AM tech ideal for stainless steel parts manufacturing
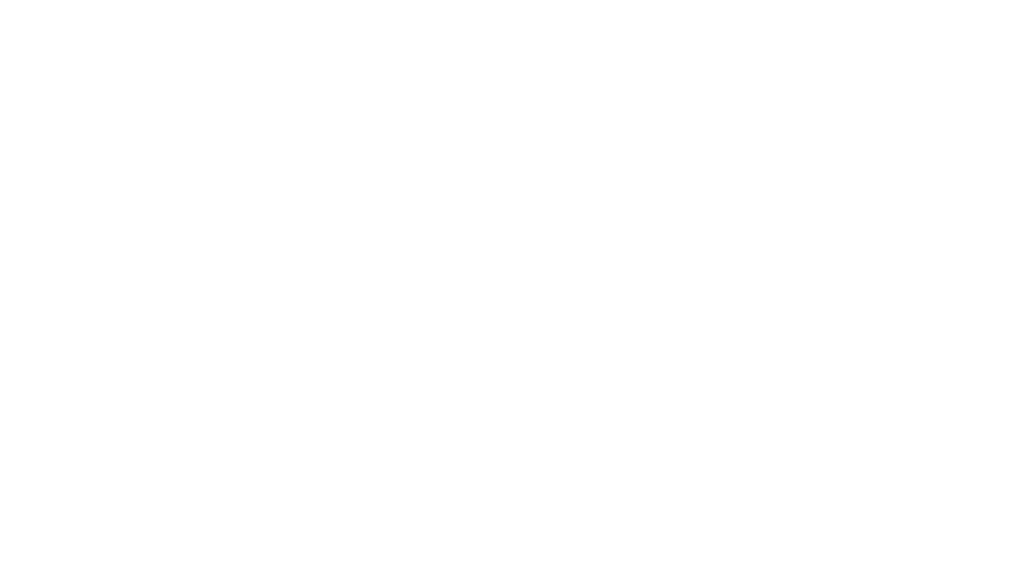
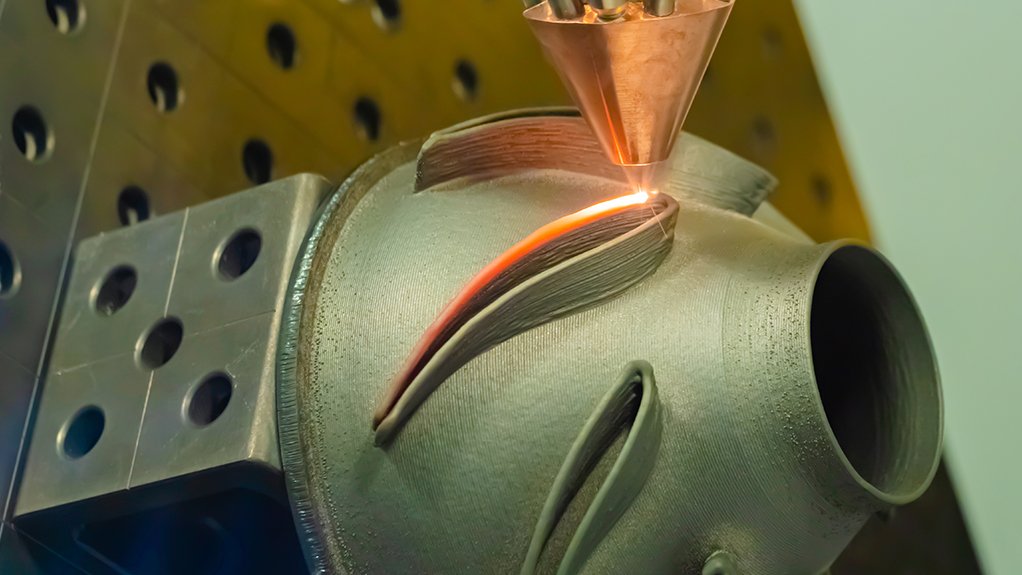
DIRECT METAL DEPOSITION AM technologies allow for new, optimised designs as well as a drastic reduction in lead times
Emerging additive manufacturing (AM) technologies have attracted significant attention owing to an attractive set of properties and attributes. A common feature of AM technologies is the build-up of objects by deposition of material layer upon layer driven by a three-dimensional, or 3D, computer model, thereby achieving near final shape or near net shape. All AM technologies applicable to metals can be used with stainless steels.
Non-profit research organisation International Stainless Steel Forum (ISSF) explains that AM technology processes are “the polar opposite” of many other manufacturing methods, such as machining, which progressively remove material.
ISSF explains that AM technologies will generate a paradigm shift in both operational efficiency and component costs. This is because it allows new, optimised designs as well as a drastic reduction in lead times for prototyping and for spare parts. It also results in smaller and simpler supply chain inventories.
Further developments will increase capabilities, such as new grades in powder form, and improved productivity by more powerful heat sources.
“Stainless steels, with their good corrosion resistance and their wide range of properties, have been used already as one of the preferred AM metallic materials,” says ISSF.
ISSF explains AM technologies such as powder-based fusion (PBF) and direct energy deposition can be beneficial to the stainless steel manufacturing industry.
PBF
PBF involves applying a layer of powder material over a built platform. A laser beam then fuses the layer according to the cross section of the part to be printed. The process of layer and fuses is repeated until the model or part is complete.
ISSF adds that hot isostatic pressing (HIP) processing can be used to reduce porosity to less than 0.2%, restore isotropy, and improve ductility, fatigue life and impact resistance. However, it is expensive and increases the lead time.
ISSF explains that stainless steels are well suited for PBF. A number of grades are available in powder form and new alloys that are impossible to produce by the traditional routes can be produced by gas atomising technology. Further, post-PBF heat treatment and finishing are similar to castings. HIP with rapid gas cooling results in an annealed and quenched metallurgical condition.
Direct Energy Deposition
Direct energy deposition includes two processes, wire arc additive manufacturing (WAAM) and laser metal deposition (LMD).
WAAM is similar to robotised multipass metal inert gas, tungsten inert gas and plasma arc welding. The part is built by successive passes. However, WAAM has more process parameters, which are computer-controlled with sensors to minimise porosity and inclusions.
WAAM requires inexpensive feedstock as it uses wire. It also has a high deposition rate with no part size limitation. Multi-metal deposition is possible and some cold work to increase strength is possible. Final machining is possible on the same machine tool while warping can be reduced by proper sequencing.
WAAM is suited to stainless steels because stainless steel is easy to deposit and welding wire grades are readily available. Post-WAAM heat treatment and finishing are also similar to those of multipass welds.
Similar to WAAM, LMD use a robotised arm to move the deposition head. However, the feedstock is powder which is melted by a focused laser beam. A protective gas, usually argon, is used, explains ISSF.
LMD offers higher productivity than PBF and has the ability to produce larger parts. However, freedom in design is limited. Variations of the process are possible by replacing powder with wire.
LMD offers finer resolution and more alloying possibilities, owing to the use of powder feedstock, compared to WAAM. Advantages of LMD when using stainless steels is that parts can be readily used. It is ideal for repair, overlay and joining.
Comments
Press Office
Announcements
What's On
Subscribe to improve your user experience...
Option 1 (equivalent of R125 a month):
Receive a weekly copy of Creamer Media's Engineering News & Mining Weekly magazine
(print copy for those in South Africa and e-magazine for those outside of South Africa)
Receive daily email newsletters
Access to full search results
Access archive of magazine back copies
Access to Projects in Progress
Access to ONE Research Report of your choice in PDF format
Option 2 (equivalent of R375 a month):
All benefits from Option 1
PLUS
Access to Creamer Media's Research Channel Africa for ALL Research Reports, in PDF format, on various industrial and mining sectors
including Electricity; Water; Energy Transition; Hydrogen; Roads, Rail and Ports; Coal; Gold; Platinum; Battery Metals; etc.
Already a subscriber?
Forgotten your password?
Receive weekly copy of Creamer Media's Engineering News & Mining Weekly magazine (print copy for those in South Africa and e-magazine for those outside of South Africa)
➕
Recieve daily email newsletters
➕
Access to full search results
➕
Access archive of magazine back copies
➕
Access to Projects in Progress
➕
Access to ONE Research Report of your choice in PDF format
RESEARCH CHANNEL AFRICA
R4500 (equivalent of R375 a month)
SUBSCRIBEAll benefits from Option 1
➕
Access to Creamer Media's Research Channel Africa for ALL Research Reports on various industrial and mining sectors, in PDF format, including on:
Electricity
➕
Water
➕
Energy Transition
➕
Hydrogen
➕
Roads, Rail and Ports
➕
Coal
➕
Gold
➕
Platinum
➕
Battery Metals
➕
etc.
Receive all benefits from Option 1 or Option 2 delivered to numerous people at your company
➕
Multiple User names and Passwords for simultaneous log-ins
➕
Intranet integration access to all in your organisation