily email newsletters
➕
Access to full search results
➕
Access archive of magazine back copies
➕
Access to Projects in Progress
➕
Access to ONE Research Report of your choice in PDF format
RESEARCH CHANNEL AFRICA
R4500 (equivalent of R375 a month)
SUBSCRIBEAll benefits from Option 1
➕
Access to Creamer Media's Research Channel Africa for ALL Research Reports on various industrial and mining sectors, in PDF format, including on:
Electricity
➕
Water
➕
Energy Transition
➕
Hydrogen
➕
Roads, Rail and Ports
➕
Coal
➕
Gold
➕
Platinum
➕
Battery Metals
➕
etc.
Receive all benefits from Option 1 or Option 2 delivered to numerous people at your company
➕
Multiple User names and Passwords for simultaneous log-ins
➕
Intranet integration access to all in your organisation