Company to improve processes with new furnaces
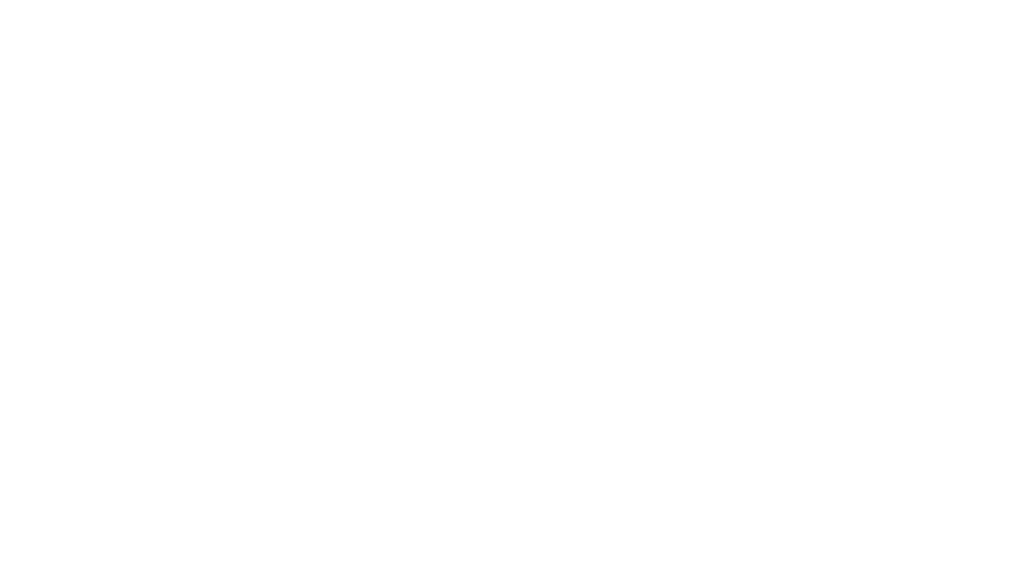
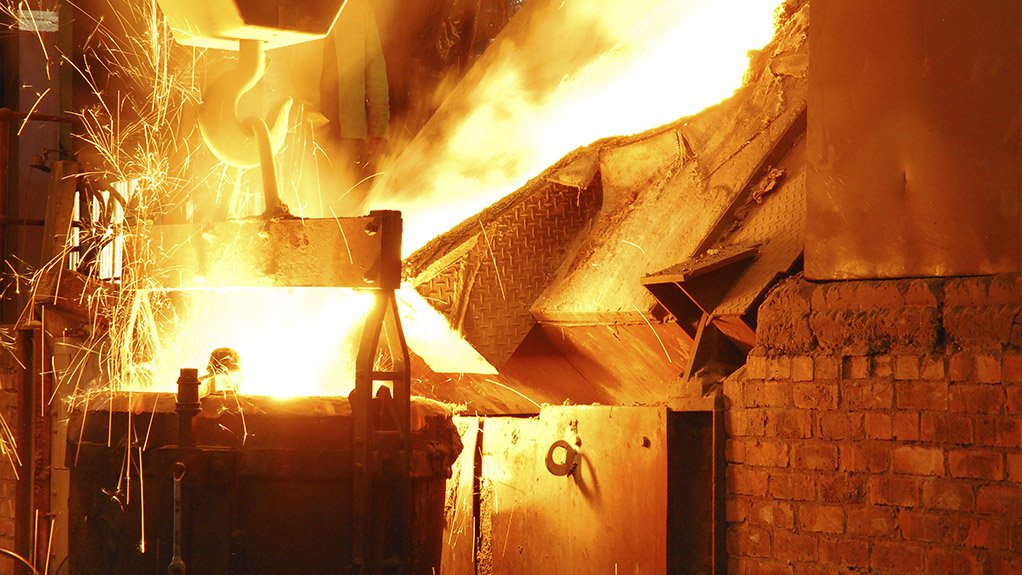
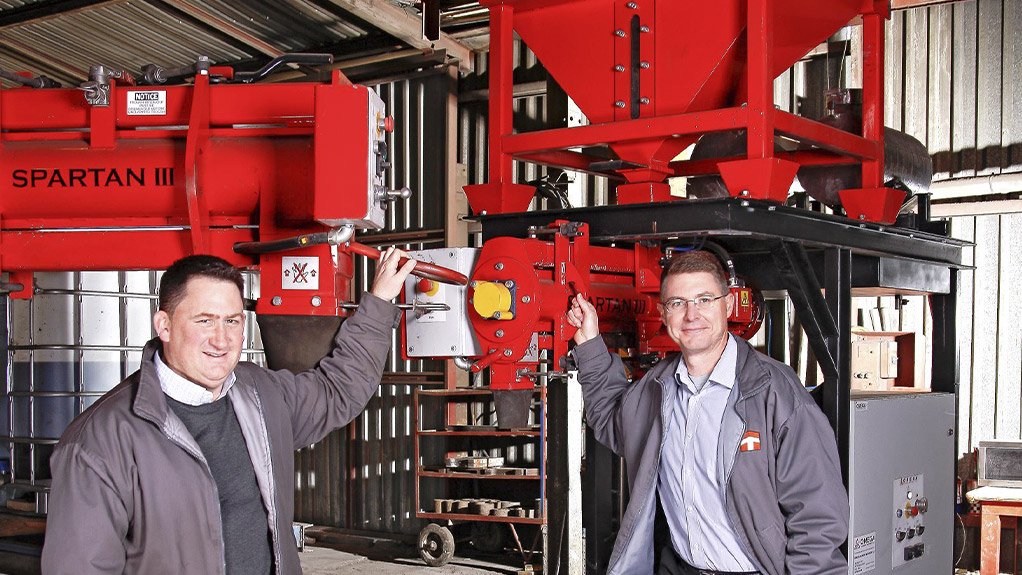
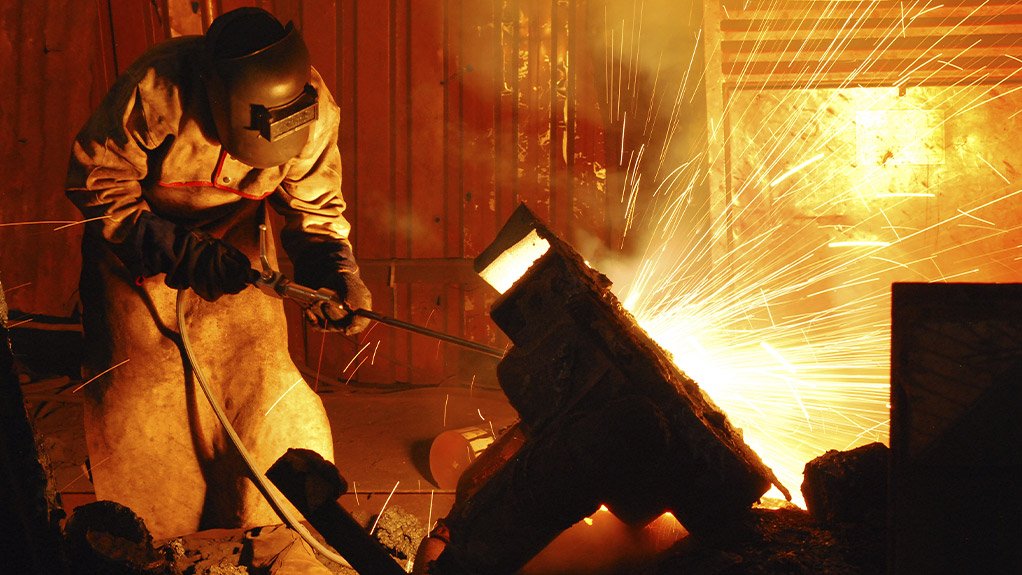
FORGING AHEAD The company has purchased 4 new furnaces to reduce electricity consumption, improve quality and productivity, improving environmental compliance and reducing maintenance costs
COMBATTING THE SLUMP Thomas Foundry is talking to role-players in the railway and renewable energy sector, and looking to expand the company’s product range into the sectors
ENVIRONMENT FRIENDLY INVESTMENTS In 2014, Thomas Foundry installed new sand processing and mixing equipment to improve casting quality, sand usage levels, reduce dumping costs and improve environmental compliance
Local metalworking company Thomas Foundry is set to improve and increase the efficiency of its metalworking and manufacturing processes with the purchase of four new induction furnaces.
The order was placed in September last year to replace three decommissioned furnaces – a 1 t furnace and two 5 t furnaces – with two 6 t furnaces, as well as a 1 t furnace and a 500 kg furnace.
The company expects the delivery and installation to be completed by the end of next month.
These furnaces will reduce electricity consumption and improve overall casting quality by reducing metal holding times, as well as improve environmental compliance and productivity. It will also reduce maintenance costs.
“Some of the equipment was 30 years old, so from a risk-management point of view, access to spares was becoming difficult. Using the new furnaces, it’ll take 90 minutes instead of five hours to do a full meltdown,” enthuses Thomas Foundry CEO Clayton Anderson.
He adds that, over and above the expected improvement in the quality of the metals being made, the company’s overall melting capacity will increase by 2.5 t.
The new furnaces will also allow for more flexibility, as the company can do trial runs using smaller amounts of metal, which was not an option before.
As the previous 1 t furnace was decommissioned, the company’s smallest furnace is currently about 3 t. The smallest amount of metal that can be melted in such a furnace is 1.5 t – it would not be economically viable to melt any amount lower than that in a trial run, says Anderson.
All the furnaces were imported from melting, holding, pouring and heating systems provider Inductotherm, in the US.
Cleaner Castings
To improve quality and minimise the company’s impact on the environment, Thomas Foundry also invested in a new generation sand-reclamation plant that incorporates advanced technology for the recovery, grading, cooling, classifying and cleaning of its foundry sand and reuse in the moulding process.
The decision to acquire such a plant was, firstly, to improve the company’s sand use levels and take advantage of a cost-saving opportunity on the dumping thereof. Sand dumping had reached about 30% of sand use and, in addition to the cost of its transportation and use, would be too excessive for the company.
Anderson maintains that halving this cost will allow for significant savings, which the company achieved.
The investment will also allow for cost-saving opportunities in terms of buying and using chemicals, additives and chromite sand, which he stresses can be a considerable expense.
Secondly, the quality of sand used in the casting and moulding process will improve to a well-rounded sand grain. Anderson illustrates that this results in a superior surface- finish quality in the metals produced, as the updated plant has already started producing better-quality castings.
Thirdly, the environmental improvements will constitute the more efficient use of resources, particularly in terms of reducing dust emissions from the plant.
Anderson stresses that these kinds of investments are crucial for local foundries to continue operating in a difficult economic environment.
Meanwhile, he points out that there were about 500 foundries operating locally 30 years ago, compared with about 120 active foundries currently. Over the past 12 months, four well-established foundries have gone into business rescue or have closed their doors, he adds.
“Future prospects for the local industry depend on what government does over the next six to 18 months to create an investment friendly climate. We believe that the railway and renewable-energy sectors offer attractive opportunities to the local foundry market. We are discussing opportunities with a number of role-players, and are planning to expand our product range into these sectors.”
He adds that the local industry has been hampered by a number of challenges. This includes a lack of work owing to excessive imports; State-owned enterprises with monopolistic pricing powers; lack of dependable electricity supply, among others.
“Foundries that haven’t made this kind of investment over the past five years are closing down. The local industry is in survival mode, and before you thrive you’ve got to survive. There are pockets of opportunity, so we will build from there. Thomas Foundry is also currently pursuing opportunities for export of product to the US,” he concludes.
Comments
Press Office
Announcements
What's On
Subscribe to improve your user experience...
Option 1 (equivalent of R125 a month):
Receive a weekly copy of Creamer Media's Engineering News & Mining Weekly magazine
(print copy for those in South Africa and e-magazine for those outside of South Africa)
Receive daily email newsletters
Access to full search results
Access archive of magazine back copies
Access to Projects in Progress
Access to ONE Research Report of your choice in PDF format
Option 2 (equivalent of R375 a month):
All benefits from Option 1
PLUS
Access to Creamer Media's Research Channel Africa for ALL Research Reports, in PDF format, on various industrial and mining sectors
including Electricity; Water; Energy Transition; Hydrogen; Roads, Rail and Ports; Coal; Gold; Platinum; Battery Metals; etc.
Already a subscriber?
Forgotten your password?
Receive weekly copy of Creamer Media's Engineering News & Mining Weekly magazine (print copy for those in South Africa and e-magazine for those outside of South Africa)
➕
Recieve daily email newsletters
➕
Access to full search results
➕
Access archive of magazine back copies
➕
Access to Projects in Progress
➕
Access to ONE Research Report of your choice in PDF format
RESEARCH CHANNEL AFRICA
R4500 (equivalent of R375 a month)
SUBSCRIBEAll benefits from Option 1
➕
Access to Creamer Media's Research Channel Africa for ALL Research Reports on various industrial and mining sectors, in PDF format, including on:
Electricity
➕
Water
➕
Energy Transition
➕
Hydrogen
➕
Roads, Rail and Ports
➕
Coal
➕
Gold
➕
Platinum
➕
Battery Metals
➕
etc.
Receive all benefits from Option 1 or Option 2 delivered to numerous people at your company
➕
Multiple User names and Passwords for simultaneous log-ins
➕
Intranet integration access to all in your organisation