Higher-quality lubrication reduces maintenance
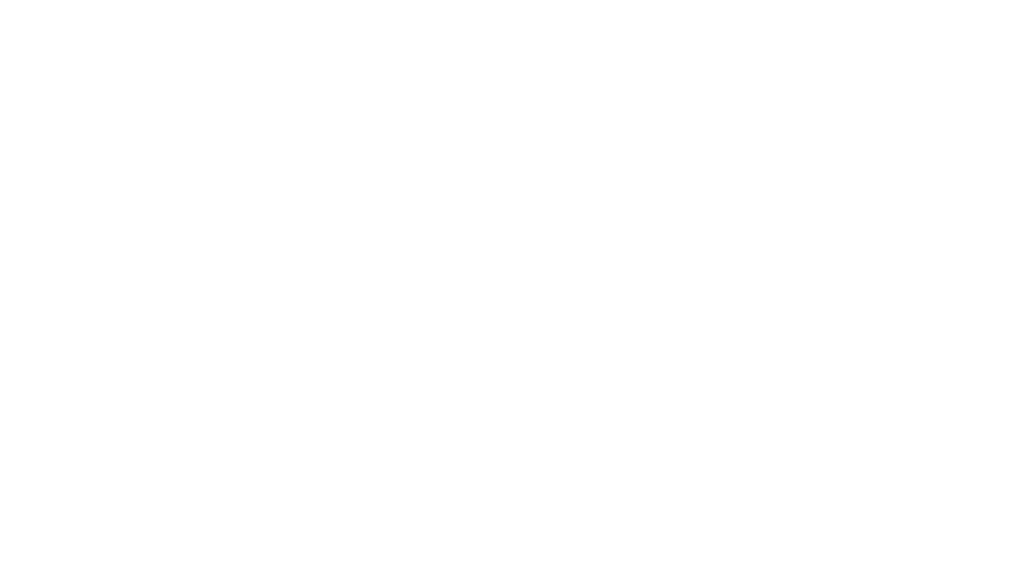
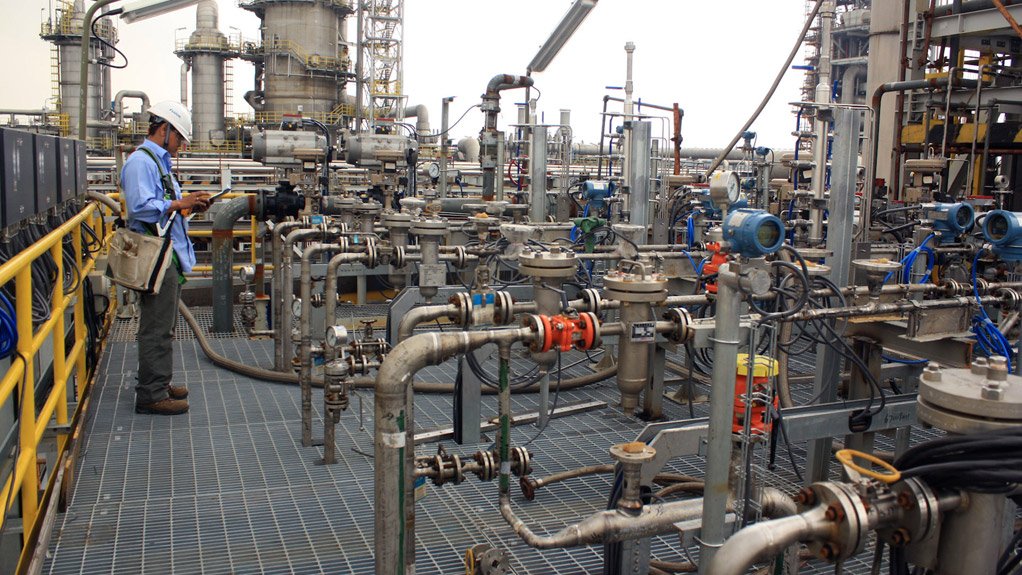
MAINTENANCE ACHIEVEMENT Many industries have reported a 2% to 10% productivity increase, owing to the correct use of predictive maintenance practices and use of correct lubrication
Wear control, lubrication and filtration company Filter Focus has assisted Germiston-based precious metals refiner Rand Refinery in significantly reducing its operational expenditure from R2.4-million to about R1-million in the past eight months by changing the refinery’s lubrication and filtration systems.
“Filter Focus assessed the refinery’s current equipment, drained, flushed and changed seals and bearings where required, and initiated a lubrication plan, Filter Focus technical manager Drew Leibbrandt tells Engineering News.
The company also monitored the impact of the process on the plant and equipment while executing an autolubricating plan and microfine filter systems for the hydraulics.
Currently, the refinery uses Lubrication Engineers (LE) Duolec (ISO 68, 320 and 460) oil, LE Monolec hydraulic oil and LE Almaguard multipurpose grease.
Since the introduction of the new oil, the refinery has moved from 80% red indicators of problem equipment to 98% green indicators of available equipment – a significant achievement in increased plant availability and equipment reliability – as well as reducing breakdowns and resulting maintenance, Leibbrandt says.
A key aim of Filter Focus is to highlight the importance of inherently high-quality lubrication, he stresses. Lubrication quality is inversely proportional to what is spent on maintenance. The higher the lubrication quality, the lower the expenses on maintenance, he points out.
“By increasing the lubrication quality, companies can reduce their maintenance schedules,” Leibbrandt adds, noting that the company has proven the effectiveness of these reductions through lubrication changes for several companies.
Filter Focus also assisted metal flow engineering company Vesuvius – after it had suffered a bearing failure three times in one week at its mill earlier this year – by converting its girth gear oil to Pyroshield gear oil.
Pyroshield is an oil-based product that contains almasol, an ingredient that reduces the friction coefficient on open gears.
Filter Focus also changed the entire lubrication system, sealed the bearings, refurbished the pumps feeding the mill, installed kidney filtration systems that recirculate and filtrate the oil on the lubrication tank and on the bearings, installed flow meters to measure the amount of lubrication oil needed for the oil and established a preventive maintenance plant for the mill.
“The lubrication is running according to the required specification for the first time,” Leibbrandt says, adding that, since Filter Focus completed the project in April, the mill has not shut down for maintenance yet.
While the company initially changed its mill bearings at three-monthly intervals, Filter Focus aims to have the bearings run for at least a year and, possibly, for a longer period before maintenance is required, Leibbrandt says.
Meanwhile, Filter Focus COO Craig FitzGerald points out that lubrication and filtration have been widely misunderstood or ignored for many years.
The notion that general lubricants and filtration systems supplied by the original-equipment manufacturer will adequately protect machinery is a general misconception, he adds.
FitzGerald explains that research done by Filter Focus found that improved lubrication quality and greater filtration efficiencies result in significant gains in total cost of ownership.
“The company has bridged this technology gap by designing and manufacturing specialist filtration systems that not only protect machine components from wear and failure but also enhance equipment reliability, availability and operating profits,” he adds.
The company further aims to grow market awareness through reliable engineering while closing the technology gap previously created by outdated operational and maintenance practices, FitzGerald says.
Leibbrandt notes that companies often focus on the 1% of lubrication cost savings by using lower-quality, cheaper bulk supply lubrication products, which might ultimately impact negatively on 99% of breakdown, labour and spare parts costs in operational expenditure, while continuous breakdowns and reactive maintenance exacerbate the lack of attention given to the type of lubrication used.
FitzGerald agrees, adding that, in a report released by the US-based Henniker Conference on national materials policy, machine wear and tear is listed as one of the three major technical areas affecting materials use and cost reductions.
FitzGerald notes that, taking the recommendations into consideration, it is difficult to believe that maintenance is still regarded as a high-expense factor and not one through which profits can be protected.
He adds that the cost of repairing machines
that fail in service is up to ten times more than the cost of anticipated and scheduled repair and maintenance.
Comments
Announcements
What's On
Subscribe to improve your user experience...
Option 1 (equivalent of R125 a month):
Receive a weekly copy of Creamer Media's Engineering News & Mining Weekly magazine
(print copy for those in South Africa and e-magazine for those outside of South Africa)
Receive daily email newsletters
Access to full search results
Access archive of magazine back copies
Access to Projects in Progress
Access to ONE Research Report of your choice in PDF format
Option 2 (equivalent of R375 a month):
All benefits from Option 1
PLUS
Access to Creamer Media's Research Channel Africa for ALL Research Reports, in PDF format, on various industrial and mining sectors
including Electricity; Water; Energy Transition; Hydrogen; Roads, Rail and Ports; Coal; Gold; Platinum; Battery Metals; etc.
Already a subscriber?
Forgotten your password?
Receive weekly copy of Creamer Media's Engineering News & Mining Weekly magazine (print copy for those in South Africa and e-magazine for those outside of South Africa)
➕
Recieve daily email newsletters
➕
Access to full search results
➕
Access archive of magazine back copies
➕
Access to Projects in Progress
➕
Access to ONE Research Report of your choice in PDF format
RESEARCH CHANNEL AFRICA
R4500 (equivalent of R375 a month)
SUBSCRIBEAll benefits from Option 1
➕
Access to Creamer Media's Research Channel Africa for ALL Research Reports on various industrial and mining sectors, in PDF format, including on:
Electricity
➕
Water
➕
Energy Transition
➕
Hydrogen
➕
Roads, Rail and Ports
➕
Coal
➕
Gold
➕
Platinum
➕
Battery Metals
➕
etc.
Receive all benefits from Option 1 or Option 2 delivered to numerous people at your company
➕
Multiple User names and Passwords for simultaneous log-ins
➕
Intranet integration access to all in your organisation