Fuel contaminants result in equipment damage
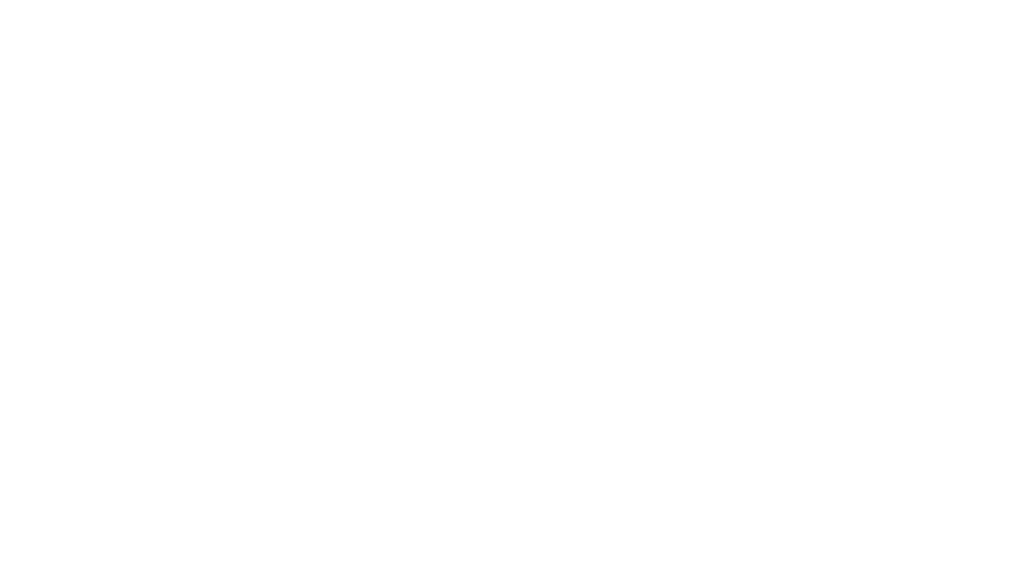
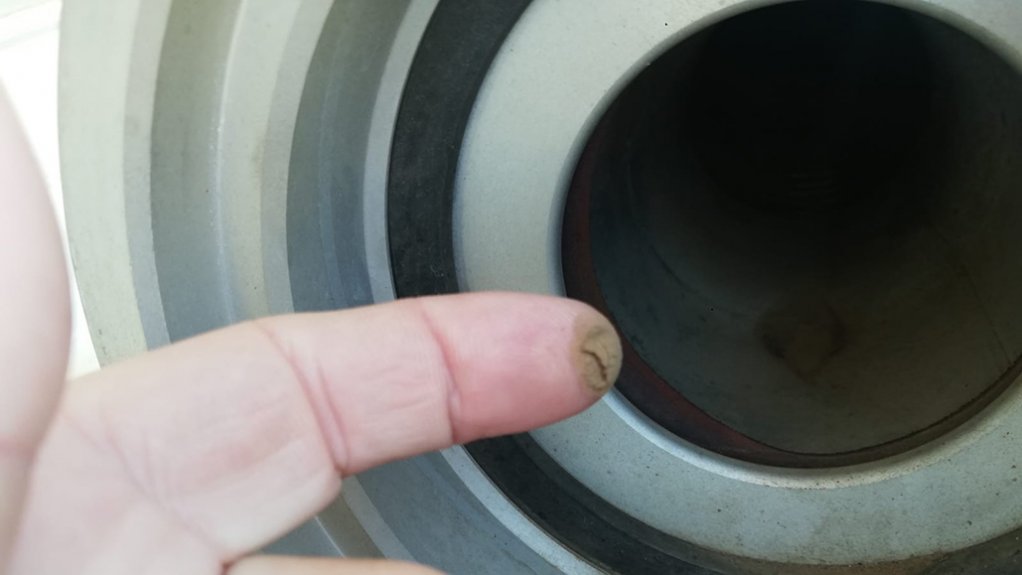
COSTLY CONTAMINATION Fuel is largely contaminated during the distribution process
A lack of knowledge about fuel contaminants results in inadequate fuel protection during the various stages of distribution and storage, and these contaminants can negatively impact on the efficient operation of equipment, says lubrication and industrial equipment specialist ISO-Reliability Partners CEO Craig FitzGerald.
Fuel cleanliness standards vary widely worldwide, with South African refineries having a higher standard of contamination – 24 mg/kg of product – compared with, for example, the standard 10 mg/kg in the US.
While refineries can implement different strategies to improve fuel cleanliness, the bulk of fuel contamination occurs throughout the distribution process, particularly when using fuel tankers.
“Refineries don’t have control over the vehicle, how clean their tanks are or how their fuel or oil is handled,” notes FitzGerald.
Therefore, all areas of the distribution channel, from transportation to storage, require a greater level of understanding of the types of hydrocarbon contaminants, how they enter and how to eliminate them.
FitzGerald explains that factors such as the cleanliness of fuel trucks and the pipes used to transfer the fuel are significant in maintaining the cleanliness of the fuel.
ISO-Reliability Partners has found that the volume of the product impacts on the percentage of contaminants in the product.
For example, 500 mℓ of product has a significantly lower percentage of contaminants, compared to 5 ℓ of product, owing to the surface area of the container used for the product, as the container itself can have a layer of dust and other contaminants that mix with the product it contains.
Further, smaller containers are generally blow-molded on site prior to packaging, while steel drums are often left open for a time prior to the product being poured in.
For larger quantities of fuel, FitzGerald emphasises the importance of using high-efficiency breathers throughout the distribution network, along with circulating diesel through fine filter systems to ensure that the fuel is as clean as possible.
Bulk suppliers need to ensure that equipment is clean before it comes into direct contact with the fuel.
Prevention Tools
Breathers can ensure tankers are completely sealed, thus preventing contaminants in ambient air from entering the equipment; desiccant breathers can dry that air to ensure that moisture does not enter the product.
Breathers can also prevent contaminants within the 1 μm to 10 μm range from entering the equipment.
FitzGerald says that people are often unaware of this contaminant range because it is invisible to the eye, but these contaminants exist in significant quantities and can damage equipment when present in fuel.
Water moisture in air is also a significant contaminant. Diesel will absorb as much moisture as possible until it can no longer hold it in suspension. The moisture then agglomerates and sinks to the bottom as free water. South African standards allow for 300 mg of free water for every kilogram of product.
While a water trap can remove free water when transferring the diesel, the fuel is still saturated with water moisture. When the fuel goes through injectors, the water will become a superheated steam at the point of injection, which can quickly damage injectors.
FitzGerald highlights the importance of proper fuel storage in a temperature-controlled room and ensuring that anything that comes into direct contact with the fuel is clean and dry.
Even in a sealed container, temperature changes can cause contaminants to enter the fuel when ambient air is being pulled into the container and, when draining fuel from storage, ambient air is also pulled in. Therefore, proper filtration and storage are required to maintain optimal vehicle performance, he adds.
Long-term Damage
Contaminants in diesel can result in damage to equipment over time, resulting in costly repairs.
FitzGerald says contaminants erode injectors over time and, consequently, diesel droplets that are atomising in the combustion chamber are also getting bigger. This results in extended burn periods and elevated exhaust gas temperatures. There is not complete combustion of all the diesel entering the combustion chamber.
When the exhaust valve stem opens, it pushes that unburned diesel out of the exhaust in the form of black smoke.
FitzGerald says that the industry has placed a significant focus on removing sulphur, benzene and aromatics from fuel to reduce emissions and create a clean fuel, after combustion, however removing these from diesel results in it having less lubricity.
He explains that physical contaminants and their impact is often not taken into account when evaluating potential clean fuels and will, therefore, continue to damage equipment, which will be compounded by the lower lubricity.
This will then result in increased emissions, which is ultimately counter intuitive, he concludes.
Comments
Press Office
Announcements
What's On
Subscribe to improve your user experience...
Option 1 (equivalent of R125 a month):
Receive a weekly copy of Creamer Media's Engineering News & Mining Weekly magazine
(print copy for those in South Africa and e-magazine for those outside of South Africa)
Receive daily email newsletters
Access to full search results
Access archive of magazine back copies
Access to Projects in Progress
Access to ONE Research Report of your choice in PDF format
Option 2 (equivalent of R375 a month):
All benefits from Option 1
PLUS
Access to Creamer Media's Research Channel Africa for ALL Research Reports, in PDF format, on various industrial and mining sectors
including Electricity; Water; Energy Transition; Hydrogen; Roads, Rail and Ports; Coal; Gold; Platinum; Battery Metals; etc.
Already a subscriber?
Forgotten your password?
Receive weekly copy of Creamer Media's Engineering News & Mining Weekly magazine (print copy for those in South Africa and e-magazine for those outside of South Africa)
➕
Recieve daily email newsletters
➕
Access to full search results
➕
Access archive of magazine back copies
➕
Access to Projects in Progress
➕
Access to ONE Research Report of your choice in PDF format
RESEARCH CHANNEL AFRICA
R4500 (equivalent of R375 a month)
SUBSCRIBEAll benefits from Option 1
➕
Access to Creamer Media's Research Channel Africa for ALL Research Reports on various industrial and mining sectors, in PDF format, including on:
Electricity
➕
Water
➕
Energy Transition
➕
Hydrogen
➕
Roads, Rail and Ports
➕
Coal
➕
Gold
➕
Platinum
➕
Battery Metals
➕
etc.
Receive all benefits from Option 1 or Option 2 delivered to numerous people at your company
➕
Multiple User names and Passwords for simultaneous log-ins
➕
Intranet integration access to all in your organisation