Fasteners, bearings and welding equipment all within supplier’s ambit
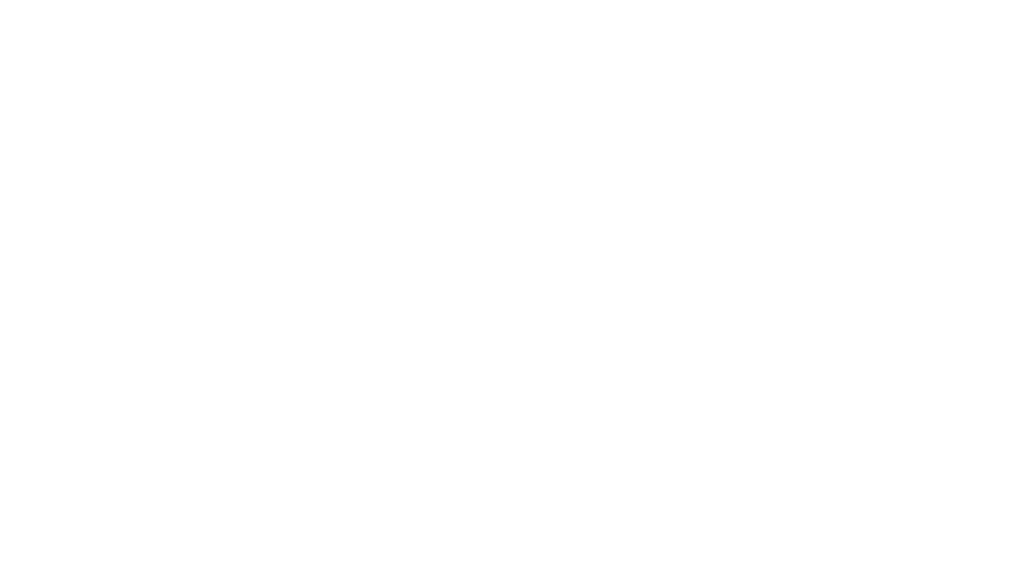
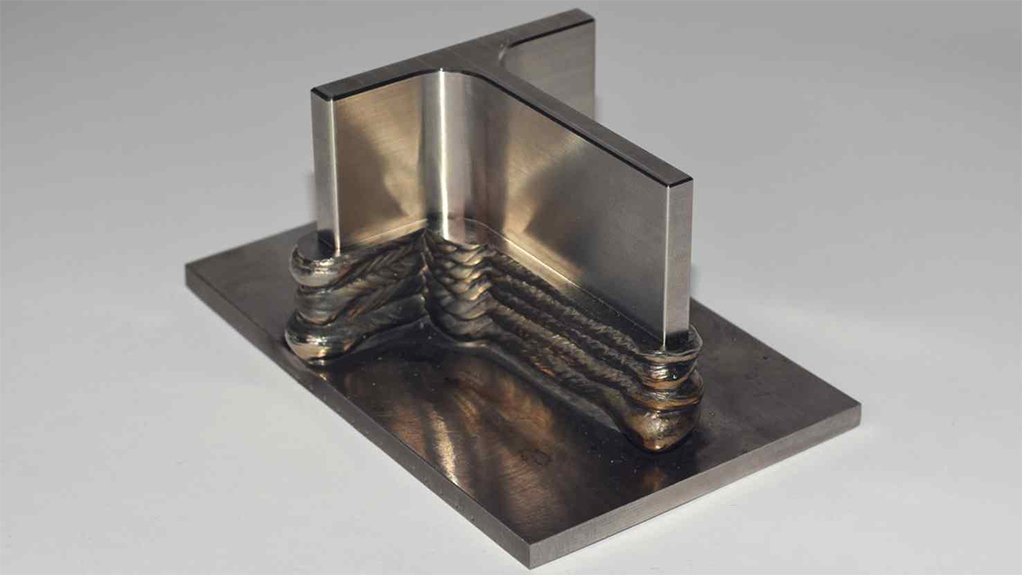
WAAM The WAAM 3D Printing for Metal: Wire Arc Additive Manufacturing with Cold Metal Transfer (CMT) from Fronius
Fasteners, bearings and welding products and equipment are relevant for the metal fabrication sector, which is built on cutting metal and welding it.
If metal cannot be bolted together with fasteners, then it can be welded together, says Bolt and Engineering Distributors (B.E.D) product welding and cutting specialist Michael Calado.
“Further, shifting metals require a bearing replacement or bearing service, for which B.E.D can offer assistance. Fasteners, bearings and welding equipment products, therefore, all fall within our ambit and product portfolio, and we have product specialists to assist our customers with individual requirements.”
B.E.D supplies the Fronius TransPulse Synergic Cold Metal Transfer (CMT) power source, which uses the wire arc additive manufacturing (WAAM) process for projects in the metal fabrication industry.
The wire-based process uses gas metal arc welding, which is a fusion welding process that can print and repair metal parts using three-dimensional (3D) printing processes.
Calado says WAAM is beneficial for the welding and metal fabrication industry because it can be manufactured with minimal material input cost and the amount of scrapped material is “significantly” reduced because its parts are milled from solid blocks of aluminium or titanium.
WAAM and Industry 4.0
The WAAM process can be carried out on B.E.D.’s Austrian supplier Fronius’ TransPulse Synergic CMT power source. This is a digitally-controlled machine that can gather data such as welding current, welding voltage, wire speed and welding speed, making it a relevant technology for Industry 4.0.
“This data enables customers to optimise their production processes, as it allows for the detection and prevention of errors, which may otherwise occur in the manufacturing process,” says Calado.
This capability is not limited to the Fronius TransPulse Synergic CMT range.
It has also been applied to Fronius’ newer TPS/i MIG welder range – Intelligent Revolution, software company iWave’s TIG welding range, the iWave multi-process range - Mig, MMA and High Frequency start AC/DC TIG, the Fronius TransSteel range and plasma cutting systems and consumables manufacturer Hypertherm’s PowerMax 65 Sync.
Further, owing to the impact of Industry 4.0 on the metal fabrication industry, more manufacturing companies have requested welding machines with data-capturing capabilities.
Consequently, more companies are also requesting that a third-party system be connected to an existing welding machine to capture data, either to assist in optimising production or in providing detailed welding reports for the end-user.
However, Calado adds that the introduction of Industry 4.0 also introduced challenges to the metal fabrication industry.
“At the start of the Fourth Industrial Revolution, it became difficult to illustrate to customers the benefits of welding data and how it could help to optimise their manufacturing production processes and reduce costs. However, over time, it has become easier as the benefits have become more apparent.”
WAAM Project
B.E.D recently completed and commissioned a project involving WAAM for specialised welding company Metallurgical and Manufacturing Services (MMS) in Centurion, Tshwane.
The project started towards the end of 2020 and continued throughout 2021 when the metal industry faced challenges in terms of supplying raw materials.
“While this project has been commissioned, WAAM is continuously growing, changing processes and pivoting to supply different industries with specialised welding,” says Calado.
The aim of the project for MMS was to reduce the cost of scarce parts and replicate the necessary ‘off-the-shelf’ parts, owing to the shortage of raw materials in industries, including the metal fabrication sector.
He explains that a milestone of the project involved MMS designing and manufacturing a ring for an application out of nickel-moly 13-4 material. This was the first functional part manufactured by MMS using Fronius’ TransPulse synergic CMT, which was supplied by B.E.D.
The WAAM project has been beneficial for MMS because it falls into its portfolio of specialised welding and manufacturing services, whereby MMS can now supply customers with a variety of welding applications offered by WAAM, adds Calado.
The project entailed the integration of a complete Fronius TransPulse synergic CMT power source with a welding robot from German industrial robot manufacturers Keller and Knappigh Augsburg. The robot was supplied by Pretoria-based machining manufacturer Jendamark.
B.E.D, amid its ongoing involvement with MMS, aims to continue providing welding solutions and supplying Fronius’ CMT power source and synergic lines, which require different materials, such as steel, aluminium, chrome-nickel steel or bronze, to be welded.
While WAAM was initially used for small and manual metal inert gas welding repair work on damaged and worn-out components, Calado says it has become easier to control and integrate robotically, owing to high-precision computer aided design software.
The project required an understanding and knowledge of the 3D printing process, as well as an understanding of the typical base materials and filler wire required for the welding process, he adds.
B.E.D has also supplied Fronius’ TransSteel 3000 Pulse machines and a battery-operated ArcRover 22 welding tractor to the local metal fabrication industry this year.
With B.E.D’s welding division having expanded to Cape Town, with the establishment of a dedicated welding and cutting repair centre there, Calado concludes that the main aim for the expansion is to supply, support and service welding equipment for customers in the Western Cape.
Comments
Press Office
Announcements
What's On
Subscribe to improve your user experience...
Option 1 (equivalent of R125 a month):
Receive a weekly copy of Creamer Media's Engineering News & Mining Weekly magazine
(print copy for those in South Africa and e-magazine for those outside of South Africa)
Receive daily email newsletters
Access to full search results
Access archive of magazine back copies
Access to Projects in Progress
Access to ONE Research Report of your choice in PDF format
Option 2 (equivalent of R375 a month):
All benefits from Option 1
PLUS
Access to Creamer Media's Research Channel Africa for ALL Research Reports, in PDF format, on various industrial and mining sectors
including Electricity; Water; Energy Transition; Hydrogen; Roads, Rail and Ports; Coal; Gold; Platinum; Battery Metals; etc.
Already a subscriber?
Forgotten your password?
Receive weekly copy of Creamer Media's Engineering News & Mining Weekly magazine (print copy for those in South Africa and e-magazine for those outside of South Africa)
➕
Recieve daily email newsletters
➕
Access to full search results
➕
Access archive of magazine back copies
➕
Access to Projects in Progress
➕
Access to ONE Research Report of your choice in PDF format
RESEARCH CHANNEL AFRICA
R4500 (equivalent of R375 a month)
SUBSCRIBEAll benefits from Option 1
➕
Access to Creamer Media's Research Channel Africa for ALL Research Reports on various industrial and mining sectors, in PDF format, including on:
Electricity
➕
Water
➕
Energy Transition
➕
Hydrogen
➕
Roads, Rail and Ports
➕
Coal
➕
Gold
➕
Platinum
➕
Battery Metals
➕
etc.
Receive all benefits from Option 1 or Option 2 delivered to numerous people at your company
➕
Multiple User names and Passwords for simultaneous log-ins
➕
Intranet integration access to all in your organisation