Cleaner fuel crucial – specialists
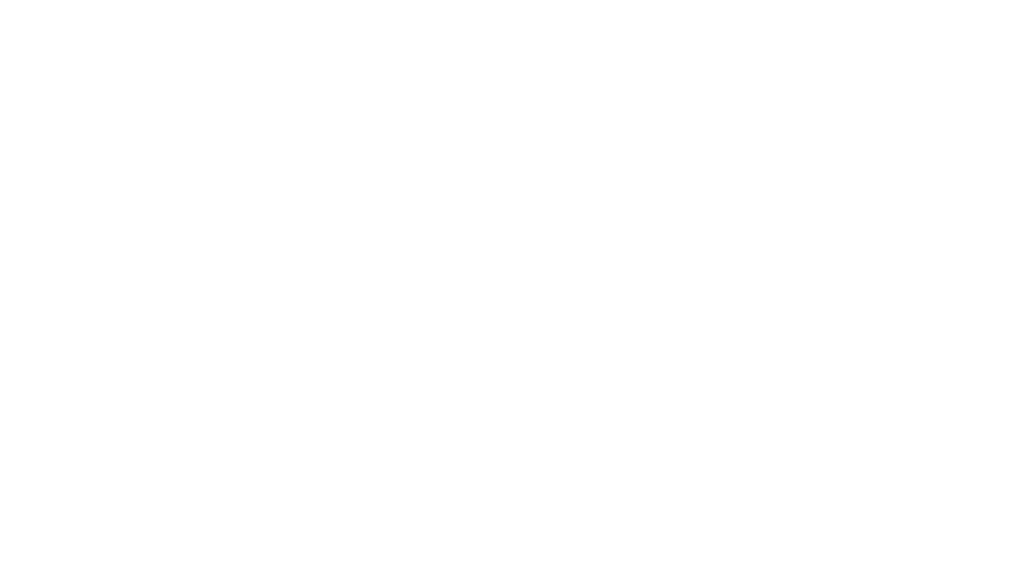
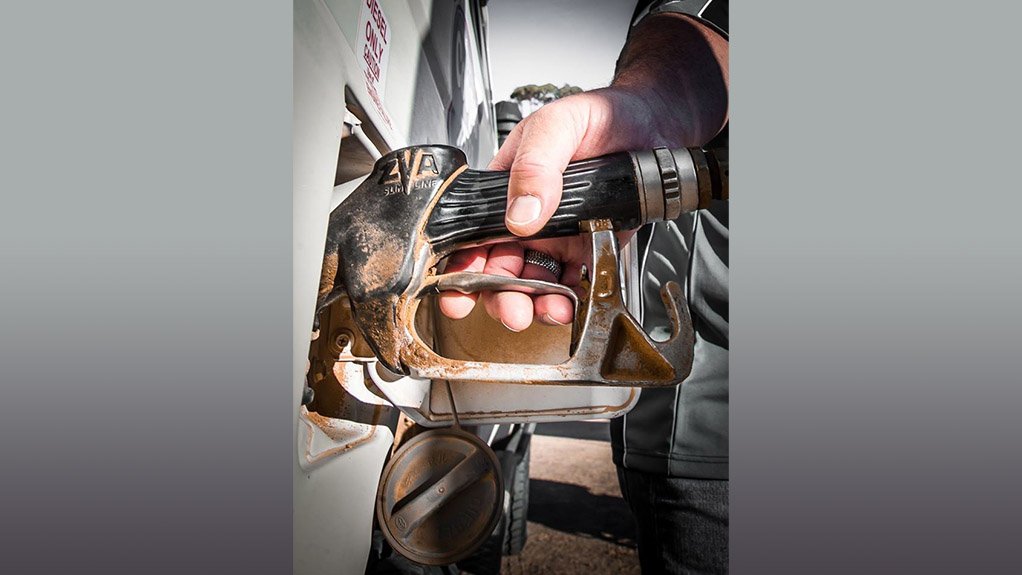
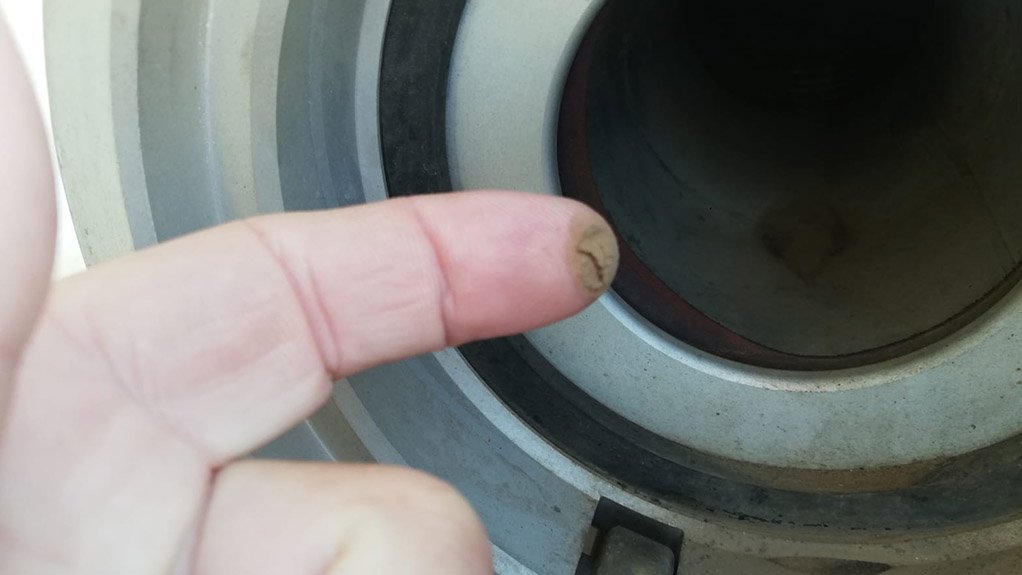
STANDARD OPERATING PROCEDURE ISO-Reliability laments the casual approach to fuel cleanliness and handling
CONTAMINATED ISO-Reliability is concerned about the microscopic level of dirt that affects machine performance and efficiency, evidenced by dust contamination inside a fuel truck delivery hose
International Organisation for Standardisation- (ISO-) compliant tribology and lubrication specialist a ISO-Reliability Partners is unlocking the hidden and lost value in business operations using its “world-class technology” to remove contaminants from fuels and lubricating oils.
ISO-Reliability Partners’ microfine filtration systems include a stainless steel desiccant air breather, which provides moisture absorption as well as radial and depth filtration with around 6 000 times the filtration media, compared with market competitors.
The breather is filled with thousands of desiccant silica gel beads designed to absorb moisture from the air and tank headspace. These change colour when filters need to be serviced. The breathers are fitted on diesel and oil bulk holding tanks, gearboxes, and lube and hydraulic systems to capture large volumes of moisture and particulate contamination at low cost.
This makes the technology not only feasible, but also highly recommended in comparison to common options on the market.
ISO microfine filtration solutions and wear particulate analysis offerings came about after ISO-Reliability Partners CEO and founding member Craig FitzGerald identified fluid contamination as the initial driver behind the vast majority of equipment failures.
FitzGerald’s career and knowledge about fluid cleanliness spans 25 years, leading to the development of highly effective methods of exclusion and removal of all forms of hydrocarbon contaminants plaguing today’s high power, high precision industrial equipment.
After studying fuel and oil samples and the subsequent impact on equipment performance worldwide, FitzGerald discovered that ISO cleanliness of fuels and oils not only played a considerable role in equipment uptime and reliability, but that standards differed around the world.
“According to the South African Bureau of Standards SANS 342:2016, the maximum water content allowed in automotive diesel fuel is 350 mg/kg, with total contamination of particulate matter being 24 mg/kg.”
The US government has a tighter specification of 10 mg/L (about 12 ppm) for particulate matter. However, FitzGerald notes that, most importantly, neither address particle size.
While most fuel filters recommended by engine manufacturers have a nominal pore size of 10 μm, studies reveal that the critical particle size for initiating significant abrasive wear in rotary injection fuel pumps and in high-pressure fuel injection systems is from 1 μm to 7 μm.
However, as designs to reduce emissions result in higher rail and injector pressures, the tighter clearances have less tolerance for solids, moisture and impurities in the fuel.
Consequently, some engine manufacturers are now specifying filters with pore size as low as 2 μm, says FitzGerald. However, moisture and dust particles that can pass through a 2-μm filter can easily damage the injection parts of a diesel engine. “The present standard is therefore not strict enough.”
SANS 342:2016 has made strides towards reduced engine failures with the inclusion of ISO 12156-1 for fuel lubricity, an essential assessment. “It must be noted that testing is done at the refining stage, yet contaminants continue to enter well after the fuel is given the green light for quality.”
Traditionally, removing contaminants is an expensive and arduous task. It cannot be fixed by filtering the fuel through in-line filters only. FitzGerald explains that, after refining, fuel passes through numerous tankers, trucks, and storage vessels before it reaches the end-user.
Owing to this, there are many potential sources of unwanted contamination. Older fuel tanks, particularly those made of black iron, are highly susceptible to internal rust and corrosion.
Because of corrosion, fuel that was previously clean could be contaminated when introduced to a tank that has internal rust build-up. During transport constant vibrations and sloshing could detach particulates.
“Air breathers throughout industry are insufficient,” says FitzGerald. High volumes of dust and water moisture enter each time fuel is transferred, further exacerbating the problem.
Water moisture in diesel fuel is one of the most troubling types of contaminants, and also one of the toughest to combat in large bulk fuel tanks. Contamination and build-up of water is difficult to spot, unless it is regularly tested for.
This is an issue for tanks not fitted with fine particulate and desiccant filtration.
FitzGerald points out that the path to contamination-free fuels relies on a combined effort from the refiners to the transporters, storage depots, handlers and end-users, who all play their part in minimising contamination entry.
The ultimate responsibility lies with the end-user to ensure that, prior to use, fuels are polished with multipass microfine filtration systems such as those exclusively manufactured by Johannesburg-based ISO-Reliability Partners.
Comments
Press Office
Announcements
What's On
Subscribe to improve your user experience...
Option 1 (equivalent of R125 a month):
Receive a weekly copy of Creamer Media's Engineering News & Mining Weekly magazine
(print copy for those in South Africa and e-magazine for those outside of South Africa)
Receive daily email newsletters
Access to full search results
Access archive of magazine back copies
Access to Projects in Progress
Access to ONE Research Report of your choice in PDF format
Option 2 (equivalent of R375 a month):
All benefits from Option 1
PLUS
Access to Creamer Media's Research Channel Africa for ALL Research Reports, in PDF format, on various industrial and mining sectors
including Electricity; Water; Energy Transition; Hydrogen; Roads, Rail and Ports; Coal; Gold; Platinum; Battery Metals; etc.
Already a subscriber?
Forgotten your password?
Receive weekly copy of Creamer Media's Engineering News & Mining Weekly magazine (print copy for those in South Africa and e-magazine for those outside of South Africa)
➕
Recieve daily email newsletters
➕
Access to full search results
➕
Access archive of magazine back copies
➕
Access to Projects in Progress
➕
Access to ONE Research Report of your choice in PDF format
RESEARCH CHANNEL AFRICA
R4500 (equivalent of R375 a month)
SUBSCRIBEAll benefits from Option 1
➕
Access to Creamer Media's Research Channel Africa for ALL Research Reports on various industrial and mining sectors, in PDF format, including on:
Electricity
➕
Water
➕
Energy Transition
➕
Hydrogen
➕
Roads, Rail and Ports
➕
Coal
➕
Gold
➕
Platinum
➕
Battery Metals
➕
etc.
Receive all benefits from Option 1 or Option 2 delivered to numerous people at your company
➕
Multiple User names and Passwords for simultaneous log-ins
➕
Intranet integration access to all in your organisation