Assembly-line extension ensures efficient automotive production
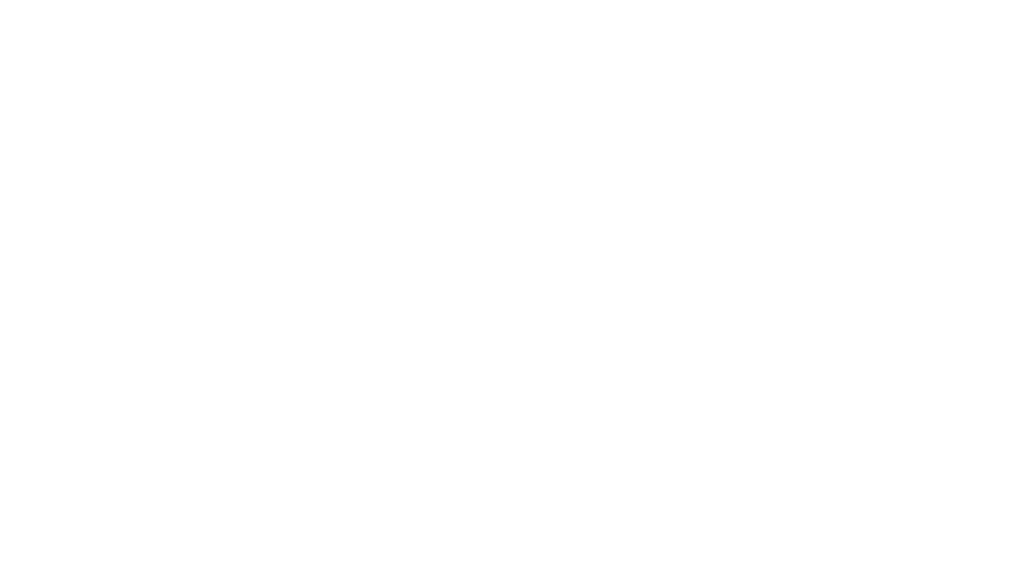
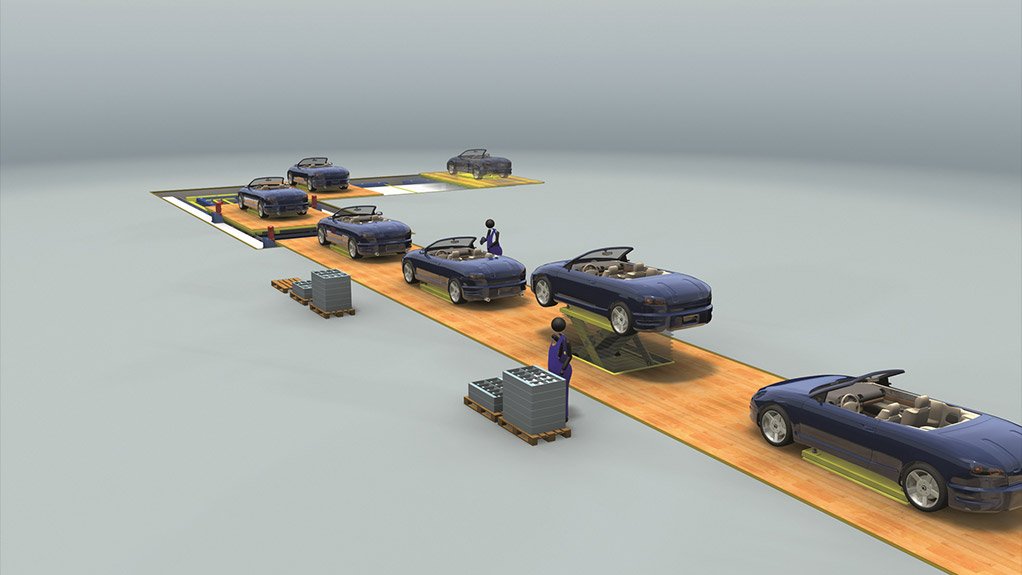
NEW HEIGHTS A height table needs to be built into the system, providing flexibility in changing the height of the stations as the requirement changes
An assembly-line extension at a major automotive producer in Port Elizabeth, in the Eastern Cape, which included replacing the existing MOVITRANS contactless energy transfer system with the latest version, has allowed for more efficient assembly of vehicles on the production line, says multinational drive technology manufacturer SEW-EURODRIVE South Africa electronics support technician Juandre La Cock.
Contactless energy transfer involves electricity being transferred without contact from a fixed conductor to one or more mobile users such as the different stations in an assembly line. Developed at the company’s research and development department in Germany, the electromagnetic connection is made through an air gap, making it maintenance- and emissions-free.
The MOVITRANS installed was a 16 kW system to accommodate 38 carriages, with 18 on each of the two lines. Each carriage required 1.5 kW for the hoist, but at different times, while the old system only had 34 carriages.
“The replacement of the existing MOVITRANS system, originally installed in 2006, allows for increasing the production line for vehicles, as a further four skillets were added. “This will increase the number of stations on the assembly line and result in faster assembly of vehicles.”
La Cock explains that there are now effectively more stations manned by more employees on the line. “This means that the production line moves faster and there are more cars as output.”
He states that the system is ideal for mobile applications, and has been tested according to BGV B11 regulations, which provide guidelines on health-related risks in terms of electromagnetic fields. It is also suitable for equipment that is required to travel long distances at high speeds, and for applications in sensitive environments, such as wax and plants where fine dust is prevalent, and paint shops where chemicals are used, as well as in wet and damp environments.
La Cock highlights that the system does not require a cable to move the assembly line, which makes it easier to move vehicles as moving parts, and pieces of equipment remain on the vehicle during vehicle transfer.
The system also assists in identifying the carriage a vehicle is on in the assembly line.
“With each station, it actually identifies the vehicle and knows which parts need to be assembled on the vehicle, and which parts have been assembled already,” states La Cock.
This system is particularly suitable for final assembly plants, trim shops and vehicle body shops.
The implementation of a conveyor system, such as the MOVITRANS system, in an automotive assembly line requires a custom drive concept that must meet the required load-bearing capacity, desired transport speed, existing space restrictions, and relevant conditions pertaining to the application.
MOVIPRO SDC Drive Inverter
The MOVIPRO SDC drive inverter is ideal for horizontal and vertical conveyor applications, as it integrates into all the necessary functions and allows for decentralised installation of up to 15 kW, making it suitable for the assembly line extension in Port Elizabeth.
La Cock emphasises that the system is suitable for installing autonomous drive sectors and networking them, owing to its robust design in terms of reliability and precise positioning requirements. Its modular, standardised design and configurable software components enables it to determine the integration of a variety of functions while reducing the intricacy of the machine or system.
The MOVIPRO SDC provides wireless communication for the MOVITRANS system using WiFi routers.
La Cock says that there being 30 stations along the assembly line with different height requirements added to the complexity of the solution for the automotive manufacturer.
This means that a height table needed to be built into the system, providing flexibility in changing the heights of vehicles at different stations, as the requirement changes for each station, La Cock highlights.
“If you need to have a car positioned at a certain height, maybe to assemble the wheels or underbody, one would be able to change the height at which the car is positioned,” states La Cock.
SEW-EURODRIVE’s scope of work on the project included not only extending the assembly line, but also ensuring that the plant was up to date with the latest technology. This involved resetting all the MOVIPROs, extending a leaky WiFi cable, as well as replacing the MOVITRANS system with the latest version, which had functioned flawlessly to date.
Emerging Tech in Assembly
While emerging digital technologies, such as those used at this assembly plant, are becoming increasingly prominent in the automotive industry, La Cock emphasises the challenge of keeping up to date with the latest technologies, stating that this is crucial in keeping up with competitors.
“We have a group of developers creating and designing all the applications and new technologies to be at the forefront of our competitors at all times. “We disseminate information regarding new products. The digital industry is completely taking over.”
SEW-EURODRIVE will attend the Africa Automation Fair 2019 from June 4 to 6 at the Ticketpro Dome in Northgate, Johannesburg. La Cock says this will be an ideal venue to showcase the company’s products for different industries, and its custom-made solutions for a variety of applications.
“Each plant has its unique way of assembling vehicles. In terms of this, SEW-EURODRIVE conducts an assessment and, based on that, we can supply a custom solution to the client,” he concludes.
Comments
Press Office
Announcements
What's On
Subscribe to improve your user experience...
Option 1 (equivalent of R125 a month):
Receive a weekly copy of Creamer Media's Engineering News & Mining Weekly magazine
(print copy for those in South Africa and e-magazine for those outside of South Africa)
Receive daily email newsletters
Access to full search results
Access archive of magazine back copies
Access to Projects in Progress
Access to ONE Research Report of your choice in PDF format
Option 2 (equivalent of R375 a month):
All benefits from Option 1
PLUS
Access to Creamer Media's Research Channel Africa for ALL Research Reports, in PDF format, on various industrial and mining sectors
including Electricity; Water; Energy Transition; Hydrogen; Roads, Rail and Ports; Coal; Gold; Platinum; Battery Metals; etc.
Already a subscriber?
Forgotten your password?
Receive weekly copy of Creamer Media's Engineering News & Mining Weekly magazine (print copy for those in South Africa and e-magazine for those outside of South Africa)
➕
Recieve daily email newsletters
➕
Access to full search results
➕
Access archive of magazine back copies
➕
Access to Projects in Progress
➕
Access to ONE Research Report of your choice in PDF format
RESEARCH CHANNEL AFRICA
R4500 (equivalent of R375 a month)
SUBSCRIBEAll benefits from Option 1
➕
Access to Creamer Media's Research Channel Africa for ALL Research Reports on various industrial and mining sectors, in PDF format, including on:
Electricity
➕
Water
➕
Energy Transition
➕
Hydrogen
➕
Roads, Rail and Ports
➕
Coal
➕
Gold
➕
Platinum
➕
Battery Metals
➕
etc.
Receive all benefits from Option 1 or Option 2 delivered to numerous people at your company
➕
Multiple User names and Passwords for simultaneous log-ins
➕
Intranet integration access to all in your organisation