Upgrade may be deemed field proven this year
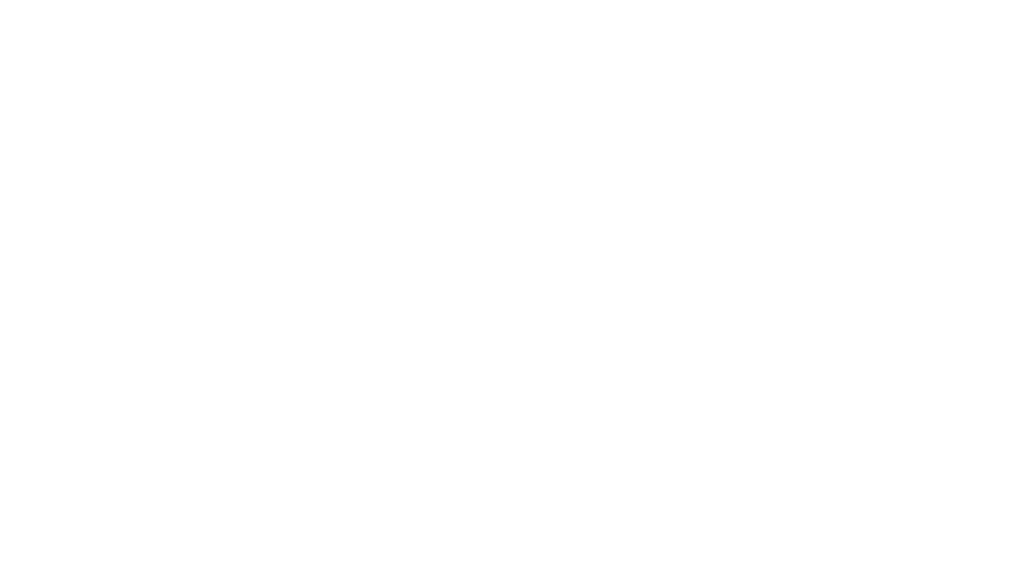
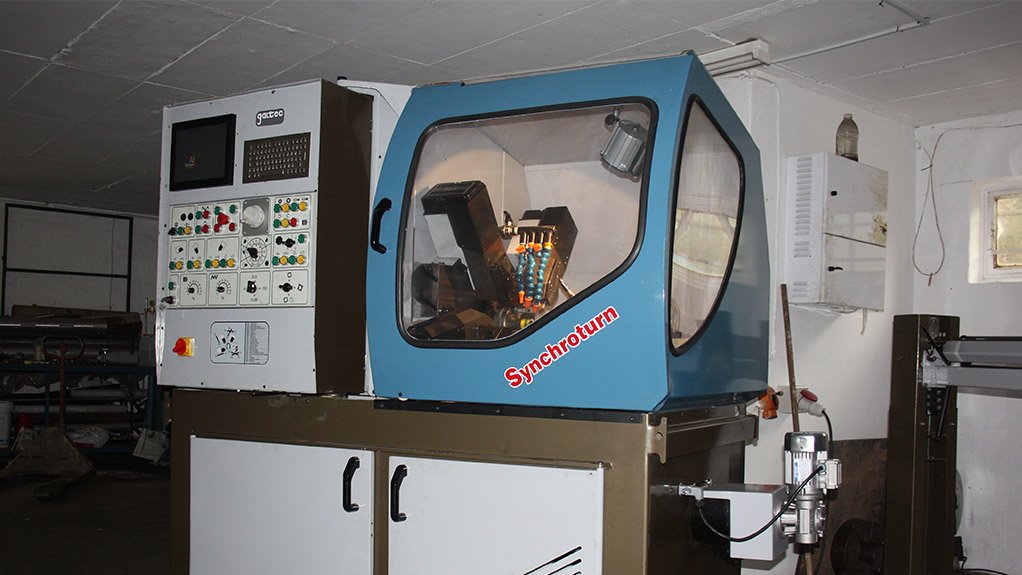
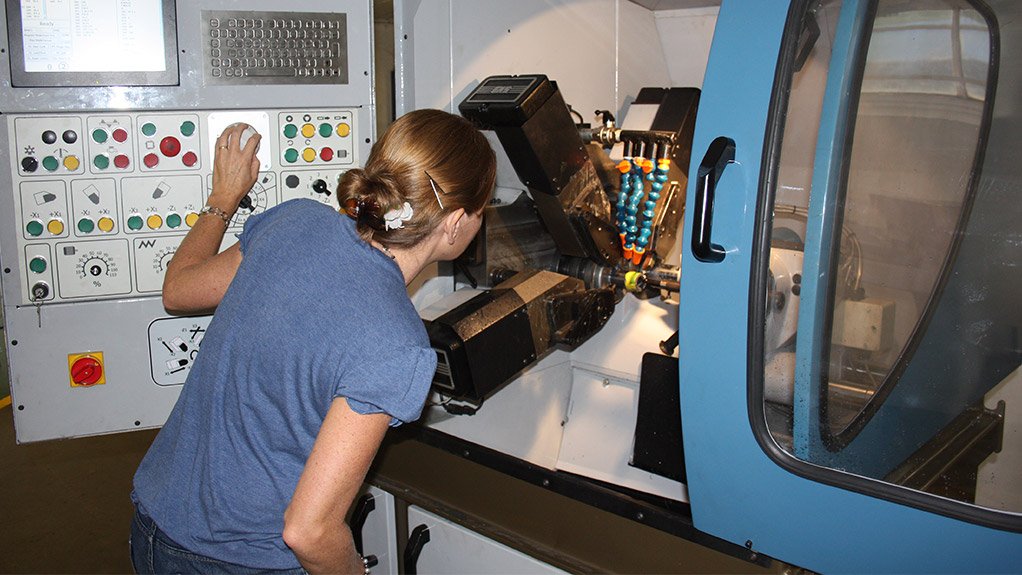
FASTER MANUFACTURING The Synchroturn can accommodate up to four tools working simultaneously on a single workpiece
SKILLS SHORTAGE There is a dwindling pool of tool setters who have the necessary skills to set cam automatic lathes
Local lathe manufacturer FAS Machine Tools has upgraded its FAS Synchro-turn computer numerically controlled (CNC) lathe to offer improved machining capability, which is expected to be deemed field proven by the end of the year.
Since launching the upgraded Synchroturn in January 2012, FAS Machine Tools has only sold three units – two in Gauteng and one in KwaZulu-Natal. The company attributes this to its cautious marketing strategy, which it will continue to employ until the upgraded Synchroturn is deemed field proven, says FAS Machine Tools CEO Peter Frow.
The upgraded lathe now includes bespoke software and control systems, enabling the parallel operation of six axes, Frow tells Engineering News.
The Synchroturn lathe uses a Galtec multiprocessor controller, which can execute four programs simultaneously, enabling the parallel working of several tools.
Industry-standard G-Codes are accepted by the upgraded lathe to program tool movements, while the Synchroturn is regarded as user friendly by operators, says FAS.
In October 2011, Engineering News reported that FAS Machine Tools started producing the Synchroturn six-axis, multi-slide range of CNC lathes, which are typically two to three times quicker than conventional CNC lathes.
The Synchroturn six-axis lathe accommodates up to four tools working simultaneously on a workpiece and has fast feed-and-chuck times, owing to the electromechanical chucking system.
The lathe is available in 60 mm or 42 mm spindle sizes. It has a feed-and-chuck time of one second, while an eight-station turret, with a 0.5-second index time, moves in two axes and is used mainly for internal working.
The independent turning slide also moves in two axes and is used for external working; the independent forming slide moves in one axis for plunge working and the independent parting slide moves in one axis for parting off. The lathe comes with a parts separator and Swarf conveyor.
Frow explained in 2011 that Synchroturn was aimed at industries that use turned parts in quantity. Such industries include the automotive, plumbing and bathroom fitting, electrical equipment, appliance and irrigation sectors.
Meanwhile, in October 2012, Engineering News published a research paper written by Frow, entitled Horses for Courses: A Strategic Overview of the Production Turning Industry in South Africa, in which he identifies that a large number of industries, including the automotive, appliance, electronics and bathroom fittings, as well as other industries and products, use turned components.
The research paper stated that some of these components are made in-house by the product manufacturer, while others are subcontracted to specialist repetition-turning ‘job shops’. The component types and sizes vary enormously, as do the batch sizes.
“Where batch sizes are larger than 100, particularly more than 1 000, the components will typically be made on one or other type of production lathe,” he stated.
Use of a production lathe means the tool movements are achieved automatically. Thus, once set, such a lathe can produce components without any direct operator action, except for loading the raw material.
“In the production-turning stakes, it is important to select the best machine for the job.
“This is one that yields the lowest cost for a particular component and batch size,” said Frow.
Generally speaking, the production-turning industry uses two distinct types of production lathes – cam automatic lathes and CNC lathes.
Frow’s paper highlights that the design of the cam automatic lathe was pioneered more than 100 years ago and it uses cams for achieving tool movements. The lathes are characterised by fast cycle times and long set-up times.
In the paper, he explain that CNC lathes were developed in the 1970s, initially as hard-wired numerically controlled machines, but they soon incorporated microprocessors, hence the term CNC. These lathes have relatively long cycle times compared with cam-operated lathes, especially when manufacturing smaller components. However, they are far more user friendly and have relatively short set-up times.
“Cycle time is a function of the metal-removal rate of the different tools, the number of tools that can be made to work simultaneously on the workpiece and the time taken for nonproductive or idle operations, such as the feeding of material and the indexing of tools,” states Frow.
The paper states that to improve a lathe’s cycle time, one must improve efficiencies of the metal removal rate, ensure that the maximum number of tools are working simultaneously and reduce the duration of idle operations.
He points out that the cam- operated multispindle lathe works on six components in various stages of completion at any one time. Thus, it has as many as 12 tools cutting simultaneously.
Frow highlights that the cam-operated multispindle lathe was developed in the late nineteenth century and still produces the quickest cycle times of any production lathe.
“However, South Africa has less than 150 of this type of machine in regular operation and the most common (about 2 500) of the cam automatics in the country is of the single-spindle type,” he explains.
Frow notes that these machines can typically have four tools working simultaneously. They use the plunge-forming technique extensively, where tools having a particular shape are advanced into the workpiece along an axis perpendicular to the spindle axis.
“By contrast, CNC lathes use single-point tools and generate the required shapes with a digitally programmed tool path. Form tools can generally be applied while end working is taking place using the overlapping technique.
“To select the best machine for a particular application, one should plot the cost-effectiveness curve of each machine being considered,” says Frow.
He states in his paper that there is a dwindling pool of tool setters who have the necessary skills to set cam automatic lathes. Each job also requires a set of job-specific cams, with the number of persons capable of designing optimum cams also having decreased.
“The majority of CNC lathes in South Africa consist of turret and single-gang-tool lathes, although there are also a fair number of dual-gang-tool-type lathes,” Frow adds.
“At a macro level, the net effect of this is a tendency to drive component prices upward, making South Africa less competitive in a global market,” he says.
Frow notes in the research paper that imported multislide lathes have cycle times comparable with those of cam automatics, but they are, unfortunately, expensive. About three conventional CNC lathes can be bought for the price of one imported multislide CNC lathe.
Further, he highlights that, despite fierce competition from the Far East, South Africa is still manufacturing CNC machines.
“The weak rand drives up the cost of imported machinery, which works in favour of local machine tool manufacturers,” Frow concludes.
Comments
Announcements
What's On
Subscribe to improve your user experience...
Option 1 (equivalent of R125 a month):
Receive a weekly copy of Creamer Media's Engineering News & Mining Weekly magazine
(print copy for those in South Africa and e-magazine for those outside of South Africa)
Receive daily email newsletters
Access to full search results
Access archive of magazine back copies
Access to Projects in Progress
Access to ONE Research Report of your choice in PDF format
Option 2 (equivalent of R375 a month):
All benefits from Option 1
PLUS
Access to Creamer Media's Research Channel Africa for ALL Research Reports, in PDF format, on various industrial and mining sectors
including Electricity; Water; Energy Transition; Hydrogen; Roads, Rail and Ports; Coal; Gold; Platinum; Battery Metals; etc.
Already a subscriber?
Forgotten your password?
Receive weekly copy of Creamer Media's Engineering News & Mining Weekly magazine (print copy for those in South Africa and e-magazine for those outside of South Africa)
➕
Recieve daily email newsletters
➕
Access to full search results
➕
Access archive of magazine back copies
➕
Access to Projects in Progress
➕
Access to ONE Research Report of your choice in PDF format
RESEARCH CHANNEL AFRICA
R4500 (equivalent of R375 a month)
SUBSCRIBEAll benefits from Option 1
➕
Access to Creamer Media's Research Channel Africa for ALL Research Reports on various industrial and mining sectors, in PDF format, including on:
Electricity
➕
Water
➕
Energy Transition
➕
Hydrogen
➕
Roads, Rail and Ports
➕
Coal
➕
Gold
➕
Platinum
➕
Battery Metals
➕
etc.
Receive all benefits from Option 1 or Option 2 delivered to numerous people at your company
➕
Multiple User names and Passwords for simultaneous log-ins
➕
Intranet integration access to all in your organisation