Recycling tech mitigates waste
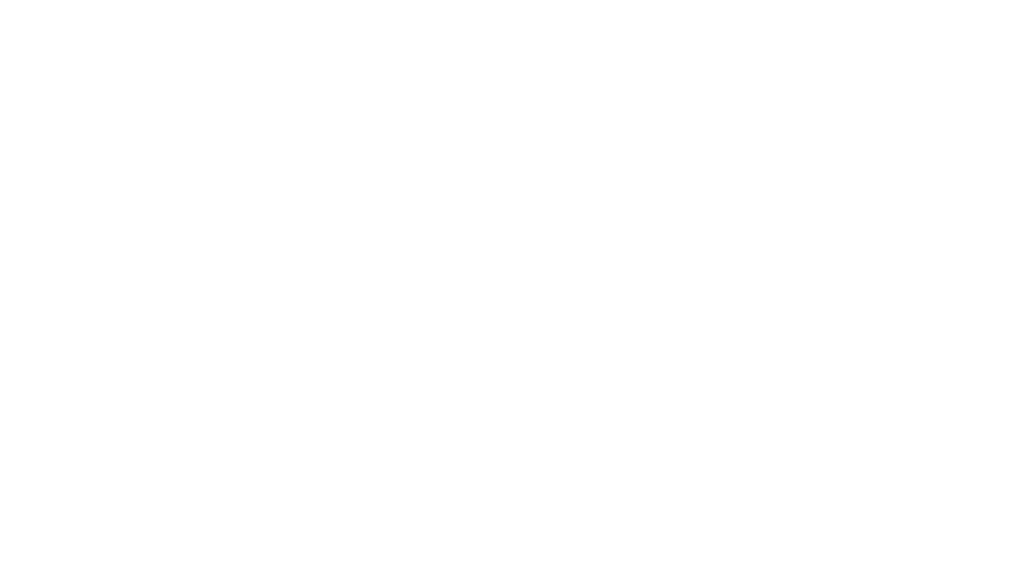
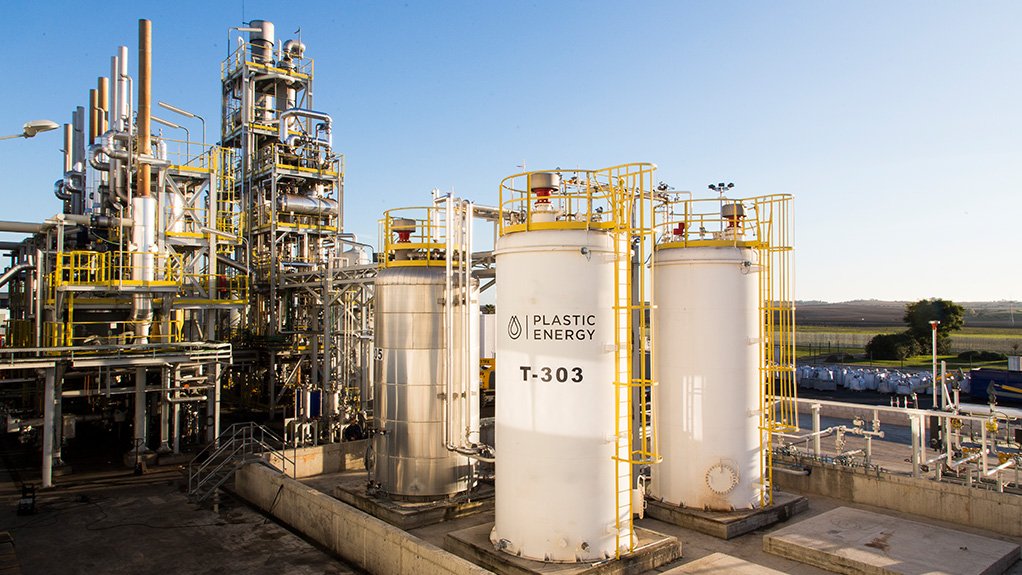
SEVILLE RECYCLING PLANT Plastic Energy’s recycling process transforms difficult-to-recycle plastic waste into an optimal oil feedstock
Plastic production has increased to more than one-million tonnes a day, resulting in a growing plastic waste challenge, which chemical recycling technologies can mitigate by turning the waste into raw materials that can be used to meet current plastic demand.
Chemical recycling company Plastic Energy is helping “to turn the tide on plastic waste”. With two recycling plants in Almeria and Seville, in Spain, the company’s recycling process transforms difficult-to-recycle plastic waste into an optimal oil feedstock, called TACOIL, which replaces fossil oils in the production of new plastic packaging.
“Chemical recycling technologies can break down plastics into their original building blocks, transforming them into valuable, virgin-quality raw materials. Virgin-like plastic feedstock can then be used in high-quality applications such as food packaging,” explains Plastic Energy policy head Adela Putinelu.
With the exception of polyethylene terephthalate bottles, mechanical recycling often downcycles materials with limited food-grade use.
However, chemical recycling can recycle plastics repeatedly, without any deterioration in quality, and can be used in food-grade, contact-sensitive plastic packaging.
Putinelu adds that, used together, mechanical recycling and chemical recycling ensure higher volumes of recycled plastic waste. She explains that demand for high-quality recycled material has increased as a result of regulatory pressure as well as sustainability commitments.
“There is currently a supply shortage of recycled content for plastics, so capacity needs to grow to fulfil current and projected demand.”
Plastic Energy’s process assists in reducing the amount of end-of-life plastics that currently end up in landfills, incinerators and as plastic waste exports while increasing the amount of plastics that are recycled. Its plastic-to-plastic model allows the company to assist in creating a circular economy for plastic waste, as well as reduce the climate impact of plastic production.
Putinelu says the company’s collaborations and partnerships with the entire plastics value chain are key to the scaling up and expansion of chemical recycling. Such collaboration ensures that more plastics are recycled and that more high-quality recycled content can be incorporated into products and packaging for consumer brands.
Plastic Energy’s feedstock, TACOIL, has already been commercialised and incorporated into several packaging products on the European market.
Only about 9% of plastic waste is recycled, with more than 22-million tonnes of plastics leaking into the oceans and the environment every year, according to intergovernmental organisation Organisation for Economic Cooperation and Development. This is causing significant harm to ecosystems and poses health hazards for communities living near landfills.
To address this escalating problem, the collecting, sorting and recycling processes for plastic waste have to drastically improve.
Further, innovative design changes need to be encouraged and implemented to improve recyclability and use plastics more sustainably.
Plastic Energy opened its new dedicated research and development labs at Loughborough University, in England, last year. The labs serve as a base for the company to further develop its technology and TACOIL.
Plastic Energy’s team of researchers and scientists have been working for more than ten years at shared research and development labs at Loughborough University. The company is enthusiastic to continue its work at the university in their dedicated labs.
Further, following the success of its two commercial plants in Spain, Plastic Energy is scaling up its activities by establishing partnerships with other companies to build new plants globally.
In Europe, Plastic Energy has a recycling plant currently under construction in the Netherlands, with partner SABIC, and another plant under construction in France.
Comments
Announcements
What's On
Subscribe to improve your user experience...
Option 1 (equivalent of R125 a month):
Receive a weekly copy of Creamer Media's Engineering News & Mining Weekly magazine
(print copy for those in South Africa and e-magazine for those outside of South Africa)
Receive daily email newsletters
Access to full search results
Access archive of magazine back copies
Access to Projects in Progress
Access to ONE Research Report of your choice in PDF format
Option 2 (equivalent of R375 a month):
All benefits from Option 1
PLUS
Access to Creamer Media's Research Channel Africa for ALL Research Reports, in PDF format, on various industrial and mining sectors
including Electricity; Water; Energy Transition; Hydrogen; Roads, Rail and Ports; Coal; Gold; Platinum; Battery Metals; etc.
Already a subscriber?
Forgotten your password?
Receive weekly copy of Creamer Media's Engineering News & Mining Weekly magazine (print copy for those in South Africa and e-magazine for those outside of South Africa)
➕
Recieve daily email newsletters
➕
Access to full search results
➕
Access archive of magazine back copies
➕
Access to Projects in Progress
➕
Access to ONE Research Report of your choice in PDF format
RESEARCH CHANNEL AFRICA
R4500 (equivalent of R375 a month)
SUBSCRIBEAll benefits from Option 1
➕
Access to Creamer Media's Research Channel Africa for ALL Research Reports on various industrial and mining sectors, in PDF format, including on:
Electricity
➕
Water
➕
Energy Transition
➕
Hydrogen
➕
Roads, Rail and Ports
➕
Coal
➕
Gold
➕
Platinum
➕
Battery Metals
➕
etc.
Receive all benefits from Option 1 or Option 2 delivered to numerous people at your company
➕
Multiple User names and Passwords for simultaneous log-ins
➕
Intranet integration access to all in your organisation