Company advances electric motor curing
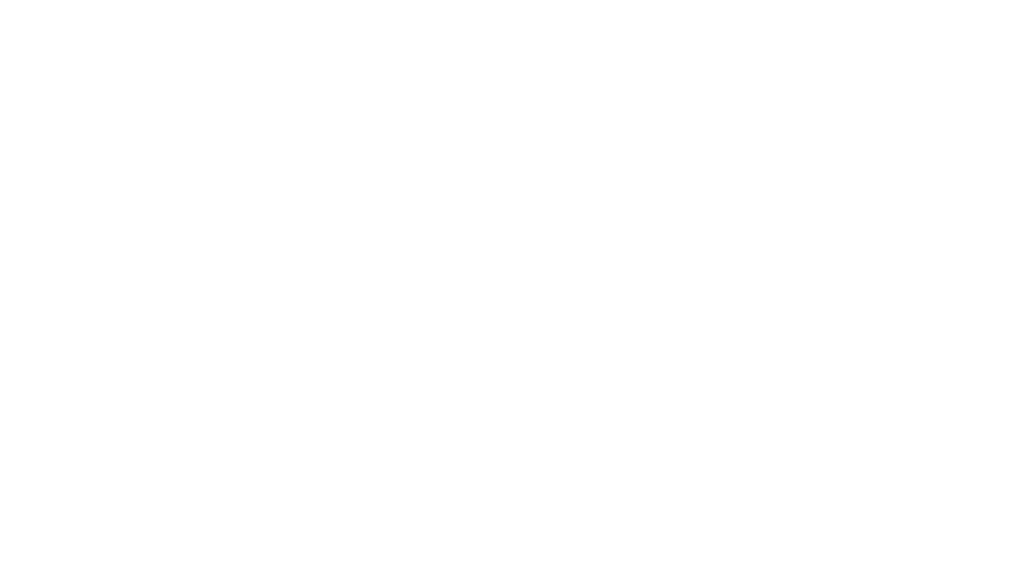
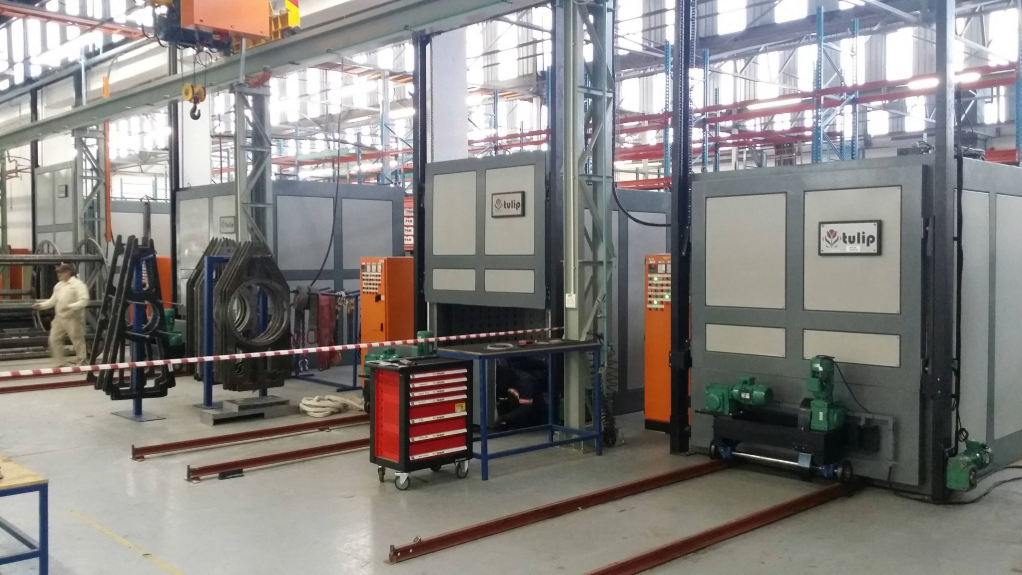
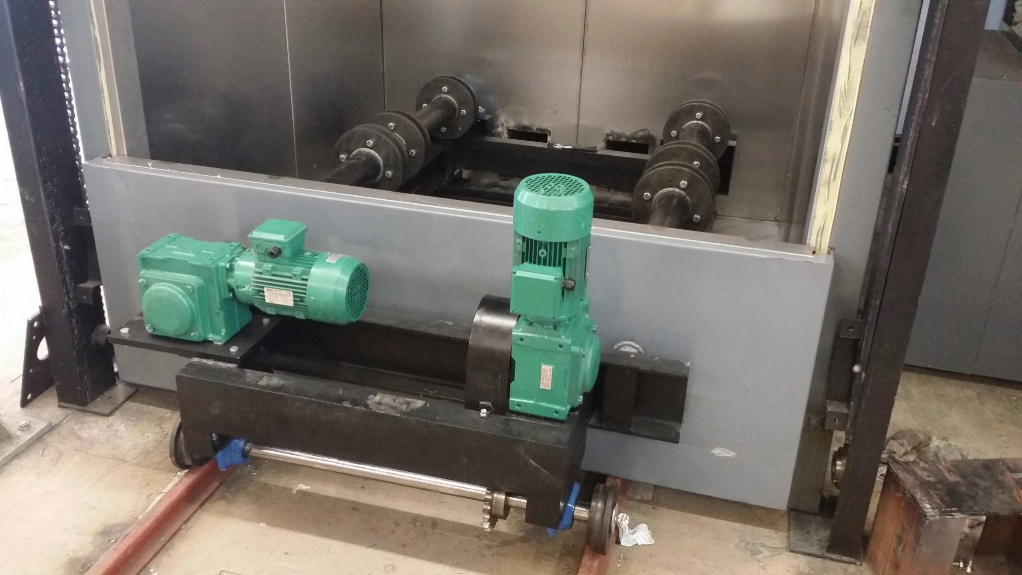
EVEN DISTRIBUTION With rotary curing, the product is slowly rotated, preventing resin accumulation and ensuring even distribution
MINIMAL EXPOSURE The heavy duty design of the outer structure, combined with the flexible design of the inner shell, ensures minimal exposure to stresses
Johannesburg-based engineering firm Tulip Technique’s Tulip rotary curing oven offers an advanced solution for the post-vacuum pressure impregnation (VPI) curing of electric motors, particularly those insulated with silicone resin.
The rotary feature of the Tulip ovens enhances the curing process by ensuring even distribution of resin within the motor coils. During the VPI process, motors are immersed in resin and then baked to set the material.
In static ovens, the liquid resin tends to drip and accumulate at the bottom, leading to inefficiencies.
“With rotary curing, the product is slowly rotated, preventing resin accumulation and ensuring even distribution,” Tulip Technique founder and technical director Wim van Dijk explains, noting that this results in less resin loss and a more uniformly cured assembly.
Temperature control and uniformity are crucial in the curing process. Continuous rotation in the rotary ovens allows for all parts of the motor to pass through different temperature zones within the oven.
“Clients have reported significantly reduced process times, owing to the efficiency of our temperature control system,” Van Dijk notes.
The development of these ovens, which was launched in 2014, was driven by a commission from Canadian manufacturer IEC Holden, which required a specialised curing process for traction motors assembled in South Africa.
“The rotary drive principle was not new, but it was applied in a rudimentary way,” Van Dijk says, adding that, previously, rewinders in South Africa had makeshift setups for rotary curing, but that this project enabled the company to innovate and develop a more efficient and reliable system.
The ovens also feature a motor-driven rising door, which improves operational efficiency. Whereas traditional swinging doors require additional space for operation, the rising-door design also improves space use, as it enables the trolley carrying the motor to move in and out of the oven seamlessly.
Additionally, the design provides ergonomic access and control for personnel, while the variable speed drive- (VSD-) controlled geared motor on the oven trolley adds to the flexibility and performance of the curing process.
“We use a VSD on each drive, including the door movement, trolley movement and product rotation, which allows us to set the optimum speed for each operation, ensuring clients need only one spare geared motor for all their Tulip ovens,” he adds.
Durably Built
Tulip Technique’s rotary curing ovens are built for durability, and the construction thereof includes an outer cold face in structural steel, a layer of ceramic fibre insulation and a stainless-steel inner shell.
The heavy duty design of the outer structure, combined with the flexible design of the inner shell, ensures minimal exposure to stresses, Van Dijk states, highlighting that clients can expect the ovens to serve them for at least 30 years.
In addition to the electric motor industry, Tulip Technique’s ovens are used in other sectors such as the polyurethane industry, mining and sugar mills.
The company designs custom-built ovens for clients, addressing unique challenges and offering tailored solutions.
Tulip Technique also ensures continuous support and back-up service for the ovens: an operating and maintenance manual is supplied with every oven, in addition to recommended spares and an electrical schematic drawing.
“We provide training for operating and maintenance staff, ensuring clients get the most out of their ovens,” Van Dijk emphasises.
The ovens are built for intense throughput and are “very forgiving of harsh treatment”, although he stresses that the company is always available to provide service back-up, especially during the initial months following delivery.
Looking ahead, Van Dijk sees a future driven by advancements in materials, quality standards and environmental policies.
“Our efficient design allows us to adapt to various challenges, from materials handling to temperature and moisture sensitivity. With over 40 years of experience, we are well positioned to offer quality thermal processing solutions to clients in established and newly developed industries,” he concludes.
Comments
Press Office
Announcements
What's On
Subscribe to improve your user experience...
Option 1 (equivalent of R125 a month):
Receive a weekly copy of Creamer Media's Engineering News & Mining Weekly magazine
(print copy for those in South Africa and e-magazine for those outside of South Africa)
Receive daily email newsletters
Access to full search results
Access archive of magazine back copies
Access to Projects in Progress
Access to ONE Research Report of your choice in PDF format
Option 2 (equivalent of R375 a month):
All benefits from Option 1
PLUS
Access to Creamer Media's Research Channel Africa for ALL Research Reports, in PDF format, on various industrial and mining sectors
including Electricity; Water; Energy Transition; Hydrogen; Roads, Rail and Ports; Coal; Gold; Platinum; Battery Metals; etc.
Already a subscriber?
Forgotten your password?
Receive weekly copy of Creamer Media's Engineering News & Mining Weekly magazine (print copy for those in South Africa and e-magazine for those outside of South Africa)
➕
Recieve daily email newsletters
➕
Access to full search results
➕
Access archive of magazine back copies
➕
Access to Projects in Progress
➕
Access to ONE Research Report of your choice in PDF format
RESEARCH CHANNEL AFRICA
R4500 (equivalent of R375 a month)
SUBSCRIBEAll benefits from Option 1
➕
Access to Creamer Media's Research Channel Africa for ALL Research Reports on various industrial and mining sectors, in PDF format, including on:
Electricity
➕
Water
➕
Energy Transition
➕
Hydrogen
➕
Roads, Rail and Ports
➕
Coal
➕
Gold
➕
Platinum
➕
Battery Metals
➕
etc.
Receive all benefits from Option 1 or Option 2 delivered to numerous people at your company
➕
Multiple User names and Passwords for simultaneous log-ins
➕
Intranet integration access to all in your organisation