Storage flexibility shown during turbulent time
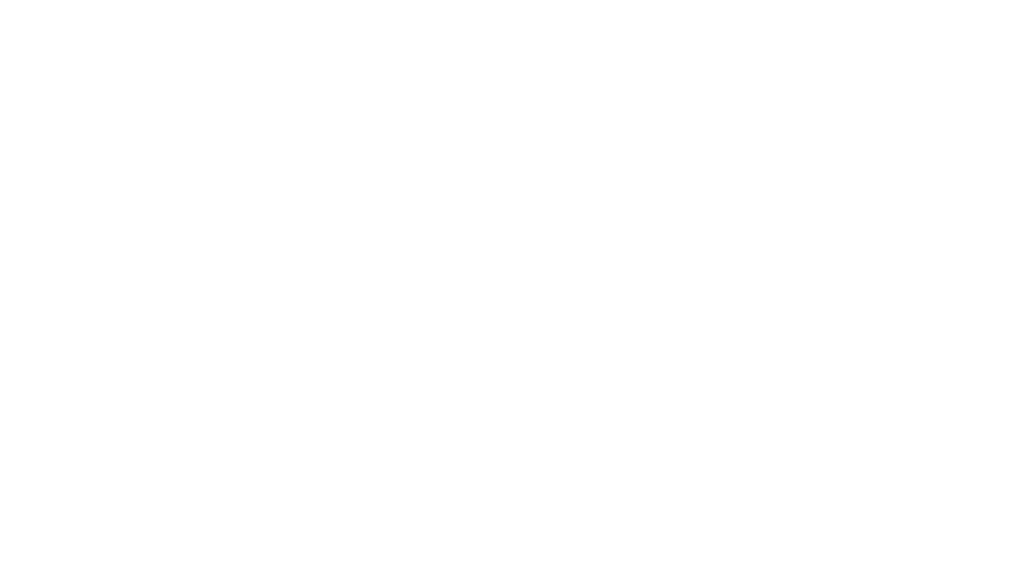
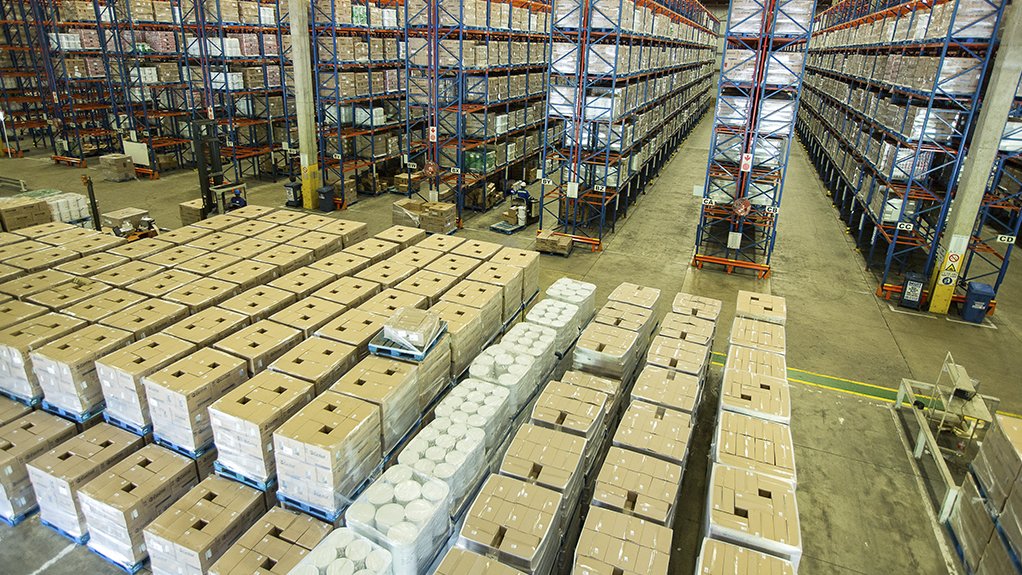
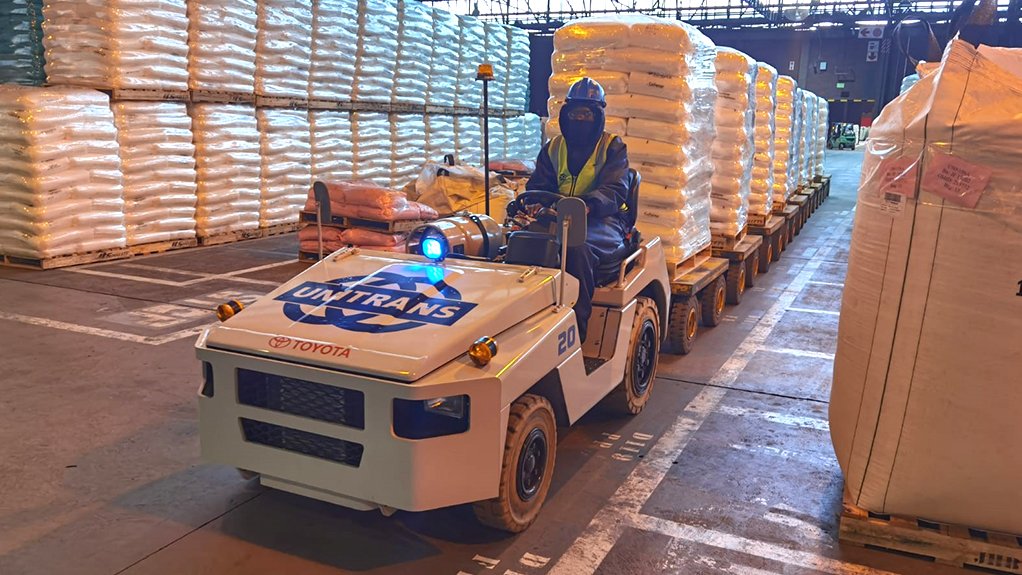
VERSATILE STORAGE The company runs two types of warehousing ¬– specialised warehouses that are customer specific and its own non-exclusive warehouses
MITIGATING SUPPLY DISRUPTIONS Unitrans has had to streamline its operations to manage inbound containers and material to ensure that there was sufficient stock at ports to supply customers
Logistics company Unitrans has shown flexibility in meeting the warehousing and storage needs of customers – particularly amid the effects of Covid-19, and the looting in KwaZulu-Natal and Gauteng in July, on the local market – says Unitrans specialised warehousing and freight GM Ryan Brooke.
“We’ve become flexible as to what we could do. We’ve been constantly looking at what kind of warehouses were strategically available in which to store products, and we are also flexible in the leases we offer. This means that we have been able to open up warehouses when needed and open up a facility at short notice,” explains Brooke.
The company runs two types of warehousing – specialised warehouses that are customer specific and its own non-exclusive warehouses.
Unitrans’ specialised warehousing and logistics services are customer-focused with the company taking over customer facilities and their outbound operations, including warehousing, contract management, long-distance and secondary transport
Brooke stresses that when the Covid-19 lockdown started locally in March last year, the uncertainty in many markets, and whether they would continue operating, accentuated the need for warehousing and storage.
Many Unitrans customers import raw materials, and this was impacted on by ports shutting down, and when ports gradually reopened, shipping agents were selective as to what would be transported on ships.
“Shipping rates also doubled, which makes it difficult to get the full containers required to be imported. Production with our customers and warehouses never stops and is constant throughout the year, so we needed to ensure that there was space where we could store customer products when stock could not be distributed and they needed facilities to store inventory.”.
He adds that Unitrans had to streamline its operations, in addition to streamlining its forwarding and clearing division Unitrans Freight Forwarding and Clearing (UFFC), to manage inbound containers and material to ensure that there was sufficient stock at ports to supply customers.
Flexible Logistics
Unitrans and local ports were also affected by the cyberattacks on State-owned entity Transnet’s port terminals in July this year, as the Port of Durban, in KwaZulu-Natal, shut down for a week and affected Unitrans’ imports and exports.
However, the company was able to keep containers and stored them at its depots while waiting for ports to reopen.
Brooke stresses that the company’s expertise and experience in running food grade warehouses ensured strict adherence to hygiene requirements necessitated by the Covid-19 pandemic.
Unitrans also employs a three-shift pattern to keep operations running and to ensure adherence to legal limits for working hours while maintaining seven day operations. When employees test positive for Covid-19, the company has to remove a whole shift for quarantine, highlighting the need for flexible shifts.
“Durban was under pressure to supply raw material to the local market and continue exports. Customers were under pressure to store their products, so we offered a rebate and three months of storage at our facilities so that they would not incur high storage costs, and keep their margins in line with the sale. We had the flexibility of keeping stock around our operations in Gauteng, KwaZulu-Natal and the Western Cape. Offering flexible storage at our facilities enabled our customers to build up stock.”
Further, Brooke affirms that the company allowed customers to use its facilities as overflow facilities during the looting and unrest in July – clients were reluctant to store product in KwaZulu-Natal, so Unitrans opened its facilities outside KwaZulu-Natal for this purpose.
Unitrans also had to hire vehicles at elevated costs to ensure that deliveries continued, which, in turn, contributed to keeping customer service levels high.
The company leveraged its line haul operations, which were used to moved stock from KwaZulu-Natal directly to clients in Gauteng. This has created further flexibility in terms of which locations clients can store and deliver stock from.
“We also maintained the security of our depots during the looting, and engaged with local communities to assist and secure our depots, as local taxi organisations also contributed to the safeguarding of our facilities. We’ve maintained our digital, online presence, but also had to keep our feet on the ground and show a presence on site. We will always be there for our customers to assist with our sites.”
Brooke adds that, going forward, Unitrans will identify additional warehouses that are suitable for customer requirements, particularly in terms of food-grade storage, with due consideration given to new purpose-built or rented facilities.
The company aims to keep customer products “under cover”, and create better locations and flow for distribution, which will, in turn, reduce transport costs.
“We’ve had to align ourselves to customer expectations and make changes to go the extra mile for our customers and remain adaptable. We have empowered our experienced staff to run any facility and achieve the customer service levels we set,” he concludes.
Comments
Press Office
Announcements
What's On
Subscribe to improve your user experience...
Option 1 (equivalent of R125 a month):
Receive a weekly copy of Creamer Media's Engineering News & Mining Weekly magazine
(print copy for those in South Africa and e-magazine for those outside of South Africa)
Receive daily email newsletters
Access to full search results
Access archive of magazine back copies
Access to Projects in Progress
Access to ONE Research Report of your choice in PDF format
Option 2 (equivalent of R375 a month):
All benefits from Option 1
PLUS
Access to Creamer Media's Research Channel Africa for ALL Research Reports, in PDF format, on various industrial and mining sectors
including Electricity; Water; Energy Transition; Hydrogen; Roads, Rail and Ports; Coal; Gold; Platinum; Battery Metals; etc.
Already a subscriber?
Forgotten your password?
Receive weekly copy of Creamer Media's Engineering News & Mining Weekly magazine (print copy for those in South Africa and e-magazine for those outside of South Africa)
➕
Recieve daily email newsletters
➕
Access to full search results
➕
Access archive of magazine back copies
➕
Access to Projects in Progress
➕
Access to ONE Research Report of your choice in PDF format
RESEARCH CHANNEL AFRICA
R4500 (equivalent of R375 a month)
SUBSCRIBEAll benefits from Option 1
➕
Access to Creamer Media's Research Channel Africa for ALL Research Reports on various industrial and mining sectors, in PDF format, including on:
Electricity
➕
Water
➕
Energy Transition
➕
Hydrogen
➕
Roads, Rail and Ports
➕
Coal
➕
Gold
➕
Platinum
➕
Battery Metals
➕
etc.
Receive all benefits from Option 1 or Option 2 delivered to numerous people at your company
➕
Multiple User names and Passwords for simultaneous log-ins
➕
Intranet integration access to all in your organisation